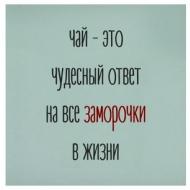
Operasi teknologi untuk air kemasan. Seleksi, pembenaran dan deskripsi skema teknologi untuk pembotolan bir. Mesin dengan satu kepala operasi pengisian
PENGANTAR…………………………………………………………………..
1. DESKRIPSI PROSES TEKNOLOGI………………
2. OTOMATISASI PROSES TEKNOLOGI……..
3. PEMROGRAMAN KONTROLER………………………………
KESIMPULAN………………………………………………………………
PENGANTAR
Otomatisasi manajemen adalah salah satu arah utama untuk meningkatkan efisiensi produksi. Lebih Yu.V. Andropov mencatat bahwa perlu untuk melakukan otomatisasi produksi, untuk memastikan meluasnya penggunaan komputer dan teknologi mikroprosesor.
Salah satu cara untuk meningkatkan efisiensi produksi energi adalah pengenalan teknologi komputer dalam sistem kontrol. Pengenalan luas dari sistem kontrol otomatis merupakan kebutuhan objektif, karena komplikasi tugas manajemen, peningkatan jumlah informasi yang perlu diproses dalam sistem manajemen.
Sampai saat ini, setiap perusahaan yang serius telah menerapkan sistem kontrol proses otomatis, dan sistem kontrol otomatis melakukan hingga 90% dari tugas perusahaan.
Dalam organisasi pemeliharaan proses teknologi, sistem kontrol lokal (lokal) untuk peralatan dan proses teknologi memainkan peran penting dan dirancang untuk mengontrol dan mengelola objek yang terpisah dan tidak terkait dan membentuk tingkat yang lebih rendah dalam sistem kontrol hierarkis. Sistem kontrol ini adalah loop tunggal dan untuk kontrol sinkron dari sistem seperti itu, dari sudut pandang saya, akan lebih baik menggunakan pengontrol dalam kontrol. Karena dengan sifat produksi yang berkelanjutan, tugas utama otomatisasi adalah pengaturan parameter secara otomatis, dan dalam produksi diskrit (seperti halnya dengan proses teknologi saya), kontrol logika perangkat lunak paling cocok. Dalam proses teknologi ini, perlu dicatat bahwa bengkel menghasilkan 5.000 botol air mineral per jam, dan penghitungan dan pendaftaran barang dengan bantuan orang yang bekerja.
Nala mungkin tidak selalu akurat. Perlu juga diperhatikan bahwa jika mesin pengisi tidak diatur dengan benar, dapat menyebabkan kerusakan produk (ledakan botol), untuk mengaturnya dengan cepat secara optimal, diperlukan informasi tentang indikator seperti tekanan di ruang mesin pengisi untuk periode tertentu. waktu (statistik dari waktu ke waktu), pencatatan informasi ini dengan bantuan personel yang bekerja tidak selalu memungkinkan dengan kualitas tinggi, dan dengan interval waktu yang singkat (langkah antar rekonsiliasi) hampir tidak mungkin. Juga, untuk alasan keamanan, karena proses teknologi ini ditandai dengan kelembaban tinggi, dan semua sistem kontrol dibangun di atas sirkuit listrik, perlu untuk meninggalkan metode pengontrolan TP tanpa kontrol. Oleh karena itu, saya menganggap perlu untuk memperkenalkan kontrol perangkat lunak-logis berdasarkan pengontrol dan perangkat lunak untuk itu ke dalam TP untuk pembotolan air mineral, yang akan menangani semua perhitungan, pendaftaran, pengukuran, dan pekerjaan melelahkan lainnya.
1. DESKRIPSI PROSES TEKNOLOGI
Diagram blok dari proses teknologi ditunjukkan pada Gambar 1.1 Untuk lebih jelasnya, saya telah membagi proses teknologi ini menjadi 10 bagian:
1. Bagian pertama adalah wadah air mineral impor (H-1 dan H-2). Jumlah kontainer adalah 2 buah 24 ton. Wadah ini dibawa keluar dari bengkel untuk tujuan keselamatan jiwa.
2. Bagian kedua adalah pompa listrik makanan A9-KNA (2 * 105? Pa), yang memompa air dari akumulator ke filter keramik F1 dan F2 (merek berarsir).
3. Pada bagian ketiga dari proses teknologi, saya menyertakan kompresor freon dan penyimpanan kapasitif H-3 untuk mendinginkan air yang dipompa melalui pompa sentrifugal TsN-1, yang berasal dari filter F1 dan F2, hingga suhu optimal +4 C untuk mencampur air mineral impor dengan karbon dioksida.
4. Bagian keempat termasuk instalasi di mana silinder karbon dioksida disuplai (tekanan dalam silinder adalah 70 MPa), silinder dihubungkan secara seri. Pasokan karbon dioksida diatur melalui peredam pneumatik, tekanan keluar untuk peredam pneumatik adalah 2MPa. Sensor aliran untuk kontrol visual juga disediakan.
5. Bagian kelima adalah saturator, di mana air mineral dicampur, dipompa dari tangki pendingin H3 menggunakan dua pompa sentrifugal TsN-2 dan TsN-3, dan karbon dioksida.
6. Bagian keenam termasuk mesin cuci botol AMMB untuk mencuci dan mendisinfeksi wadah. Untuk mencuci botol, air disuplai ke mesin di bawah tekanan P = 2 MPa; dalam jumlah F = 6m3?/menit. Di pintu keluar, layar cahaya disediakan untuk pemeriksaan visual kualitas wadah yang dicuci, yaitu di pintu keluar dari mesin cuci botol. Kualitas dalam hal ini adalah keutuhan botol dan kemurniannya.
7. Bagian ketujuh dari proses teknologi adalah monoblok penuangan, dapat dibagi menjadi tiga komponen:
Dosis - untuk pasokan sirup, jika air manis diproduksi;
Mesin pengisian otomatis untuk mengisi cairan di bawah tekanan, karena dalam proses teknologi ini pengisian ke dalam botol dilakukan bukan berdasarkan level (untuk setiap botol sejumlah air mineral tertentu), tetapi dengan rasio tekanan di ruang mesin pengisi dan tekanan dalam botol;
Mesin capping (merk UB) - untuk menutup botol dengan gabus timah.
8. Bagian kedelapan adalah mesin forwarding BA, berfungsi untuk mendeteksi cacat, kualitas disini adalah : capping botol harus dilakukan sedemikian rupa agar botol tidak retak dan harus ditutup rapat untuk mencegah degassing, seperti serta masuknya benda asing, seperti partikel kotoran, pecahan kaca dan sebagainya.
9. Yang kesembilan termasuk mesin pelabelan VEM 614, yang digunakan untuk pelabelan otomatis. Jika botol yang diisi telah melewati mesin penerusan, maka label yang sesuai dengan isi botol ditempelkan di atasnya. Dalam hal ini, label tidak boleh diberi selotip, tetapi dalam bentuk pra-potong.
10. Bagian kesepuluh adalah kemasan, seluruhnya diproduksi dengan bantuan tenaga kerja yang terdiri dari dua orang.
Dari satu bagian proses teknologi ke bagian lain, botol diumpankan oleh konveyor.
2. OTOMATISASI PROSES TEKNOLOGI
2.1. Deskripsi diagram fungsional yang diperluas dari otomatisasi pembotolan air mineral.
FSA diperpanjang ditunjukkan pada Gambar 2.2.
Dalam proses teknologi ini, skema pemblokiran, pensinyalan, dan perlindungan disediakan. Ketika level (posisi 1) mencapai level atas atau bawah di mesin pengisi PA, katup listrik (posisi 1) akan ditutup atau dibuka masing-masing.
Ketika level (posisi 2) mencapai bagian atas atau bawah di saturator, pompa sentrifugal (posisi 2) akan dimatikan atau dihidupkan, masing-masing.
Ketika level (posisi 3) mencapai level atas atau bawah di tangki pendingin H-3, pompa sentrifugal (posisi 3) akan dimatikan atau dihidupkan, masing-masing.
Ketika suhu (posisi 4) mencapai atas atau bawah di tangki pendingin H-3, katup listrik (posisi 4) akan ditutup atau dibuka masing-masing.
Kontrol kualitas dilakukan dalam kapasitas mesin pengisi RA (posisi 5).
3.2. Pilihan alat otomatisasi.
Untuk mengotomatisasi proses, perlu menggunakan sejumlah perangkat dan sensor transduser.
Kontrol suhu dilakukan menggunakan termokopel TKhK - 0179 (item 4-1). Untuk menghubungkannya, perlu untuk menormalkannya menggunakan konverter Sh-703 (posisi 4-2). Kesalahan dasar 0,53 – 1,35%.
Aktuator dikendalikan oleh tombol PKE - 212C (posisi 1-6, 1-7,2-6, 2-7, 3-6, 3-7, 4-6, 4-7). Dari panel kontrol operator melalui starter magnetik PME-011 (posisi 1-4, 1-5, 2-4, 2-5, 3-4, 3-5, 4-4, 4-5).
Dr-M (posisi 1-7, 4-8) digunakan sebagai mekanisme listrik eksekutif. Ini mulai bekerja menerima pulsa dari sensor, setelah itu melakukan pengujian sendiri dan secara otomatis berhenti setelah membuka atau menutup katup.
Untuk mengontrol kualitas air mineral, digunakan alat analisa konsentrasi DKB-1M (posisi 5-1), dengan sinyal keluaran yang dinormalisasi sebesar 0,5 mA.
Untuk mengontrol level, pengukur level LABKO - 2W digunakan (posisi 1-1, 2-1, 3-1). Sinyal keluaran dinormalisasi menggunakan konverter Sapphire-22DD (posisi 1-2, 2-2, 3-2).
3. PEMROGRAMAN KONTROLER.
Untuk pemahaman yang lebih baik tentang program ini, saya menyajikan algoritmenya:
Di sirkuit 1, 2, 3 (Gambar 2.2.), levelnya dipantau di mesin pengisi RA, saturator, tangki pendingin H-3.
Di sirkuit 4, suhu di tangki pendingin H-3 dipantau.
Kami menerima nilai berikut sebagai kombinasi kode:
Masukkan nilai level L1 dari RA |
||
L1=1 Pergi ke "Tutup slide pada katup (posisi 1-7)" |
||
L1 =0,5 m Pergi ke "Buka katup geser (butir 1-7)" |
||
Masukkan nilai level L2 dari saturator |
||
L2=2 m Pergi ke "Matikan pompa (butir 2-7, 2-8)" |
||
L2 =0,3 m Buka "Aktifkan pompa (butir 2-7, 2-8)" |
||
Masukkan nilai level L3 dari tangki pendingin H-3. |
||
L3=1.5m Pergi ke "Matikan pompa (butir 3-7)" |
||
L3 =0,2 m Pergi ke "Nyalakan pompa (butir 3-7)" |
||
Masukkan nilai level T dari RA |
||
T £ 4 0 C Pergi ke "Tutup slide pada katup (butir 4-8)" |
||
T > 4 0 C Pergi ke "Buka katup geser (butir 4-8)" |
||
Apakah ada sinyal keluar program? |
||
Jika ya, buka "Hentikan eksekusi program" |
||
Jika tidak, pergi ke awal program |
||
Tutup slide pada katup (posisi 1-7) |
||
Buka gate valve pada valve (posisi 1-7) |
||
Matikan pompa (butir 2-7, 2-8) |
||
Nyalakan pompa (butir 2-7, 2-8) |
||
Matikan pompa (butir 3-7) |
||
Nyalakan pompa (butir 3-7) |
||
Tutup katup gerbang pada katup (butir 4-8) |
||
Buka gate valve pada valve (posisi 4-8) |
||
Nilai tingkat keluaran L1 |
||
Nilai tingkat keluaran L2 |
||
Tampilkan nilai level L3 |
||
Suhu tampilan T |
||
KESIMPULAN
Tujuan dari kerja kursus ini adalah untuk mengembangkan perangkat lunak untuk pengontrol yang dapat diprogram untuk mengontrol proses pembotolan air mineral.
Skema teknologi pembotolan bir.
Antrean dimulai dengan pengiriman kotak dengan botol ke mesin pemecah kantong oleh penumpuk. Dari mesin pengemasan, kotak masuk ke mesin untuk mengekstraksi botol dari kotak. Botol yang diekstraksi pergi ke mesin cuci botol, di mana botol dicuci dan disuntikkan. Botol kemudian melewati layar cahaya untuk pemeriksaan akhir dari botol yang dicuci. Botol-botol yang diolah dengan air masuk ke mesin pengisian dan penutup. Untuk meningkatkan stabilitas bir, setelah pembotolan, botol dikirim untuk dipasteurisasi. Pasteurisasi dilakukan dalam pasteurizer terowongan. Setelah pasteurisasi, botol melalui mesin penolakan untuk memeriksa produk untuk cacat. Produk yang lolos penolakan dikirim ke mesin pelabelan. Botol-botol tersebut kemudian diumpankan ke mesin pengepakan botol. Saat pembotolan bir dengan kapasitas 12.000 botol per jam, setelah menempatkan botol di dalam kotak, pengemasan dalam film menyusut mengikuti.
Skema teknologi pembotolan dalam botol PET.
Botol PET tiba di pabrik dalam bentuk pertunjukan.). Selanjutnya, pertunjukan dimasukkan secara manual ke dalam mesin blow moulding otomatis. Kemudian pertunjukan yang dipanaskan melewati konveyor pelat ke mesin pembilasan tempat pertunjukan dibilas. Dari mesin pembilas, botol-botol itu tiba dengan cara yang kacau; untuk menempatkannya secara berurutan, botol-botol itu melewati mesin pengisi. Botol-botol PET yang berjejer diumpankan ke mesin capping. Conveyor capping terhubung ke mesin. Produk jadi pergi ke mesin pelabelan. Botol PET jadi pergi ke jalur pengemasan. Dan kemudian botol PET yang dikemas dikirim oleh penumpuk ke gudang produk jadi.
Skema teknologi pembotolan bir ke dalam tong.
Tong kosong diangkut dari gudang tara ke mesin cuci tong eksternal untuk menghilangkan kotoran. Kemudian, dari alat pencuci luar, tong-tong itu masuk ke dalam unit pencuci dan pengisian bagian dalam. Tong siap untuk kontrol pengisian dimasukkan ke timbangan otomatis.
2 Perhitungan produk pembuatan bir
Tabel 1 - Rangkaian produk
Tabel 2 - Distribusi bir menurut jenis dan jenis wadah
dalam botol | ||||||
Berezina | ||||||
Slutsk spesial. | ||||||
Zhigulevskoe spesial | ||||||
Bobruisk gelap |
Perhitungan produk dilakukan untuk 100 kg produk biji-bijian yang dikonsumsi untuk setiap jenis bir, diikuti dengan perhitungan ulang untuk 1 dal dan output tahunan.
Kirim karya bagus Anda di basis pengetahuan sederhana. Gunakan formulir di bawah ini
Mahasiswa, mahasiswa pascasarjana, ilmuwan muda yang menggunakan basis pengetahuan dalam studi dan pekerjaan mereka akan sangat berterima kasih kepada Anda.
Di-host di http://www.allbest.ru/
pengantar
Produksi penyulingan adalah salah satu cabang industri makanan, menyediakan produksi minuman beralkohol dan minuman beralkohol. Produksi modern vodka dan minuman beralkohol didasarkan pada penggunaan peralatan berteknologi tinggi dan canggih, bahan dan reagen baru. Penggunaan teknologi dan bahan baru yang memenuhi syarat membutuhkan pemahaman yang mendalam tentang proses fisikokimia disolusi, adsorpsi, difusi, dan proses penting lainnya yang terjadi selama transformasi bahan baku dan produk setengah jadi menjadi produk jadi.
Dalam beberapa tahun terakhir, telah terjadi perubahan besar dalam teknologi pengolahan air. Instalasi pengkondisian air osmosis balik banyak digunakan, tetapi penggunaannya memerlukan pendekatan yang berbeda untuk mengatur seluruh produksi secara keseluruhan, pengetahuan tentang esensi proses yang mendasari osmosis balik dan kemampuan untuk mengontrol proses ini.
Mencuci botol adalah kondisi yang diperlukan untuk memastikan kualitas produk, karena saat menggunakan kemasan yang dapat dikembalikan, botol dapat membawa label lama dan memiliki kontaminasi terus-menerus. Sebelum mencuci piring, mereka disortir tergantung pada tingkat kekotorannya. Biasanya botol yang kotor dikirim langsung ke mesin cuci botol. Botol yang terkontaminasi secara berlebihan sudah dicuci sebelumnya (direndam).
Botol polusi berlebih dikirim ke pra-pencucian, yang dibagi menjadi pencucian basa dan asam-basa.
Pencucian alkali adalah mencuci piring yang membutuhkan penggunaan larutan alkali konsentrasi tinggi, dilakukan pada mesin cuci botol dengan mode berikut:
Konsentrasi alkali di bak mandi adalah 3%;
Produktivitas mesin dibelah dua;
Jika ada pemandian kedua, suhunya akan tetap 70-80 °C;
Jarum suntik dan pencucian luar botol dilakukan dengan air pada suhu 40-45 ° C;
Piring terkontaminasi yang sudah dicuci sebelumnya dikirim ke mesin untuk dicuci secara teratur.
Pencucian asam-basa. Untuk piring yang sangat kotor (endapan garam, cincin di dinding, dll.), yang harus diolah sebelumnya dengan asam, serta untuk kontaminasi yang memerlukan perawatan dengan alkali konsentrasi tinggi (residu lemak, dll.), asam pendahuluan manual -pemrosesan dasar di bak cuci khusus atau perangkat lain. Piring yang sangat kotor dicuci di ruang terpisah, diisolasi dari toko cuci dan pembotolan. Pada saat yang sama, perlu untuk mematuhi peraturan keselamatan yang disediakan saat bekerja dengan asam dan alkali.
Tergantung pada jenis kontaminasi, botol diperlakukan dengan larutan soda abu atau asam klorida menggunakan ruff.
1. Bagian teknologi
Seleksi, pembenaran dan deskripsi skema teknologi.
Vodka dan minuman beralkohol lainnya dituangkan ke dalam botol kaca. Proyek kursus ini menyajikan skema yang baik untuk memurnikan air untuk mencuci botol dengan kemungkinan digunakan kembali. Air adalah produk yang sangat mahal untuk bisnis, sehingga dapat digunakan kembali akan sangat mengurangi biaya keuangan. Keuntungannya juga otomatisasi penuh dari proses pencucian, pemurnian air dan regenerasi deterjen.
Air dari suplai air diarahkan ke saringan pasir (1), kemudian ke saringan mikro (2) "AQUA-elektronik". Dengan bantuan filter ini, air dibebaskan dari suspensi dan garam besi. Setelah pra-perawatan, air masuk ke pengumpul air (16). Jika perlu, aditif penstabil disuplai ke dalamnya dengan bantuan pompa dosis (15) - larutan encer asam sulfat dari tangki (13) dan polifosfat dari tangki (14). Untuk kemudahan penggunaan, larutan reagen disiapkan sekali sehari. Selanjutnya, air diolah dalam unit bakterisida (17) dan dikirim ke kolektor penyimpanan (18), dari mana air dipompa melalui sistem akumulator hidrolik (19) menggunakan tiga pompa pendorong tekanan tinggi (20) ke dalam kaskade perangkat reverse osmosis (21).
Kualitas air yang dimurnikan dikendalikan oleh pengukur garam (23), dan kuantitasnya dikendalikan oleh pengukur aliran (22). Dengan bantuan pompa (6), air yang dilunakkan dikirim ke tangki tekanan (7). Air yang diperoleh dengan metode di atas memiliki indikator berikut: kesadahan total 0,02-0,22 mg * eq / dmi, alkalinitas 0,16-0,3 mol / dmi, kemampuan oksidasi 0,2-1,5 mg O2 / dmi, kandungan mikronutrien rendah.
Pabrik reverse osmosis beroperasi pada air dengan kandungan garam hingga 0,5 g/dm³. Saat menggunakan instalasi persiapan air awal, itu tidak diperlukan. Ketika kandungan garam dari 0,5 sampai 30 g/m3 dan lebih tinggi, serta ketika kekeruhan air lebih dari 1,5 mg/dm3, mikrofiltrasi, ultrafiltrasi dan kationisasi Na harus dilakukan sebelum pengolahan air reverse osmosis.
Cara yang lebih mudah untuk mengolah air adalah Na-kationisasi. Dengan kesadahan total air yang tinggi, dilengkapi dengan melewati filter (1), (2) dan filter penukar Na-kation (4). Regenerasi filter Na-kationit dilakukan dengan larutan garam yang dipasok dari pelarut garam (3). Air lunak dikumpulkan dalam kolektor (5), setelah itu dikirim ke tangki tekanan (7), dan kemudian diproses sesuai dengan metode yang dijelaskan sebelumnya. Air ini diperlukan untuk membilas botol di mesin cuci botol.
Peti dengan botol kotor datang dari gudang ke pengekstrak botol (24). Kotak dengan botol diumpankan ke mesin dan berhenti di bawah kepala dengan gripper. Kemudian kepala turun ke dalam kotak dan meraih leher botol, bangkit dan membawa botol ke meja. Peti kosong bergerak lebih jauh di sepanjang konveyor, tempatnya diambil oleh peti berikutnya.
Melalui konveyor pelat (25), botol diarahkan ke pencuci botol (26) dengan larutan basa yang berasal dari tangki (10). Di mesin cuci botol, botol baru hanya dibilas, dan botol yang bersirkulasi sudah dibersihkan sebelumnya, dan kemudian dicuci di mesin dengan air dingin dan hangat, larutan alkali. Natrium hidroksida, natrium karbonat, trisodium fosfat, sulfosalt, dll digunakan sebagai deterjen. Konsentrasi larutan alkali untuk mesin cuci manual dan semi-otomatis adalah 1,0-3,0%, untuk mesin otomatis - 1,8-2,0%, suhu larutan tidak boleh lebih rendah dari 80 °C.
Larutan alkali disiapkan dalam tangki pencampur (10), di mana melalui meter (9) langsung dari truk tangki melalui pompa (6) alkali dan air dari kolektor (8) disuplai. Anda juga dapat menggunakan larutan bekas untuk mencuci. Untuk melakukan ini, dari mesin cuci botol melalui pompa (6), larutan alkali pertama-tama memasuki filter keramik (12), dan kemudian ke kolom regenerasi (11). Setelah kolom, alkali memasuki tangki pencampur (10) melalui pompa (6).
Efluen dari mesin cuci botol dikirim untuk diolah. Pertama, efluen mengalir secara gravitasi ke pengumpul air limbah (27). Setelah itu, pompa (6) menuju ke bak (28), di mana ia mengendap dari partikel tersuspensi. Dari sana, air yang mengendap melewati pompa (6) ke saringan pasir (29), di mana pemurnian akhir terjadi, setelah itu air murni dipompa (6) ke tangki air murni (8).
Persyaratan untuk bahan baku, bahan penolong dan produk jadi
Air minum GOST 51232-98
Persyaratan kualitas air menurut SaNPiN 2.1.4.1074-01
Produk jadi:
Botol kaca GOST 10117-91
Gabus mahkota GOST 10167-88
Karbon dioksida GOST 8050-85
Label GOST 16 353
Lem dekstrin GOST 7699
Deterjen dan desinfektan GOST 5100
Etil alkohol GOST R52522-2006
Vodka GOST R51355-1999
1. Vodka dan vodka khusus harus disiapkan sesuai dengan persyaratan standar ini sesuai dengan peraturan teknologi, instruksi untuk produksi vodka dan vodka khusus dan resep sesuai dengan standar sanitasi dan aturan yang disetujui dengan cara yang ditentukan.
2. Tergantung pada rasa dan sifat aromatik, kandungan bahan vodka dibagi menjadi vodka dan vodka khusus.
3. Dari segi sifat organoleptik, vodka dan vodka khusus harus memenuhi persyaratan:
Karakteristik: cairan transparan tanpa inklusi dan sedimen asing
Warna: cairan tidak berwarna
Rasa dan aroma: khas untuk vodka jenis ini, tanpa rasa dan aroma asing. Vodka harus memiliki rasa ringan yang melekat pada vodka dan aroma vodka yang khas; vodka khusus - rasa ringan dan aroma spesifik yang ditekankan.
Tabel 1.
Meja 2.
Kontrol teknokimia dan mikrobiologis produksi
Kontrol teknokimia sangat penting dalam industri minuman beralkohol, yang menghasilkan berbagai macam minuman keras, minuman keras, tincture dan vodka berkualitas tinggi dari bahan baku berharga - etil alkohol, bahan baku nabati dan produk makanan (gula, minyak esensial, dll.) . Kontrol teknokimia ditujukan untuk meningkatkan kualitas produk, pengenalan teknologi rasional, kepatuhan terhadap norma konsumsi bahan baku dan bahan, mengurangi kerugiannya.
Kontrol teknokimia adalah seperangkat indikator yang mencirikan komposisi kimia dan parameter fisikokimia bahan baku, produk setengah jadi, bahan penolong yang digunakan dalam produksi produk jadi, serta menetapkan identitas hasil yang diperoleh dengan nilai dari standar yang relevan. Kontrol teknokimia menyediakan penentuan seperangkat indikator yang memberikan informasi lengkap tentang kualitas produk berdasarkan analisis yang dilakukan dan data alat ukur kontrol. Salah satu tugas utama yang dihadapi oleh layanan kontrol teknokimia adalah untuk mengontrol kemajuan proses teknologi, kualitas bahan baku dan produk jadi. Produk berkualitas tinggi hanya dapat diperoleh dengan menggunakan bahan baku, yang kualitasnya memenuhi persyaratan yang diperlukan, dan dengan memperhatikan rezim teknologi yang optimal untuk produksi produk akhir. Bahkan penyimpangan terkecil dalam kualitas bahan baku dan pelanggaran dalam rezim teknologi mengarah pada pelepasan produk jadi berkualitas rendah atau pernikahan. Penyimpangan ini terungkap hanya dengan bantuan kontrol teknokimia. Kontrol teknokimia di perusahaan harus memastikan kepatuhan terhadap rezim teknologi resep, kontrol kualitas bahan baku, produk setengah jadi dan produk jadi sesuai dengan standar dan spesifikasi.
Kaitan penting dalam melakukan pengendalian teknokimia adalah metode analisis itu sendiri, yang harus memberikan hasil yang akurat dan dapat diandalkan. Berdasarkan hasil tersebut, dimungkinkan untuk mengembangkan dan menyempurnakan rezim teknologi, menguraikan cara untuk menghilangkan kekurangan dan kerugian dalam produksi, dan mencegah pelepasan produk berkualitas rendah. Kontrol semacam itu bisa menjadi yang paling efektif, karena kontrol teknokimia berfungsi tidak hanya untuk mendeteksi cacat pada produk jadi, tetapi juga untuk mencegahnya, serta untuk menghilangkan situasi yang menyebabkan cacat pada semua tahap proses produksi.
Tabel 3. Kontrol teknokimia
Tabel 4. Pengendalian Mikrobiologi
akuntansi produksi
Dalam proses produksi vodka, minuman beralkohol, dan minuman berkarbonasi rendah alkohol, mereka mencatat bahan utama, bahan tambahan, dan produk jadi.
Konsumsi bahan baku ditentukan dengan mempertimbangkan resep, instruksi teknologi, dan juga dengan mempertimbangkan kerugian_produksi yang tak terhindarkan.
Norma kerugian produksi tergantung pada teknologi, peralatan yang digunakan, kondisinya, disiplin produksi dan faktor lainnya. Tingkat kerugian diatur pada berbagai tahap produksi dan diperiksa ulang_setidaknya_1_waktu_dalam_5_tahun.
Akuntansi_vodka.
Solusi air-alkohol di departemen pemurnian dan vodka jadi diperhitungkan berdasarkan volume dan kandungan alkohol anhidrat di dalamnya. Produk jadi, mis. dikemas dalam botol, didekorasi dan dikemas dalam kotak bergelombang, diukur dan dinyatakan dalam dekaliter.
Produk jadi yang ditransfer ke ekspedisi, serta dilepaskan ke jaringan distribusi, diperhitungkan oleh jumlah kotak, jumlah botol, dan akhirnya_in_dekalitre.
Untuk menghitung botol dan kotak di pabrik, alat penghitung digunakan, terutama dari jenis elektrokontak.
Alkohol_inventaris.
Saat menginventarisasi alkohol di tempat industri, volume alkohol dalam tangki pengukur dan tangki lainnya ditentukan sesuai dengan pembacaan pengukur level. Selain itu, setiap peti kemas harus memiliki sertifikat verifikasi Negara dengan cara yang ditentukan. Secara bersamaan mengukur kekuatan dan temperature_of_alcohol_in_each_reservoir.
Jumlah produk setengah jadi (jus beralkohol, minuman buah, infus, roh aromatik), larutan air-alkohol, vodka, minuman beralkohol dan minuman berkarbonasi rendah alkohol dalam tangki, perkawinan yang dapat diperbaiki dan tidak dapat diperbaiki ditentukan dengan pembacaan gelas ukur di dekaliter dan sekaligus mengukur suhu cairan, mengambil sampel untuk penentuan benteng dari setiap wadah.
Di departemen vodka, jumlah larutan air-alkohol dalam filter diperhitungkan, dan jumlah cairan yang mengandung alkohol dalam komunikasi ditunjukkan. Perhitungan alkohol dalam komunikasi dan baterai filtrasi dilakukan sesuai dengan tindakan keberadaan alkohol dalam peralatan.
Dalam kasus luar biasa, cairan air-alkohol dikeringkan dari equipment_and_measured.
Saat menentukan alkohol anhidrat dalam produk setengah jadi atau produk jadi dengan kandungan ekstraktif yang signifikan pada suhu di atas atau di bawah 20ºC, volume produk dikurangi menjadi 20ºC. Membawa volume ke 20 ° C dilakukan sesuai dengan tabel khusus, yang memperhitungkan ekspansi volumetrik produk, tergantung pada kandungan ekstraktif dan alkohol di dalamnya. Jumlah alkohol anhidrat ditemukan dengan mengalikan kekuatan pada 20ºC dengan volume produk, dikurangi menjadi 20ºC.
Akuntansi untuk alkohol dan gula dilakukan untuk mengontrol proses teknologi, untuk menghemat sumber daya material dan untuk tujuan_pelaporan_penuh.
2. Perkiraan bagian
resep mikrobiologi mentah vodka
Perhitungan produk
Resep vodka "Michurinskaya":
alkohol diperbaiki "Ekstra",
air lunak,
apel 3kg,
wortel - 0,82 kg,
gula - 6 kg.
Perhitungan didasarkan pada 1000 produk yang diberikan.
Tabel 5
Menurut norma yang dikonfirmasi oleh Kementerian Perindustrian Pangan, kerugian diterima:
Alkohol 0,94%,
Perkawinan yang dapat dikoreksi 1,7%,
Pernikahan yang tidak dapat diperbaiki 0,7%.
Perhitungan jumlah alkohol
Untuk menentukan jumlah alkohol yang dikonsumsi untuk persiapan vodka ini, perlu diperhitungkan kerugiannya yang tidak dapat diperbaiki selama persiapan penyortiran, pemrosesan dengan karbon aktif, penyaringan, dan pembotolan. Kerugian ini dihitung sebagai persentase dari jumlah alkohol yang memasuki produksi. Kami menerima nilai kerugian alkohol berikut.
Tabel 6
Untuk persiapan vodka jenis ini, kami mengambil alkohol yang diperbaiki, diproduksi dari bahan baku biji-bijian kentang, dengan kekuatan 96,4%. Konsumsi alkohol anhidrat untuk persiapan penyortiran 1000 dal, dengan mempertimbangkan kekuatan dan kerugian dalam produksi, akan
V = = 403,76 memberi
Konsumsi roh yang diperbaiki "Ekstra" dengan kekuatan 96,4% vol.
V = = 418,84 memberi
Perhitungan jumlah air yang dikoreksi.
Mempertimbangkan kontraksi campuran alkohol - air untuk mendapatkan 40% vol. penyortiran ke 100 memberi alkohol dengan kekuatan 96,4% vol. konsumsi air akan 142,2 memberi. Untuk 1000 produk yang diberikan, konsumsi airnya adalah:
V air = = 595,59 dal
Perhitungan kuantitas penyortiran.
Jumlah penyortiran yang disiapkan lebih besar dari jumlah vodka yang diterima, karena sebagian dikembalikan untuk persiapan penyortiran berikutnya, sebagian hilang saat mencuci filter dan kolom batubara, dan selama regenerasi dikembalikan dalam bentuk perkawinan yang tidak dapat diperbaiki. Nilai kerugian diambil sebesar 1,7% dari jumlah total produksi. Selain itu, kerugian penyortiran terjadi dengan memo buruk, yang tidak dapat digunakan kembali. Dengan mempertimbangkan kerugian ini, volume penyortiran akan menjadi:
kelas V. = = 1033,4 memberi,
di mana: 1,7 - nilai pernikahan yang dapat diperbaiki%,
0,7 - nilai pernikahan yang tidak dapat diperbaiki%,
Volume pernikahan yang dapat dikoreksi
V ISP.br. = = 17 memberi
V rusak br. = = 7 memberi
Jika kita memperhitungkan hilangnya vodka di toko pembersih dan menganggap bahwa toko pembotolan menghasilkan semua cacat yang tidak dapat diperbaiki dalam jumlah 0,5% dari total volume produksi, maka volume vodka dalam tong yang dibawa adalah:
V==1015 memberi
Tabel 7. Tabel ringkasan konsumsi bahan baku per 1000 produk yang diberikan
Produk |
Satuan |
Kuantitas Produk |
||
Alkohol yang diperbaiki |
||||
air reklamasi |
||||
Penyortiran |
||||
Pernikahan yang dikoreksi |
||||
Pernikahan yang tidak dikoreksi |
||||
Vodka dalam tong |
||||
Tabel 8 Ringkasan meja produk
Produk |
satuan pengukuran |
Ukuran produk |
||||
Alkohol yang diperbaiki |
||||||
air reklamasi |
||||||
Penyortiran |
||||||
Pernikahan yang dikoreksi |
||||||
Pernikahan yang tidak dikoreksi |
||||||
Vodka dalam tong |
||||||
Perhitungan dan pemilihan peralatan
Untuk memilih peralatan untuk skema teknologi ini, Anda perlu menghitung jumlah botol yang diproduksi per jam, yaitu:
a \u003d 10 * 1900000 * 1,02 * 0,3 / 21 * 3 * 8 * 2 * 0,9 * 0,5 \u003d 12817 botol / jam
Kami memilih 2 jalur dengan kapasitas 6.000 botol per jam
Perhitungan energi
Tabel 9. Perhitungan konsumsi listrik
Tabel 10 Perhitungan konsumsi uap
Tabel 11 Perhitungan konsumsi air.
Tabel 12 Perhitungan konsumsi udara terkompresi
Tabel 13 Ringkasan tabel perhitungan energi
3. Perlindungan tenaga kerja
Zat berbahaya dan berbahaya utama dalam industri alkohol dan minuman beralkohol adalah bahan baku curah, karbon dioksida, alkohol dan alkali, dan area berbahaya adalah peralatan teknologi yang beroperasi di bawah tekanan.
Untuk menciptakan kondisi kerja yang sehat dan aman dalam produksi, semua peralatan teknologi dan proses teknologi harus memenuhi persyaratan keselamatan.
Di toko perkakas, perlu untuk mematuhi persyaratan Aturan saat menyimpan kotak.
Saat menumpuk dengan tangan, peti dengan barang pecah belah harus ditumpuk dalam tumpukan tidak lebih dari 2m. Bagian utama antara tumpukan harus memiliki lebar minimal 2m.
Suhu botol yang masuk ke mesin cuci botol harus minimal 10°C.
Mesin cuci botol harus ditempatkan di lantai bawah. Dalam hal menempatkan mesin cuci botol di lantai 2, perlu dilakukan tindakan anti air dari kemungkinan kebocoran cairan pencuci melalui lantai.
Penyimpanan asam dan alkali pekat di ruang cuci dilarang.
Mesin cuci botol harus memiliki interlock untuk menonaktifkan drive dalam kasus berikut:
Saat memuat atau mengganggu konveyor pembawa botol;
Saat mengganggu benda kerja untuk memuat dan menurunkan botol;
Dalam hal kehilangan botol yang tidak lengkap dari sarang pembawa botol;
Saat meluap dengan botol konveyor outfeed;
Dengan penurunan tekanan di jaringan pasokan air di saluran masuk ke mesin dan perubahan suhu cairan pencuci.
Mengisi bak mesin pencuci botol dengan larutan pencuci dan memuat kaset dengan botol harus dimekanisasi. Larutan pembersih harus disiapkan di ruangan terpisah. Dimungkinkan untuk mengeluarkan botol yang pecah dari bagian kerja mesin hanya dengan perangkat khusus (pengait, penjepit, dll.)
Kulet yang terbentuk selama pengoperasian mesin harus dilepas hanya setelah mesin berhenti dan tidak boleh menumpuk di dekat peralatan.
4. Sanitasi industri
Tugas utama sanitasi industri adalah untuk mencegah efek buruk dari faktor-faktor produksi berbahaya yang bekerja untuk memastikan kondisi kerja yang aman, menghilangkan penyebab morbiditas terkait pekerjaan dan produksi, serta kelelahan dini.
Di perusahaan makanan, faktor-faktor yang mempengaruhi fungsi sistem pernapasan, sistem peredaran darah, sistem saraf, organ penglihatan dan pendengaran terutama dianggap berbahaya.
Zat berbahaya
Zat berbahaya utama yang mencemari udara di perusahaan makanan adalah debu yang berasal dari organik dan mineral, berbagai gas dan uap yang dihasilkan selama pemrosesan bahan baku, bahan awal, pembuatan produk antara, produk, dan yang terkandung dalam limbah produksi. Debu, gas, dan uap berbahaya yang masuk ke tubuh manusia dalam jumlah kecil melalui organ pernapasan, pencernaan, atau kulit memiliki efek toksik atau patogen yang merugikan, mengganggu fungsi fisiologis organ, sistem, atau menyebabkan berbagai penyakit.
Bagian utama zat berbahaya memasuki tubuh manusia melalui organ pernapasan, yang melakukan salah satu fungsi utama pendukung kehidupan manusia - memasok oksigen ke seluruh tubuh.
Untuk mencegah konsekuensi yang merugikan, serta mati lemas karena kekurangan oksigen, udara yang digunakan untuk bernapas harus memenuhi persyaratan sanitasi dan higienis untuk kandungan komponen utamanya dan kotoran berbahaya.
Dari gas dan uap berbahaya, yang paling berbahaya adalah karbon monoksida dan dioksida, sulfur dioksida, nitrogen oksida, uap alkohol, esens makanan, asam, alkali, dll.
Tindakan perlindungan kolektif terhadap zat berbahaya
Di perusahaan makanan, untuk mencegah dampak zat berbahaya pada manusia, serangkaian tindakan perlindungan kolektif digunakan, yang dapat dibagi menjadi: teknologi, tugas utamanya adalah mencegah pelepasan zat berbahaya ke tempat produksi; teknis, yang dirancang untuk menjaga MPC zat berbahaya di tempat; tindakan medis dan pencegahan terdiri dari pemantauan klinis sistematis terhadap keadaan kesehatan pekerja; pengendalian meliputi penilaian kandungan uap, gas, dan debu berbahaya di udara.
Iklim mikro di tempat kerja
Iklim mikro tempat industri adalah kondisi meteorologi lingkungan internal, ditentukan oleh kombinasi suhu, kelembaban relatif dan kecepatan udara yang bekerja pada tubuh manusia, serta radiasi termal dan suhu permukaan struktur penutup dan peralatan teknologi.
Indikator iklim mikro: suhu (°С), kelembaban relatif (%), kecepatan udara (m/s) dan intensitas radiasi termal (W/m²) - memiliki nilai absolut dari nilai optimal dan yang diizinkan.
Kebisingan dan getaran industri
Peralatan teknologi perusahaan makanan adalah sumber kebisingan dan getaran. Kebisingan dan getaran, sebagai iritasi biologis, menyebabkan penyakit umum pada tubuh manusia.
Kesesuaian tingkat kebisingan dan getaran di tempat kerja dengan persyaratan standar keselamatan ditetapkan dengan membandingkan parameter yang diukur dengan standar sanitasi.
Karena getaran dan kebisingan paling sering saling terkait, disarankan untuk mengklasifikasikan tindakan perlindungan kolektif terhadapnya sebagai tindakan perlindungan vibroakustik. Langkah-langkah ini dibagi menjadi: organisasi, yang terdiri dari pengecualian peralatan vibroacoustic aktif dari skema teknologi, penggunaan peralatan dengan beban dinamis minimal, operasi yang benar, dll.; yang teknis dibagi menjadi dua kategori: yang menghilangkan kebisingan dan getaran pada sumber kemunculannya dan mengurangi intensitas getaran dan kebisingan ke tingkat standar sanitasi; bangunan dan langkah-langkah perencanaan termasuk perencanaan penempatan peralatan untuk mengurangi dampaknya terhadap manusia.
Perlindungan individu berarti
Berdasarkan penunjukan, alat pelindung diri dibagi menjadi alat pelindung diri dan alat pengaman; sarana perlindungan sanitasi dan sarana tugas.
Alat pelindung diri dan perangkat keselamatan dirancang untuk mencegah atau mengurangi paparan faktor produksi berbahaya dan berbahaya ke tingkat yang disyaratkan. Mereka digunakan ketika sarana perlindungan kolektif tidak memberikan keamanan yang lengkap, penggunaannya secara teknis atau ekonomis tidak praktis atau tidak mungkin dalam kondisi khusus ini.
Selain APD, para pekerja bisnis makanan yang bersentuhan langsung dengan produk makanan juga dilengkapi dengan alat pelindung diri sanitasi, yang dirancang untuk melindungi produk makanan dari infeksi dan kontaminasi.
Alat pelindung diri yang bertugas dirancang untuk melindungi pekerja saat melakukan perbaikan mendesak, menghilangkan konsekuensi kecelakaan atau untuk bekerja dalam situasi yang tidak terduga.
Kesimpulan
Dalam proyek kursus ini, skema departemen pencucian dipertimbangkan, yang menyediakan pemurnian lengkap air bekas dengan kemungkinan penggunaan kembali. Berkat kemungkinan ini, biaya ekonomi air berkurang, karena. air untuk produksi adalah produk yang sangat mahal.
literatur
1. I.I. Burachevsky dan lainnya "Produksi vodka dan minuman".
2. Faradzhev "Teknologi umum".
3. V.E. Balashov "Desain tingkat perusahaan
4. Kovalevsky "Teknologi produksi fermentasi", 2004.
5. V.S. Nikitin, Yu.M. Burashnikov "Perlindungan tenaga kerja di industri makanan", Moskow: "Kolos", 1996.
Diselenggarakan di Allbest.ru
Dokumen serupa
Pengembangan skema teknologi untuk pembotolan bir. Persyaratan untuk bahan baku, bahan penolong dan produk jadi. Pengendalian teknokimia dan mikrobiologi. Bahan baku yang digunakan untuk produksi bir "Moskow". Persyaratan sanitasi untuk peralatan.
makalah, ditambahkan 03/01/2015
Metode untuk mendapatkan alkohol. Diagram skematis produksi vodka. Metode persiapan campuran air-alkohol dan penyaringannya. Evaluasi kualitas minuman beralkohol: prosedur mencicipi, menghitung produk jadi, penyimpanan dan pelepasannya.
laporan latihan, ditambahkan 15/01/2008
Persiapan air untuk produksi penyulingan. Skema teknologi utama untuk mendapatkan vodka. Pencampuran minuman, penyaringan bertingkat minuman beralkohol. Teknologi untuk produksi cuka makanan. Produksi karbon dioksida padat.
tutorial, ditambahkan 02/09/2012
Studi tentang metode pemurnian vodka modern dari kotoran dan dampaknya terhadap kualitas produk jadi. Pengembangan teknologi untuk produksi vodka menggunakan penyaringan perak di perusahaan OAO "Sibir". Efisiensi ekonomi produksi.
makalah, ditambahkan 10/03/2014
Deskripsi proses teknologi produksi vodka, bahan baku dan bahan. Klasifikasi dan karakteristik organoleptik vodka. Desain otomatisasi untuk sistem kontrol pompa dan stabilisasi suhu di departemen pencampuran di CJSC MPBK "Ochakovo".
tesis, ditambahkan 12/02/2012
Proses teknologi produksi vodka pada contoh CJSC MPBK "Ochakovo". Peran departemen pencampuran dalam produksi vodka. Skema mnemonik wadah alkohol dan peralatan pompa. Efisiensi ekonomi dari otomatisasi proses produksi.
tesis, ditambahkan 09/04/2013
Struktur kepengurusan SOJSC "BAKHUS". Teknologi untuk produksi alkohol dan vodka. Pembotolan, pengemasan dan penyimpanan produk jadi. Peralatan teknologi untuk transportasi bahan baku dan produk jadi, kontrol kualitas. Tenaga kerja dan perlindungan lingkungan.
laporan latihan, ditambahkan 27/10/2009
Karakteristik bagian-bagian penyusun bahan baku. Termasuk dalam penyortiran bahan. Pengolahan campuran air-alkohol dengan karbon aktif. Deskripsi skema teknologi untuk produksi vodka "mata air emas". Perhitungan neraca bahan dan tong pemilahan.
makalah, ditambahkan 04/05/2009
Berbagai macam dan nilai gizi keju. Persyaratan dasar untuk bahan baku untuk produksinya. Seleksi, pembenaran dan deskripsi skema teknologi produksi. Perhitungan pemilihan dan tata letak dan penempatan peralatan. Kontrol teknokimia produksi.
makalah, ditambahkan 27/10/2013
Menyusun program produksi perusahaan. Pemilihan skema teknologi untuk lini produksi vodka dan minuman. Indikator organoleptik produk. Perhitungan produk, peralatan, wadah dan bahan pembantu. akuntansi dan kontrol produksi.
Proses teknologi pembotolan bir.
Deskripsi skema teknologi pengisian ke dalam botol PET
Preforms pada palet dikirim ke mesin blow moulding oleh truk forklift. Mesin memiliki sistem pengumpanan dan sistem penyortiran bentuk awal. Dengan bantuannya, bentuk awal dibagi menjadi 16 cetakan, di mana botol ditiup menggunakan kompresor udara bertekanan tinggi dan oven radiasi inframerah. Mobil memiliki kendali atas botol, pernikahan dikesampingkan.
Setelah mesin blow moulding, botol-botol dipindahkan di sepanjang jalur yang disebut konveyor udara.
Konveyor adalah struktur baja berkualitas tinggi dengan bagian gantung untuk mentransfer botol PET kosong dari mesin blow moulding.
Konveyor udara membawa botol PET dari mesin blow moulding ke mesin pembilas otomatis. Bantuan bilas bekerja berdasarkan prinsip sirkulasi. Botol dengan bantuan auger diumpankan ke bintang utama mesin. Di pintu masuk ke mesin ada kontrol untuk botol yang dijatuhkan atau botol berdiameter besar. Ketika interlock dipicu, mesin berhenti. Bintang terkemuka memandu botol ke gripper khusus yang mencengkeram lehernya. Kemudian, dengan bantuan cam, botol diputar 180 ° dan nozel, berputar selaras dengan gripper, mulai menyemprot. Bintang di pintu keluar bergerak selaras dengan tangkapan, mengeluarkan botol. Pembilas saluran masuk dilengkapi dengan sensor untuk mengenali botol yang rusak.
Setelah dibilas, botol dipindahkan ke pembotolan dengan menggunakan bintang.
Sistem tiga ruang dengan kontrol elektronik. Mengisi isobarik, di bawah tekanan. Botol ditekan dengan kuat pada katup pengisian dengan bantuan pengangkat. Ada empat langkah dalam proses pembotolan:
tekanan udara;
pemerataan tekanan dan pengisian botol dengan produk;
mengatur tingkat minuman dan menghentikan proses pembotolan;
menghilangkan tekanan berlebih.
Sebuah foamer dipasang antara mesin pengisi dan capper untuk mengeluarkan udara dari botol. Busa berbutir halus naik ke leher botol dan menggantikan udara.
Capping dilakukan dengan tutup ulir dengan diameter 28 mm. Bir diumpankan ke unit pembotolan yang dipasteurisasi.
Setelah ditutup, botol dipindahkan ke mesin pelabelan melalui konveyor pelat. Label diterapkan dalam tiga posisi: label depan, kerah dan label belakang. Penerapan penandaan laser (А1ХТЕСК) dilakukan pada label belakang. Mesin pelabelan dilengkapi dengan kontrol pelabelan. Pernikahan untuk pendaftaran ditugaskan ke "kantong" khusus. Selanjutnya, produk dikirim ke pengemasan termal oleh konveyor.
Botol didistribusikan di atas nampan karton dan dibungkus dengan kertas timah. Setelah itu, mereka dipindahkan melalui konveyor pengemasan ke paletizer pengemasan, di mana mereka ditumpuk di palet euro. Dan operasi selanjutnya adalah pembungkusan film.
Produk yang tumpah dan dikemas dikirim ke gudang produk jadi.
Deskripsi skema teknologi menuangkan bir ke dalam botol.
Bir diumpankan dari forfas ke pipa menuju pompa pasteurisasi. Pompa melakukan peningkatan tekanan hingga sekitar 13,5 Vag. Setelah itu, bir masuk ke bagian regenerasi pasteurizer dan kemudian ke bagian pasteurizer, di mana suhu outlet 720C. Suhu ini dipertahankan selama 30 detik pada tekanan sekitar 11,5 bar. Kemudian bir masuk ke bagian regenerasi, dan kemudian ke bagian pendinginan. Setelah dingin, bir diumpankan ke unit pembotolan.
Kotak dengan wadah diumpankan dari gudang ke depalletizer. Ini digunakan untuk menghapus kotak dari palet. Peti dengan botol dikirim ke ekstraktor, dan palet kosong diumpankan ke pembuat palet. Dengan bantuan ambil (pegangan adalah perangkat pneumatik untuk menangkap botol), ekstraktor mengeluarkan botol dari kotak dan meletakkannya di konveyor.
Konveyor mengantarkan botol ke mesin cuci botol. Mesin cuci botol adalah mesin cuci jarum suntik, dalam proses melewatkannya, botol dicuci luar dan dalam, dan juga terinfeksi.
Proses pencucian botol dapat dibagi menjadi lima operasi:
mengosongkan botol dan pra-bilas (merendam) dengan air panas;
berendam dalam bak mandi alkali;
penghapusan label;
pembersihan mekanis (membilas dengan alkali dan air panas);
bilas dengan air panas dan pendinginan dengan air dingin.
Setelah mesin cuci botol, botol bersih melewati inspektur botol, di mana botol diperiksa. Botol yang rusak dikeluarkan dari unit pengisian dengan sistem konveyor.
Langkah selanjutnya adalah mengisi dan menutup botol pada unit pembotolan.
Di mesin pengisi, botol pertama kali dimasukkan ke saluran masuk melalui roda gigi cacing. Kemudian, melalui tanda bintang di saluran masuk, mereka memasuki piring yang terletak di bawah keran pembotolan. Pelat menekan botol ke katup pengisian. Tangki berbentuk cincin dengan keran pengisian berputar, minuman dari produksi memasuki tangki melalui pompa. Mengisi botol dengan minuman terjadi dalam beberapa tahap: mengeluarkan udara dari botol, mengisi botol dengan karbon dioksida, mengisi botol dengan bir, mengurangi tekanan pada botol.