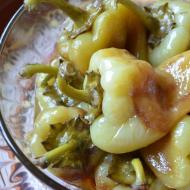
A víz palackozásának technológiai műveletei. A sörpalackozás technológiai sémájának kiválasztása, indoklása és leírása. Gépek egy töltőfejjel
BEVEZETÉS…………………………………………………………………..
1. A TECHNOLÓGIAI FOLYAMAT LEÍRÁSA………………
2. A TECHNOLÓGIAI FOLYAMAT AUTOMATIZÁLÁSA……..
3. A VEZÉRLŐ PROGRAMOZÁSA…………………………
KÖVETKEZTETÉS………………………………………………………………
BEVEZETÉS
Az irányítás automatizálása a termelési hatékonyság növelésének egyik fő iránya. Tovább Yu.V. Andropov megjegyezte, hogy szükséges a gyártás automatizálása, a számítógépek és a mikroprocesszoros technológia széles körű elterjedésének biztosítása.
Az energiatermelés hatékonyságának növelésének egyik módja a számítástechnika bevezetése az irányítási rendszerekbe. Az automatizált irányítási rendszerek széleskörű bevezetése objektív szükségszerűség, az irányítási feladatok bonyolultsága, az irányítási rendszerekben feldolgozandó információ mennyiségének növekedése miatt.
A mai napig minden komoly vállalkozás bevezetett automatizált folyamatirányító rendszereket, és az automatizált vezérlőrendszerek látják el a vállalkozás feladatainak 90%-át.
A technológiai folyamatok karbantartásának megszervezésében fontos szerepet játszanak a technológiai berendezések és folyamatok helyi (lokális) vezérlőrendszerei, amelyek különálló, egymással nem összefüggő objektumok vezérlésére és kezelésére hierarchikus irányítási rendszerben az alsó szintet alkotják. Ezek a vezérlőrendszerek egyhurkosak, és az ilyen rendszerek szinkron vezérléséhez véleményem szerint a legjobb egy vezérlőt használni a vezérlésben. Mivel a gyártás folyamatos jellege mellett az automatizálás fő feladata a paraméterek automatikus szabályozása, a diszkrét gyártásnál (mint az én technológiai folyamatomnál is) a szoftveres-logikai vezérlés a legalkalmasabb. Ennél a technológiai folyamatnál figyelembe kell venni, hogy a műhely óránként 5000 palack ásványvizet állít elő, valamint az áruk számlálása és nyilvántartása munkás segítségével.
Nala nem mindig pontos. Figyelembe kell venni azt is, hogy a töltőgép helytelen beállítása termékkárosodáshoz (palackrobbanáshoz) vezet, az optimális gyors beállítás érdekében információra van szükség olyan mutatókról, mint a töltőgép kamrájában uralkodó nyomás bizonyos időszakokban. Időben (időbeli statisztika), ennek az információnak a dolgozó személyzet segítségével történő rögzítése nem mindig lehetséges jó minőségben, rövid időintervallum (az egyeztetések közötti lépés) mellett pedig szinte lehetetlen. Ezenkívül biztonsági okokból, mivel ezt a technológiai folyamatot magas páratartalom jellemzi, és minden vezérlőrendszer elektromos áramkörre épül, el kell hagyni a TP vezérlés nélküli vezérlési módját. Ezért szükségesnek tartom az ásványvíz palackozó TP-be a vezérlőn és a hozzá való szoftveren alapuló szoftver-logikai vezérlést bevezetni, ami minden számítást, regisztrációt, mérést és egyéb fáradságos munkát elvégz.
1. A TECHNOLÓGIAI FOLYAMAT LEÍRÁSA
A technológiai folyamat blokkdiagramja az 1.1. ábrán látható A nagyobb áttekinthetőség érdekében ezt a technológiai folyamatot 10 részre osztottam:
1. Az első rész egy tartály import ásványvíz számára (H-1 és H-2). A konténerek száma 2 db 24 tonnás. Ezeket a tartályokat életbiztonsági okokból kiviszik a műhelyből.
2. A második rész egy élelmiszeripari elektromos szivattyú A9-KNA (2 * 105? Pa), amely vizet pumpál az akkumulátorokból az F1 és F2 kerámiaszűrőkbe (a márka árnyékolt).
3. A technológiai folyamat harmadik részébe beépítettem egy freonkompresszort és egy H-3 kapacitív tárolótartályt az F1 és F2 szűrőkből érkező, TsN-1 centrifugálszivattyúval szivattyúzott víz optimális hőmérsékletre hűtésére. +4 C import ásványvíz szén-dioxiddal való keveréséhez.
4. A negyedik rész egy olyan berendezést tartalmaz, ahol szén-dioxid palackokat szállítanak (a palack nyomása 70 MPa), a palackok sorba vannak kötve. A szén-dioxid-ellátás szabályozása pneumatikus reduktorral történik, a pneumatikus reduktor kimeneti nyomása 2MPa. A vizuális vezérléshez áramlásérzékelők is rendelkezésre állnak.
5. Az ötödik rész egy telítő, ahol ásványvizet kevernek össze, szivattyúznak a H3 hűtőtartályból két TsN-2 és TsN-3 centrifugálszivattyúval, valamint szén-dioxiddal.
6. A hatodik rész tartalmaz egy AMMB palackmosó gépet a tartályok mosására és fertőtlenítésére. A palackmosáshoz a víz P = 2 MPa nyomás alatt kerül a gépbe; mennyiségben F = 6m3?/perc. A kijáratnál egy fényernyőt biztosítanak a kimosott tartályok minőségének vizuális ellenőrzésére, vagyis a palackmosógép kijáratánál. A minőség ebben az esetben a palack integritása és tisztasága.
7. A technológiai folyamat hetedik része a kiöntő monoblokk, három részre osztható:
Adagolás - szirupellátáshoz, ha édes vizet állítanak elő;
Automata töltőgép folyadékok nyomás alatti töltésére, mivel ebben a technológiai folyamatban a palackozás nem szint szerint történik (minden palackhoz meghatározott mennyiségű ásványvíz), hanem a töltőgép kamrájában és a palackban lévő nyomás arányával. ;
Kupakoló gép (UB márka) - palack bádogdugóval történő lezárásához.
8. A nyolcadik rész a BA szállítógép, ez a hibák feltárását szolgálja, a minőség itt a következő: a palack lezárását úgy kell elvégezni, hogy a palack ne repedjen meg, és légmentesen zárva kell lennie a gáztalanítás elkerülése érdekében, mivel valamint idegen testek behatolása, például szennyeződés részecskék, üvegdarabok stb.
9. A kilencedikhez tartozik a VEM 614 címkézőgép, amelyet automatikus címkézésre használnak. Ha a megtöltött palack áthaladt a szállítógépen, akkor a palack tartalmának megfelelő címkét ragasztanak rá. Ebben az esetben a címkét nem szalaggal kell beadni, hanem előre kivágott formában.
10. A tizedik rész a csomagolás, amely teljes egészében két fős dolgozó stáb segítségével készül.
A technológiai folyamat egyik részéből a másikba a palackot szállítószalag táplálja.
2. A TECHNOLÓGIAI FOLYAMAT AUTOMATIZÁLÁSA
2.1. Ásványvíz palackozási automatizálás kiterjesztett működési diagramjának leírása.
A kiterjesztett FSA a 2.2. ábrán látható.
Ebben a technológiai folyamatban blokkolási, jelzési és védelmi rendszereket biztosítanak. Amikor a szint (1. pozíció) eléri a felső vagy alsó szintet a PA töltőgépben, az elektromos szelep (1. pozíció) rendre zárva vagy kinyílik.
Amikor a szint (2. pozíció) eléri a telítőben a tetejét vagy az alját, a centrifugálszivattyúk (2. pozíció) rendre kikapcsolnak, illetve bekapcsolnak.
Amikor a szint (3. pozíció) eléri a felső vagy alsó szintet a H-3 hűtőtartályban, a centrifugálszivattyú (3. pozíció) rendre kikapcsol, illetve bekapcsol.
Amikor a hőmérséklet (4. pozíció) eléri a felső vagy alsó hőmérsékletet a H-3 hűtőtartályban, az elektromos szelep (4. pozíció) záródik, illetve nyit.
A minőségellenőrzés az RA töltőgép kapacitásában történik (5. pozíció).
3.2. Automatizálási eszközök kiválasztása.
A folyamat automatizálásához számos jelátalakító eszköz és érzékelő használatára van szükség.
A hőmérséklet-szabályozás a TKhK - 0179 hőelem segítségével történik (4-1. tétel). Az érintkezésükhöz normalizálni kell őket az Sh-703 átalakítóval (4-2 pozíció). Alaphiba 0,53 – 1,35%.
Az aktuátor vezérlése a PKE - 212C gombokkal történik (1-6, 1-7,2-6, 2-7, 3-6, 3-7, 4-6, 4-7 pozíció). A kezelőpanelről a PME-011 mágneses indítón keresztül (1-4, 1-5, 2-4, 2-5, 3-4, 3-5, 4-4, 4-5 pozíció).
A Dr-M (1-7, 4-8 pozíció) végrehajtó elektromos mechanizmusok. Az érzékelő impulzusának vételekor kezd működni, majd önállóan működik, és automatikusan leáll a szelep nyitása vagy zárása után.
Az ásványvíz minőségének ellenőrzésére a DKB-1M koncentráció-analizátort (5-1 pozíció) használják, 0,5 mA normalizált kimeneti jellel.
A szint szabályozásához LABKO - 2W szintmérőt használnak (1-1, 2-1, 3-1 pozíció). A kimeneti jel normalizálása a Sapphire-22DD átalakítóval történik (1-2, 2-2, 3-2 pozíció).
3. A VEZÉRLŐ PROGRAMOZÁSA.
A program jobb megértése érdekében bemutattam az algoritmusát:
Az 1-es, 2-es, 3-as körökben (2.2. ábra) a szint figyelése az RA töltőgépben, telítőben, H-3 hűtőtartályban történik.
A 4. körben a H-3 hűtőtartály hőmérsékletét szabályozzák.
A következő értékeket fogadjuk el kódkombinációként:
Adja meg az L1 szintű értéket az RA-ból |
||
L1=1 Lépjen a "Szelep tolózárjának zárása (1-7. pozíció)" pontra. |
||
L1 = 0,5 m. Lépjen a "Nyissa ki a csúszószelepet (1-7. tétel)" pontra. |
||
Adja meg az L2 szint értékét a szaturátorból |
||
L2=2 m Tovább a "Szivattyúk kikapcsolása (2-7., 2-8. tétel)" részhez. |
||
L2 = 0,3 m. Lépjen a "Szivattyúk engedélyezése (2-7., 2-8. tétel)" pontra. |
||
Adja meg az L3 szintértéket a H-3 hűtőtartályból. |
||
L3=1,5 m Tovább a "Szivattyú kikapcsolása (3-7. tétel)" ponthoz |
||
L3 = 0,2 m. Lépjen a "Szivattyú bekapcsolása (3-7. tétel)" pontra. |
||
Adja meg a T szint értékét az RA-ból |
||
T £ 4 0 C Ugrás a "Close slee on valve (4-8. tétel)" pontra. |
||
T > 4 0 C Lépjen a "Nyissa ki a tolózárat (4-8. tétel)" pontra. |
||
Van-e program kilépési jel? |
||
Ha igen, lépjen a "Programvégrehajtás leállítása" pontra. |
||
Ha nem, menjen a program elejére |
||
Zárja el a tolózárat a szelepen (1-7. pozíció) |
||
Nyissa ki a tolózárat a szelepen (1-7. pozíció) |
||
Kapcsolja ki a szivattyúkat (2-7, 2-8 tétel) |
||
Kapcsolja be a szivattyúkat (2-7, 2-8 tétel) |
||
Kapcsolja ki a szivattyút (3-7. tétel) |
||
Kapcsolja be a szivattyút (3-7. tétel) |
||
Zárja el a tolózárat a szelepen (4-8. tétel) |
||
Nyissa ki a tolózárat a szelepen (4-8. pozíció) |
||
Kimeneti szint értéke L1 |
||
Kimeneti szint értéke L2 |
||
L3 szintű érték megjelenítése |
||
Kijelző hőmérséklet T |
||
KÖVETKEZTETÉS
A tanfolyam célja egy olyan programozható vezérlő szoftver kifejlesztése volt, amely az ásványvíz palackozási folyamatát vezérli.
A sörpalackozás technológiai sémája.
A sor azzal kezdődik, hogy egy rakodógép szállítja a dobozokat palackokkal a zacskótörő géphez. A csomagológépből a dobozok a dobozokból palackokat kivonó gépbe kerülnek. A kihúzott palackok a palackmosó gépbe kerülnek, ahol a palackokat kimossák és befecskendezik. A palackok ezután átmennek egy fényernyőn a kimosott palackok végső ellenőrzéséhez. A vízzel kezelt palackok a töltő-záró gépbe kerülnek. A sör stabilitásának növelése érdekében a palackozás után a palackokat pasztőrözésre küldik. A pasztőrözés alagútpasztőrözőben történik. A pasztőrözés után a palackok egy kilökőgépen mennek keresztül, hogy ellenőrizzék a termékek hibáit. Az elutasításon átesett termékek a címkézőgépbe kerülnek. Ezután a palackok a gépbe kerülnek a palackok dobozokba rakására. A 12 000 palack/óra kapacitású sör palackozásánál a palackok dobozba helyezése után zsugorfóliába csomagolás következik.
A PET-palackba történő palackozás technológiai sémája.
A PET-palackok performs formájában érkeznek az üzembe.). Ezután az előadásokat manuálisan adagolják egy automata fúvógépbe. Ezután a felforrósított előadásokat a tányéros szállítószalagon keresztül az öblítőgéphez vezetik, ahol az előadásokat leöblítik. Az öblítőgépből kaotikusan érkeznek a palackok, sorba rendezéséhez a palackok áthaladnak a töltőgépen. A sorban sorakozó PET palackok a kupakológépbe kerülnek, a géphez kupakoló szállítószalag csatlakozik. A késztermékek a címkézőgépbe kerülnek. A kész PET palackok a csomagolósorra kerülnek. Ezután a becsomagolt PET-palackokat egy rakodógép a késztermékek raktáraiba küldi.
A sör hordóba palackozásának technológiai sémája.
Az üres hordókat a táraraktárból a külső hordós mosógépbe szállítják, hogy eltávolítsák a szennyeződéseket. Ezután a külső mosóberendezésből a hordók a belső mosó- és töltőegységbe jutnak. A töltésvezérlésre kész hordókat az automata mérlegekhez táplálják.
2 A sörtermékek kiszámítása
1. táblázat – Termékválaszték
2. táblázat – A sör megoszlása tartályok fajtái és típusai szerint
palackokban | ||||||
Berezina | ||||||
Szlucki különleges. | ||||||
Zhigulevskoe speciális | ||||||
Bobruisk sötét |
A termékszámítás 100 kg sörfajtánként elfogyasztott gabonatermékre történik, majd az 1 dal és az éves kibocsátás újraszámítása következik.
Küldje el a jó munkát a tudásbázis egyszerű. Használja az alábbi űrlapot
Diákok, végzős hallgatók, fiatal tudósok, akik a tudásbázist tanulmányaikban és munkájukban használják, nagyon hálásak lesznek Önnek.
Házigazda: http://www.allbest.ru/
Bevezetés
A szeszfőzdék gyártása az élelmiszeripar egyik ága, amely alkoholos italok és szeszes italok előállítását biztosítja. A vodkák és alkoholos italok korszerű gyártása csúcstechnológiás és kifinomult berendezések, új anyagok és reagensek használatán alapul. Az új technológiák és anyagok minősített alkalmazása megköveteli az oldódási, adszorpciós, diffúziós és más fontos folyamatok fiziko-kémiai folyamatainak mély megértését, amelyek a nyersanyagok és félkész termékek késztermékké történő átalakítása során fordulnak elő.
Az elmúlt években jelentős változások mentek végbe a vízkezelési technológiák terén. A fordított ozmózisos vízkondicionáló egységek széles körben használatosak, de használatuk a teljes termelés egészének megszervezéséhez, a fordított ozmózis alapjául szolgáló folyamatok lényegének ismeretéhez és e folyamat irányításának képességéhez szükséges.
A palackmosás elengedhetetlen feltétele a termékminőség biztosításának, hiszen a visszaváltható csomagolás használatakor a palackokon régi címkék lehetnek, és tartósan szennyeződhetnek. Mosogatás előtt az edényeket a szennyezettség mértékétől függően szétválogatják. Az átlagosan szennyezett palackok közvetlenül a palackmosóba kerülnek. A túlzottan szennyezett palackokat előmossák (áztatják).
A felesleges szennyeződést tartalmazó palackokat az előmosáshoz küldik, amely lúgos és savas bázisú mosásra oszlik.
A lúgos mosás olyan mosogatás, amelyhez nagy koncentrációjú lúgos oldatot kell használni, palackmosó gépeken a következő módban történik:
A lúg koncentrációja a fürdőben 3%;
A gép termelékenysége felére csökken;
Ha van 2. fürdő, akkor 70-80°C hőmérsékletet tart fenn;
A palackok befecskendezését és külső mosását 40-45 ° C hőmérsékletű vízzel végezzük;
Az előmosott piszkos edényeket rendszeres mosogatásra küldik a gépbe.
Savas-lúgos mosás. Erősen szennyezett edényekhez (sólerakódások, gyűrűk a falakon stb.), amelyeket előzetesen savval kell kezelni, valamint olyan szennyeződések esetén, amelyek nagy koncentrációjú lúggal való kezelést igényelnek (zsírmaradványok stb.), kézi elősavat -alapfeldolgozás speciális mosóvályúkban vagy egyéb eszközökben. Az erősen szennyezett edényeket külön helyiségben, a mosó-palackozótól elkülönítve mossák el. Ugyanakkor be kell tartani a savakkal és lúgokkal végzett munka során előírt biztonsági előírásokat.
A szennyeződés típusától függően a palackokat szódabikarbónával vagy sósavoldattal kezelik egy fodros segítségével.
1. Technológiai rész
A technológiai séma kiválasztása, indoklása és leírása.
A vodkát és más alkoholos italokat üvegekbe töltik. Ez a kurzusprojekt egy jó víztisztítási rendszert mutat be palackmosáshoz, annak újrafelhasználásának lehetőségével. A víz nagyon drága termék a vállalkozások számára, így az újrafelhasználás nagymértékben csökkenti a pénzügyi költségeket. Az előny a mosás, a víztisztítás és a mosószerek regenerálásának teljes automatizálása is.
A vízellátásból a víz a homokszűrőbe (1), majd az „AQUA-electronics” mikroszűrőbe (2) kerül. Ezeknek a szűrőknek a segítségével a vizet megszabadítják a szuszpenzióktól és a vassóktól. Az előkezelés után a víz a vízgyűjtőbe (16) kerül. Szükség esetén adagolószivattyúk (15) segítségével stabilizáló adalékokat adagolnak hozzá - híg kénsavoldatot a tartályból (13) és polifoszfátokat a tartályból (14). A könnyebb használat érdekében a reagens oldatokat naponta egyszer készítik el. Ezután a vizet egy baktériumölő egységben (17) kezelik, és egy tároló kollektorba (18) továbbítják, ahonnan egy három nagynyomású dugattyús szivattyú (20) segítségével egy kaszkádba szivattyúzzák egy hidraulikus akkumulátorrendszeren (19) keresztül. fordított ozmózisos eszközök (21).
A tisztított víz minőségét sómérő (23), a mennyiségét áramlásmérő (22) szabályozza. Egy szivattyú (6) segítségével a lágyított víz egy nyomótartályba (7) kerül. A fent leírt módszerrel nyert víz a következő mutatókkal rendelkezik: teljes keménység 0,02-0,22 mg * ekv / dmi, lúgosság 0,16-0,3 mol / dmi, oxidálhatóság 0,2-1,5 mg O2 / dmi, alacsony mikroelem-tartalom.
A fordított ozmózisos üzem legfeljebb 0,5 g/dm³ sótartalmú vízzel működik. Előzetes víz-előkészítés telepítése esetén nem szükséges. Ha a sótartalom 0,5-30 g/m3 és magasabb, valamint a víz zavarossága 1,5 mg/dm3-nél nagyobb, akkor a fordított ozmózisos vízkezelés előtt mikroszűrést, ultraszűrést és Na-kationizálást kell bevezetni.
A víz előkezelésének egyszerűbb módja a Na-kationizálás. A víz nagy teljes keménysége mellett szűrőkön (1), (2) és Na-kationcserélő szűrőn (4) való átengedéssel egészül ki. A Na-kationit szűrő regenerálása a sóoldóból (3) származó sóoldattal történik. A meglágyult vizet egy gyűjtőben (5) gyűjtik össze, majd egy nyomótartályba (7) juttatják, majd a korábban leírt módszer szerint feldolgozzák. Ez a víz szükséges a palackok mosógépben való kiöblítéséhez.
A piszkos palackokat tartalmazó ládák a raktárból a palackkiszívóba (24) érkeznek. A palackokat tartalmazó dobozok a gépbe kerülnek, és a fej alatt megfogókkal megállnak. Aztán a fej leereszkedik a dobozba, megragadja az üvegek nyakát, felemelkedik és az asztalhoz viszi a palackokat. Az üres láda tovább halad a szállítószalag mentén, helyét a következő láda veszi át.
Egy lemezes szállítószalag (25) segítségével a palackokat a 10 tartályból származó lúgos oldattal egy palackmosóhoz (26) irányítják. Palackmosó gépben az új palackokat csak kiöblítik, a keringő palackokat pedig előtisztítják, majd a gépben hideg-meleg vízzel, lúgos oldattal mossák ki. Mosószerként nátrium-hidroxidot, nátrium-karbonátot, trinátrium-foszfátot, szulfosókat stb. használnak. A lúgoldat koncentrációja kézi és félautomata mosógépeknél 1,0-3,0%, automata mosógépeknél - 1,8-2,0%, az oldat hőmérséklete nem lehet 80 °C-nál alacsonyabb.
A lúgos oldatot a keverőtartályban (10) készítik, ahol a kollektorból (8) a lúg és a víz a mérőtartályon (9) keresztül közvetlenül a tartálykocsiból a szivattyún (6) keresztül jut el. Mosáshoz is használhatja a használt oldatot. Ehhez a palackmosó gépből a szivattyún (6) keresztül a lúgoldat először a kerámiaszűrőbe (12), majd a regeneráló oszlopba (11) jut. Az oszlop után a lúg a szivattyún (6) keresztül jut a keverőtartályba (10).
A palackmosógép szennyvizét kezelésre küldik. Először a szennyvíz gravitációs erővel a szennyvízgyűjtőbe (27) áramlik. Ezt követően a szivattyú (6) a 28 aknához megy, ahol a lebegő részecskékből ülepedik. Innen a leülepedett víz a szivattyún (6) keresztül a homokszűrőbe (29) jut, ahol megtörténik a végső tisztítás, majd a megtisztított vizet (6) a tisztított víztartályba (8) szivattyúzzák.
Nyersanyagokra, segédanyagokra és késztermékekre vonatkozó követelmények
Ivóvíz GOST 51232-98
Vízminőségi követelmények a SaNPiN 2.1.4.1074-01 szerint
Elkészült termékek:
Üvegpalackok GOST 10117-91
Korona parafa GOST 10167-88
Szén-dioxid GOST 8050-85
GOST 16 353 címkék
Ragasztó dextrin GOST 7699
Mosó- és fertőtlenítőszerek GOST 5100
Etil-alkohol GOST R52522-2006
Vodka GOST R51355-1999
1. A vodkákat és a speciális vodkákat a jelen szabvány követelményeinek megfelelően kell elkészíteni, a technológiai előírások, a vodkák és speciális vodkák előállítására vonatkozó utasítások, valamint az előírt módon jóváhagyott egészségügyi szabványok és szabályok szerinti receptúrák szerint.
2. Az íztől és az aromás tulajdonságoktól függően a vodka összetevőinek tartalma vodkára és speciális vodkára oszlik.
3. Az érzékszervi jellemzők tekintetében a vodkának és a különleges vodkának meg kell felelnie a következő követelményeknek:
Jellemző: átlátszó folyadék, idegen zárványok és üledék nélkül
Szín: színtelen folyadék
Íz és aroma: az ilyen típusú vodkákra jellemző, idegen íz és aroma nélkül. A vodkának a vodkában rejlő enyhe ízűnek és jellegzetes vodkaaromának kell lennie; speciális vodkák - enyhe íz és hangsúlyos specifikus aroma.
Asztal 1.
2. táblázat.
A termelés technológiai kémiai és mikrobiológiai ellenőrzése
A technológiai kémiai ellenőrzés nagyon fontos az alkoholos italgyártásban, amely értékes nyersanyagokból - etil-alkoholból, növényi alapanyagokból és élelmiszeripari termékekből (cukor, illóolajok stb.) - kiváló minőségű likőrök, likőrök, tinktúrák és vodkák széles választékát állítja elő. . A technológiai kémiai ellenőrzés célja a termékek minőségének javítása, a racionális technológiák bevezetése, a nyersanyagok és anyagok felhasználására vonatkozó normák betartása, veszteségük csökkentése.
A technokémiai ellenőrzés olyan mutatók összessége, amelyek jellemzik a nyersanyagok, félkész termékek, a késztermékek előállításához használt segédanyagok kémiai összetételét és fizikai-kémiai paramétereit, valamint megállapítják a kapott eredmények azonosságát az értékekkel. vonatkozó szabványoknak. A technokémiai ellenőrzés olyan mutatókészlet meghatározását teszi lehetővé, amely az elvégzett elemzések és az ellenőrző mérőműszerek adatai alapján teljes körű információt nyújt a termék minőségéről. A technokémiai ellenőrzési szolgálat egyik fő feladata a technológiai folyamat előrehaladásának, az alapanyagok és késztermékek minőségének ellenőrzése. Kiváló minőségű termékek csak olyan alapanyagok felhasználásával érhetők el, amelyek minősége megfelel a szükséges követelményeknek, valamint a végtermék előállításához szükséges optimális technológiai rezsimek betartásával. Még a nyersanyagok minőségének legkisebb eltérései és a technológiai rendszer megsértése is gyenge minőségű késztermékek kibocsátásához vagy házassághoz vezet. Ezek az eltérések csak a technokémiai kontroll segítségével derülnek ki. A vállalkozásoknál a technológiai kémiai ellenőrzésnek biztosítania kell a receptúrák technológiai szabályainak betartását, a nyersanyagok, félkész termékek és késztermékek minőségi ellenőrzését a szabványoknak és előírásoknak megfelelően.
A technokémiai ellenőrzés végrehajtásának fontos láncszeme maguk az elemzési módszerek, amelyeknek pontos és megbízható eredményeket kell adniuk. Az ilyen eredmények alapján lehetőség nyílik a technológiai rezsim fejlesztésére és finomítására, a termelési hiányosságok és veszteségek kiküszöbölésére, valamint az alacsony minőségű termékek kibocsátásának megakadályozására. Az ilyen ellenőrzés lehet a leghatékonyabb, hiszen a technokémiai ellenőrzés nemcsak a késztermékek hibáinak feltárására, hanem azok megelőzésére, valamint a hibás helyzetek kiküszöbölésére szolgál a gyártási folyamat minden szakaszában.
3. táblázat Technokémiai szabályozás
4. táblázat Mikrobiológiai kontroll
Termelési könyvelés
A vodkák, szeszes italok és alacsony alkoholtartalmú szénsavas italok gyártása során nyilvántartást vezetnek a fő-, segédanyagokról és késztermékekről.
Az alapanyagok felhasználásának meghatározása a receptúrák, technológiai utasítások, valamint az elkerülhetetlen termelési veszteségek figyelembevételével történik.
A termelési veszteségek normái a technológiától, az alkalmazott berendezésektől, azok állapotától, a gyártási fegyelemtől és egyéb tényezőktől függenek. A veszteség mértékét a gyártás különböző szakaszaiban állítják be, és_legalább_1_időben_5_évente újraellenőrzik.
Számviteli_vodka.
A tisztító részlegben lévő víz-alkohol oldatokat és a kész vodkát térfogat és a bennük lévő vízmentes alkoholtartalom alapján veszik figyelembe. A késztermékek, pl. palackokba csomagolva, díszítve és hullámkarton dobozokba csomagolva, mennyiségileg meghatározva és dekaliterben kifejezve.
Az expedícióra átvitt, valamint az elosztóhálózatba kibocsátott késztermékeket a dobozok, a palackok és végül a dekaliterek száma alapján veszik figyelembe.
Az üzemben a palackok és dobozok számbavételére elsősorban elektrokontakt típusú számlálóberendezéseket használnak.
Alkohol_leltár.
Ipari helyiségekben történő alkoholleltározáskor a mérőtartályokban és egyéb tartályokban lévő alkohol mennyiségét a szintmérők leolvasása alapján határozzák meg. Ezenkívül minden konténernek rendelkeznie kell az előírt módon állami hitelesítési tanúsítvánnyal. Egyidejűleg mérje meg az_alkohol_erősségét és hőmérsékletét_minden_tartályban.
A félkész termékek (szeszes levek, gyümölcsitalok, forrázatok, aromás szeszes italok), vizes-alkoholos oldatok, vodkák, alkoholos italok és alacsony alkoholtartalmú szénsavas italok tartályban, javítható és helyrehozhatatlan házassága számát a mérőpoharak leolvasása határozza meg. dekaliterek és egyidejűleg mérik a folyadékok hőmérsékletét, minden tartályból mintát vesznek az erődítmény meghatározásához.
A vodka osztályon a szűrőkben lévő víz-alkohol oldat mennyiségét veszik figyelembe, a kommunikációban feltüntetik az alkoholtartalmú folyadékok mennyiségét. Az alkohol elszámolása a kommunikációban és a szűrőakkumulátorban a berendezésben lévő alkohol jelenlétének megfelelően történik.
Kivételes esetekben a víz-szeszes folyadékot leeresztik a berendezésből_és_mért.
A vízmentes alkohol meghatározásakor félkész termékekben vagy jelentős extrakciós anyagot tartalmazó késztermékekben 20 °C feletti vagy alatti hőmérsékleten a termék térfogatát 20 °C-ra csökkentjük. A térfogat 20 ° C-ra történő emelése speciális táblázatok szerint történik, amelyek figyelembe veszik a termékek térfogatának bővülését, a bennük lévő extraktum- és alkoholtartalomtól függően. A vízmentes alkohol mennyiségét úgy határozzuk meg, hogy a 20 °C-on mért erősséget megszorozzuk a termék 20 °C-ra csökkentett térfogatával.
Az alkohol és cukor elszámolása a technológiai folyamat ellenőrzése, az anyagi erőforrások megtakarítása és a_teljes_beszámoltatás érdekében történik.
2. Települési rész
vodka nyers mikrobiológiai recept
Termékszámítás
A "Michurinskaya" vodka receptje:
alkohol javított "Extra",
lágyított víz,
alma 3 kg,
sárgarépa - 0,82 kg,
cukor - 6 kg.
A számítás 1000 megadott terméken alapul.
5. táblázat
Az Élelmiszeripari Minisztérium által jóváhagyott normák szerint a veszteségeket elfogadják:
Alkohol 0,94%,
Javítható házasság 1,7%,
Jóvátehetetlen házasság 0,7%.
Az alkohol mennyiségének kiszámítása
A vodka elkészítéséhez elfogyasztott alkohol mennyiségének meghatározásához figyelembe kell venni annak helyrehozhatatlan veszteségét a válogatás előkészítése, az aktív szénnel történő feldolgozás, a szűrés és a palackozás során. Ezeket a veszteségeket a termelésbe kerülő alkohol mennyiségének százalékában számítják ki. Az alábbi alkoholveszteség-értékeket fogadjuk el.
6. táblázat
Az ilyen típusú vodka elkészítéséhez burgonyaszem alapanyagokból előállított, 96,4%-os rektifikált alkoholt veszünk. A vízmentes alkohol fogyasztása az 1000 dalos válogatás elkészítéséhez, figyelembe véve a szilárdságot és a termelési veszteségeket,
V = =403,76 adott
96,4 térfogatszázalékos "Extra" rektifikált szesz fogyasztása.
V = = 418,84 adott
A korrigált víz mennyiségének kiszámítása.
Figyelembe véve az alkohol-víz keverék összehúzódását, hogy 40 térfogatszázalékot kapjunk. 100-ra válogatva 96,4 térfogatszázalékos alkoholt kaptunk. vízfogyasztás 142,2 lesz. 1000 termék után a vízfogyasztás a következő lesz:
V víz = = 595,59 dal
A válogatás mennyiségének kiszámítása.
Az előkészített válogatás mennyisége nagyobb, mint a beérkezett vodka mennyisége, mert egy része visszakerül a következő válogatás előkészítésére, egy része szűrők és szénoszlopok mosásakor elveszik, regeneráláskor pedig helyrehozhatatlan házasság formájában visszakerül. A veszteségek értékét a teljes termelési mennyiség 1,7%-ának kell tekinteni. Ezenkívül válogatási veszteség lép fel a rossz hulladékkal, amelyet nem lehet újra felhasználni. Ezeket a veszteségeket figyelembe véve a válogatási mennyiség a következő lesz:
V fokozat. = = 1033,4 adott,
ahol: 1,7 - a javítható házasság értéke,
0,7 - a helyrehozhatatlan házasság értéke,
A javítható házasság kötete
V isp.br. = = 17 adta
V hibás br. = = 7 adott
Ha figyelembe vesszük a tisztítóüzemben bekövetkezett vodkaveszteséget, és feltételezzük, hogy a palackozóműhely a teljes termelési mennyiség 0,5%-ának megfelelő helyreállíthatatlan hibát okoz, akkor a behozott tartályokban lévő vodka mennyisége:
V==1015 adta
7. táblázat Az 1000 termékre jutó nyersanyag-felhasználás összesítő táblázata
Termékek |
Egységek |
Termék mennyisége |
||
Rektifikált alkohol |
||||
Visszanyert víz |
||||
Válogató |
||||
Javított házasság |
||||
Javítatlan házasság |
||||
Vodka a kádban |
||||
8. táblázat Összefoglalás asztal Termékek
Termékek |
mértékegység |
Termék méret |
||||
Rektifikált alkohol |
||||||
Visszanyert víz |
||||||
Válogató |
||||||
Javított házasság |
||||||
Javítatlan házasság |
||||||
Vodka a kádban |
||||||
Számítás és felszerelés kiválasztása
A technológiai séma felszerelésének kiválasztásához ki kell számítania az óránként gyártott palackok számát, azaz:
a \u003d 10 * 1900000 * 1,02 * 0,3 / 21 * 3 * 8 * 2 * 0,9 * 0,5 \u003d 12817 palack / óra
2 sort választunk ki 6000 palack/óra kapacitással
Energia számítások
9. táblázat A villamosenergia-fogyasztás számítása
10. táblázat Gőzfogyasztás számítása
11. táblázat A vízfogyasztás számítása.
12. táblázat Sűrített levegő fogyasztásának számítása
13. táblázat Az energiaszámítások összefoglaló táblázata
3. Munkavédelem
Az alkohol- és szeszesital-iparban a fő káros és veszélyes anyagok az ömlesztett nyersanyagok, a szén-dioxid, az alkohol és a lúg, a veszélyes területek pedig a nyomás alatt működő technológiai berendezések.
A termelésben az egészséges és biztonságos munkakörülmények megteremtéséhez szükséges, hogy minden technológiai berendezés és technológiai folyamat megfeleljen a biztonsági követelményeknek.
Az edényboltban a dobozok tárolásánál be kell tartani a Szabályzat előírásait.
Kézi egymásra rakáskor az edényeket tartalmazó ládákat legfeljebb 2 méteres halmokban kell egymásra rakni. A rakatok közötti fő átjárónak legalább 2 m szélesnek kell lennie.
A palackmosó gépbe kerülő palackok hőmérséklete legalább 10°C legyen.
A palackmosó gépeket az alsó szinten kell elhelyezni. Palackmosó gépek 2. emeleti elhelyezése esetén gondoskodni kell arról, hogy a mosófolyadék padlókon keresztül történő esetleges szivárgása megakadályozza a vízszigetelést.
A mosóhelyiségben tömény savakat és lúgokat tárolni tilos.
A palackmosónak reteszeléssel kell rendelkeznie a meghajtó letiltásához a következő esetekben:
A palackhordozó szállítószalag betöltésekor vagy elakadásakor;
A palackok be- és kirakodásához szükséges munkatestek elakadásakor;
Palackok hiányos elvesztése esetén a palackhordozók fészkéből;
Amikor túlcsordul a kivezető szállítószalag palackjai;
A vízellátó hálózat nyomásesésével a gép bemeneténél és a mosófolyadékok hőmérsékletének megváltozásával.
A palackmosó gép kádjainak mosóoldattal való feltöltését és a kazetták palackokkal való feltöltését gépesíteni kell. A tisztítóoldatokat külön helyiségben kell elkészíteni. A törött palackok eltávolítása a gép munkarészeiről csak speciális eszközökkel (kampó, fogó stb.) lehetséges.
A gépek működése során keletkezett törmeléket csak a gépek leállása után szabad eltávolítani, és nem szabad a berendezés közelében felhalmozódni.
4. Ipari higiénia
Az ipari higiénia fő feladata a működő káros termelési tényezők káros hatásainak megelőzése a biztonságos munkakörülmények biztosítása, a foglalkozási és termelési megbetegedések, valamint a korai fáradtság okainak megszüntetése érdekében.
Az élelmiszeripari vállalkozásoknál elsősorban a légzőrendszer, a keringési rendszer, az idegrendszer, a látó- és hallásszervek működését befolyásoló tényezők minősülnek károsnak.
Káros anyagok
Az élelmiszeripari vállalkozások levegőjét szennyező fő káros anyagok a szerves és ásványi eredetű por, az alapanyagok feldolgozása során keletkező különféle gázok, gőzök, kiindulási anyagok, köztes termékek, termékek előállítása, valamint a termelési hulladékban lévők. A légző-, emésztő- vagy bőrszerveken keresztül kis mennyiségben az emberi szervezetbe jutó káros porok, gázok, gőzök károsan mérgező vagy kórokozó hatást fejtenek ki rá, megzavarják a belső szervek, rendszerek élettani működését, vagy különböző betegségeket okoznak.
A káros anyagok nagy része a légzőszerveken keresztül jut be az emberi szervezetbe, amelyek az emberi életfenntartás egyik fő funkcióját - az egész szervezet oxigénellátását - látják el.
A káros következmények, valamint az oxigénhiány miatti fulladás elkerülése érdekében szükséges, hogy a légzéshez használt levegő megfeleljen az egészségügyi és higiéniai követelményeknek mind fő összetevői, mind káros szennyeződései tekintetében.
A káros gázok és gőzök közül a legveszélyesebbek a szén-monoxid és -dioxid, a kén-dioxid, a nitrogén-oxidok, az alkoholok gőzei, az élelmiszer-esszenciák, a savak, lúgok stb.
Kollektív védekezési intézkedések a káros anyagok ellen
Az élelmiszeripari vállalkozásoknál a káros anyagok emberre gyakorolt hatásának megelőzése érdekében kollektív védelmi intézkedéseket alkalmaznak, amelyek a következőkre oszthatók: technológiai, amelynek fő feladata a káros anyagok termelő helyiségekbe való kijutásának megakadályozása; műszaki, amelyek célja a helyiségben lévő káros anyagok MPC-jének fenntartása; az orvosi és megelőző intézkedések a munkavállalók egészségi állapotának szisztematikus klinikai ellenőrzéséből állnak; az ellenőrzés magában foglalja a levegőben lévő káros gőzök, gázok és porok tartalmának felmérését.
Mikroklíma a munkahelyen
Az ipari helyiségek mikroklímája a belső környezet meteorológiai viszonyai, melyeket az emberi szervezetre ható hőmérséklet, relatív páratartalom és légsebesség kombinációja, valamint a zárt szerkezetek és technológiai berendezések felületeinek hősugárzása és hőmérséklete határoz meg.
A mikroklíma indikátorok: hőmérséklet (°С), relatív páratartalom (%), légsebesség (m/s) és hősugárzás intenzitása (W/m²) abszolút értékkel rendelkeznek az optimális és megengedett értékekkel.
Ipari zaj és rezgés
Az élelmiszeripari vállalkozások technológiai berendezései zaj- és rezgésforrást jelentenek. A zaj és a rezgés, mivel biológiai irritáló hatású, általános betegséget okoz az emberi szervezetben.
A munkahelyi zaj- és rezgésszintek biztonsági előírásoknak való megfelelését a mért paraméterek egészségügyi szabványokkal való összehasonlításával állapítják meg.
Mivel a rezgés és a zaj leggyakrabban összefügg egymással, célszerű az ellenük irányuló kollektív védelmi intézkedéseket vibroakusztikus védelmi intézkedések közé sorolni. Ezek az intézkedések a következőkre oszlanak: szervezeti, amelyek magukban foglalják az aktív vibroakusztikus berendezések kizárását a technológiai sémából, minimális dinamikus terhelésű berendezések használatát, helyes működését stb.; a műszakiakat két kategóriába sorolják: azok, amelyek megszüntetik a zajt és a rezgést az előfordulásuk forrásánál, és csökkentik a vibráció és a zaj intenzitását az egészségügyi szabványok szintjére; Az építési és tervezési intézkedések magukban foglalják a berendezések elhelyezésének megtervezését az emberekre gyakorolt hatások csökkentése érdekében.
Az egyéni védelem eszközei
Előjegyzés alapján az egyéni védőeszközök egyéni védőeszközökre és biztonsági eszközökre oszthatók; egészségügyi védelmi eszközök és szolgálati eszközök.
Az egyéni védőeszközök és biztonsági eszközök célja, hogy megakadályozzák vagy a szükséges szintre csökkentsék a munkavállalók veszélyes és káros termelési tényezőknek való kitettségét. Ezeket akkor alkalmazzák, ha a kollektív védelem eszközei nem nyújtanak teljes biztonságot, alkalmazásuk műszakilag vagy gazdaságilag nem célszerű vagy lehetetlen ilyen körülmények között.
Az élelmiszeripari termékekkel közvetlenül érintkező élelmiszer-ipari dolgozók az egyéni védőfelszerelésen kívül személyi higiéniai védőfelszereléssel is rendelkeznek, amely az élelmiszerek fertőzéstől és szennyeződéstől való védelmét szolgálja.
Az ügyeletes egyéni védőeszközök célja a munkavállalók védelme sürgős javítási munkák elvégzése, a balesetek következményeinek kiküszöbölése vagy előre nem látható helyzetekben történő munkavégzés során.
Következtetés
Ebben a kurzusprojektben egy mosási részleg sémát vettek figyelembe, amely a használt víz teljes tisztítását biztosította, annak újrafelhasználásának lehetőségével. Ennek a lehetőségnek köszönhetően csökkennek a víz gazdasági költségei, mert. A termeléshez használt víz nagyon drága termék.
Irodalom
1. I.I. Burachevsky és mások. "Vodkák és alkoholos italok gyártása".
2. Faradzhev "Általános technológia".
3. V.E. Balashov "Vállalkozások diplomatervezése
4. Kovalevsky "A fermentációs gyártás technológiája", 2004.
5. V.S. Nikitin, Yu.M. Burashnikov "Munkavédelem az élelmiszeriparban", Moszkva: "Kolos", 1996.
Az Allbest.ru oldalon található
Hasonló dokumentumok
A sörpalackozás technológiai sémájának kidolgozása. Nyersanyagokra, segédanyagokra és késztermékekre vonatkozó követelmények. Technokémiai és mikrobiológiai védekezés. A "Moszkva" sör gyártásához felhasznált nyersanyagok. A berendezések egészségügyi követelményei.
szakdolgozat, hozzáadva 2015.03.01
Az alkohol megszerzésének módjai. A vodka előállításának sematikus diagramja. A víz-alkohol keverékek elkészítési módja és szűrése. A szeszes italok minőségének értékelése: a kóstolás, a késztermékek elszámolásának, tárolásának és kiadásának rendje.
gyakorlati jelentés, hozzáadva: 2008.01.15
Víz előkészítése lepárlógyártáshoz. A vodka beszerzésének fő technológiai sémája. Italkeverés, alkoholos italok kaszkádszűrése. Az élelmiszer-ecet előállításának technológiája. Szilárd szén-dioxid előállítása.
oktatóanyag, hozzáadva: 2012.02.09
A vodka szennyeződésektől való tisztításának modern módszereinek tanulmányozása és ezek hatása a késztermék minőségére. A vodka ezüstszűréssel történő előállítására szolgáló technológia fejlesztése az OAO "Sibir" vállalatnál. A termelés gazdasági hatékonysága.
szakdolgozat, hozzáadva 2014.10.03
A vodka, alapanyagok és anyagok előállításának technológiai folyamatának ismertetése. A vodka osztályozása és érzékszervi jellemzői. Automatizálási tervezés szivattyú-vezérlőrendszerekhez és hőmérséklet-stabilizáláshoz a CJSC MPBK "Ochakovo" keverési részlegében.
szakdolgozat, hozzáadva 2012.02.12
A vodkagyártás technológiai folyamata a CJSC MPBK "Ochakovo" példáján. A keverő részleg szerepe a vodka gyártásában. Alkoholtartályok és szivattyúberendezések mnemonikus sémája. A gyártási folyamatok automatizálásának gazdaságossága.
szakdolgozat, hozzáadva: 2013.09.04
A SOJSC "BAKHUS" irányítási struktúrája. Alkohol és vodka előállításának technológiája. Késztermékek palackozása, csomagolása és tárolása. Nyersanyagok és késztermékek szállításának technológiai berendezései, minőségellenőrzése. Munka- és környezetvédelem.
gyakorlati jelentés, hozzáadva: 2009.10.27
Az alapanyagok alkotórészeinek jellemzői. Bevétel az összetevők válogatásába. Víz-alkohol keverék kezelése aktív szénnel. A vodka "arany tavasz" előállításának technológiai rendszerének leírása. Anyagmérleg és válogatókád számítása.
szakdolgozat, hozzáadva 2009.04.05
A sajt választéka és tápértéke. A gyártásához szükséges alapanyagokra vonatkozó alapvető követelmények. A gyártás technológiai sémájának kiválasztása, indoklása, leírása. A felszerelés kiválasztásának és elrendezésének, elhelyezésének számítása. A gyártás technológiai kémiai ellenőrzése.
szakdolgozat, hozzáadva 2013.10.27
A vállalkozás termelési programjának elkészítése. A vodka és likőrök gyártósorának technológiai sémájának kiválasztása. A termékek érzékszervi mutatói. Termékek, berendezések, konténerek és segédanyagok számítása. Számviteli és gyártásellenőrzés.
A sörpalackozás technológiai folyamata.
A PET-palackba töltés technológiai sémájának ismertetése
A raklapon lévő előformákat targonca szállítja a fúvógépbe. A gép adagolórendszerrel és előforma-válogató rendszerrel rendelkezik. Segítségével az előformákat 16 formára osztják, amelyekbe nagynyomású légkompresszor és infravörös sugárzó sütő segítségével palackokat fújnak. Az autó uralja a palackokat, a házasságot félreteszik.
A fúvógép után a palackokat az úgynevezett légszállítószalagon továbbítják a vonal mentén.
A szállítószalag egy kiváló minőségű acélszerkezet, függő részekkel az üres PET-palackok fúvógépből történő átviteléhez.
A légszállító szállítja a PET-palackokat a fúvóformázó gépből az automata öblítőgépbe. Az öblítő a keringési elven működik. A palackokat csiga segítségével táplálják a gép ólomcsillagára. A gép bejáratánál van egy vezérlő egy leejtett vagy egy nagy átmérőjű palackhoz. Amikor a reteszelések kioldódnak, a gép leáll. A vezető sztár speciális fogókhoz vezeti a palackokat, amelyek a nyakuknál fogva megragadják őket. Ezután egy bütyök segítségével a palackot 180°-kal elfordítják, és a fogóval szinkronban forgó fúvókák elkezdik a permetezést. A kijáratnál lévő csillag a rögzítéssel szinkronban mozog, eltávolítja az üvegeket. A bemeneti öblítő érzékelőkkel van felszerelve a hibás palackok felismerésére.
Öblítés után a palackokat csillagok segítségével palackozzák.
Háromkamrás rendszer elektronikus vezérléssel. A töltés izobár, nyomás alatt. A palackot emelő segítségével szorosan a töltőszelephez nyomják. A palackozási folyamat négy lépésből áll:
túlnyomás;
nyomáskiegyenlítés és palacktöltés termékkel;
az ital szintjének beállítása és a palackozási folyamat leállítása;
túlnyomás enyhítése.
A töltőgép és a kupak közé habosító van beépítve, hogy eltávolítsa a levegőt a palackból. A finomszemcsés hab a palack nyakáig emelkedik és kiszorítja a levegőt.
A lezárás 28 mm átmérőjű csavaros kupakkal történik. A sör pasztőrözötten kerül a palackozó egységbe.
Lezárás után a palackokat tányéros szállítószalag segítségével továbbítják a címkézőgépbe. A címkéket három helyen alkalmazzák: elülső címke, gallér és hátsó címke. A lézeres jelölés (А1ХТЕСК) felhordása a hátlapon történik. A címkézőgép címkézésvezérlővel van felszerelve. A regisztrációhoz szükséges házasság egy speciális „zsebhez” van rendelve. Ezután a terméket a szállítószalag termikus csomagolásba küldi.
A palackokat kartontálcákra osztják és fóliával csomagolják. Ezt követően a csomagoló szállítószalagon keresztül a csomagoló raklapozóra kerülnek, ahol euróraklapokra rakják őket. A következő művelet pedig a fóliázás.
A kiömlött és becsomagolt terméket a késztermék raktárba szállítjuk.
A sör palackokba öntésének technológiai sémájának leírása.
A sört a forfákból táplálják a pasztőröző szivattyúhoz vezető csővezetékbe. A szivattyú a nyomást körülbelül 13,5 Vag-ra növeli. Ezt követően a sör a pasztőröző regeneráló részébe, majd a pasztőröző részébe kerül, ahol a kilépő hőmérséklet 720C. Ezt a hőmérsékletet 30 másodpercig tartjuk körülbelül 11,5 bar nyomáson. Ezután a sör a regenerációs részlegbe kerül, majd a hűtőszekcióba. Lehűlés után a sör a palackozó egységbe kerül.
A konténeres dobozok a raktárból a raklapozóba kerülnek. A dobozok raklapról történő eltávolítására szolgál. A palackos ládákat az elszívóba szállítják, az üres raklapot pedig a palettázóba táplálják. A markoló segítségével (a markoló egy pneumatikus eszköz a palackok rögzítésére) az elszívó kiveszi a palackokat a dobozból és a szállítószalagra helyezi.
A szállítószalag szállítja a palackokat a palackmosóba. A palackmosó gép mosófecskendős gép, az átengedés során a palackok kívül-belül kimosódnak, megfertőződnek.
A palackmosási folyamat öt műveletre osztható:
palackok kiürítése és forró vízzel való előöblítés (áztatás);
áztatás lúgos fürdőben;
címkék eltávolítása;
mechanikai tisztítás (lúggal és forró vízzel történő öblítés);
forró vízzel öblítjük és hideg vízzel hűtjük.
A palackmosó után a tiszta palackok átmennek a palackvizsgálón, ahol a palackokat megvizsgálják. A hibás palackokat szállítószalag távolítja el a töltőegységből.
A sor következő lépése a palackok feltöltése és lezárása a palackozó egységen.
A töltőgépben a palackokat először egy csigahajtómű segítségével a bemenetbe vezetik. Ezután a bemenetnél lévő csillagon keresztül belépnek egy tányérba, amely a palackozó csapok alatt található. A lemez a palackot a töltőszelephez nyomja. A töltőcsapokkal ellátott gyűrű alakú tartály forog, a termelésből származó ital a szivattyún keresztül jut be a tartályba. A palackok itallal való feltöltése több lépésben történik: levegő eltávolítása a palackból, a palack szén-dioxiddal való feltöltése, a palack sörrel való feltöltése, a palack nyomásának csökkentése.