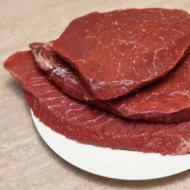
Как делают творог на заводе. Аппаратурно-технологическая схема производства творога. Производство творога традиционным способом
Актуальность соблюдения технологии приготовления творога на производстве обусловлена необходимостью и важностью этого продукта питания для человека. Творогом называют такой традиционный продукт, процесс изготовления которого позволяет сохранить максимальную насыщенность белками. Это кисломолочная продукция, которой присущи диетические свойства, лечебные качества и повышенная пищевая ценность. Большая часть современных лечебных меню, разработанных специалистами, включает творог в качестве одного из базовых элементов питания. Впрочем, как обращают внимание диетологи, даже полностью здоровым людям не стоит пренебрегать этим продуктом - он важен и полезен для всех.
О чем идет речь
Прежде чем рассматривать кратко технологии производства творога, сформулируем, о чем идет речь. Творог - это концентрат белковых структур молока и дополнительных компонентов, присутствующих в этой природной питательной жидкости. Нельзя переоценить значимость протеинов для человеческого организма. Именно они обеспечивают тело материалом для клеточного строительства. Белки нужны для создания ферментных соединений и иммунных тел, за счет которых человек может защищаться от болезней разного рода.
Человеческий организм получает белковые структуры с продуктами питания, расщепляет их, превращая в аминокислоты. Именно эти блоки используются для формирования новых белковых молекул, свойственных конкретному организму. Чтобы процесс протекал полноценно, тело должно иметь два десятка уникальных аминокислот. С пищей сложнее всего получать триптофан, метионин. Оба этих соединения необходимы для полноценной активности нервной системы, обеспечивают возможность работоспособности кроветворных органов и пищеварительного тракта.
Изготовление: с самого начала
Известно несколько технологий производства творога на предприятиях, но все они начинаются с работы по подготовке продукта. Прием молока предполагает не только контроль количества поступающей жидкости, но и проверку ее качества. Задача фирмы - проконтролировать параметры продукции и отсортировать полученное сырье. После смешивания можно выявить органолептические параметры, а именно, вкус молока и его оттенок, аромат и чистоту. Специалисты, занимающиеся молоком, оценивают структуру, уровень кислотности и плотности, наличие и содержание жировой фракции. Если в производственных условиях возникает необходимость хранить молоко продолжительное время, продукт охлаждают. Условия хранения жидкости - прогрев не выше 10 градусов, длительность - не более шести часов.
Известны технологии приготовления творога с применением сухого молока. Его необходимо сперва восстановить. Для этого нужна вода, нагретая до уровня 35-45 градусов (по шкале Цельсия). Затем продукт охлаждают и дают ему набухнуть в течение в среднем четырех часов. Допускается разведение в среде, нагретой до 12 градусов, с предоставлением последующего достаточного времени на набухание. Это практикуется, если нет возможности охлаждать продукцию. Процесс набухания не считают обязательным, но он позволяет повысить выход в среднем на десятую долю. В период набухания в емкость можно добавить растительную клетчатку и специализированные смеси. Продукцию следует обрабатывать в диспергаторе либо регулярно смешивать.
Подготовка: продолжение
Технология приготовления творога предполагает обеспечение продукции возможности нормализоваться после набухания. Процесс включает стабилизацию по жировым фракциям сливками. Альтернатива - растопленный жир. Для этого применяют диспергатор. Вещество топят до 55 градусов, нагревают молоко до этого же уровня и смешивают ингредиенты. Закончив процедуру нормализации, состав дополняют специальными компонентами. Для их подготовки используется холодная вода. Очищенная жидкость необходима в количестве, в среднем десятикратно превышающем объем молока. Ингредиенты смешивают посредством танка либо диспергатора.
О температуре
Технология производства сметаны, творога и творожных изделий предполагает применение специализированного оборудования. Для пастеризации продукции применяют установки, в которых ингредиенты в течение трети минуты находятся под влиянием температуры до 95 градусов. Это обеспечивает максимальную эффективность белкового коагуляционного процесса. Как следствие, выход продукта увеличивается.
Следующий этап - охлаждение смеси до температуры, близкой к 30 градусам. Допускается отклонение в большую и меньшую сторону на пару делений. Процесс предполагает применение мезофильных компонентов. При необходимости использования термофильных ингредиентов или многокомпонентной продукции прогрев необходим до 35 градусов. Смесь перемещают в творожную ванну. Без заквашивания продукция не хранится из-за дополнительного обсеменения, что может привести к дрожжевому привкусу творога, повышенной кислотности.
Подготовка сгустка
Творога предполагает добавление закваски, последующее смешение длительностью четверть часа. Продукт дополняют хлористым кальцием, специальными ферментами, перемешивают еще 10 минут и дают настояться, пока не появится необходимый сгусток. Если кислотность слишком низкая, разрезка приведет к специфической консистенции - готовый продукт напоминает резину.
Длительность молочного сквашивания с применением специальных бактерий - не более 15 часов, но и не меньше шести. Чтобы определить, готов ли сгусток, необходимо титровать плотность и кислотность среды. Подготовленный сгусток режут на кубы и дают настояться полчаса-час, пока не выделится сыворотка. Допускается нагревать вещество до 40 градусов, что позволяет сократить выдержку до 40 минут. Чтобы сгусток прогревался равномерно, его перемешивают. Манипуляции необходимо делать осторожно. На этом этапе есть опасность сварить сгусток. Необходимо предупредить такую ошибку, при этом обработав сгусток так, чтобы сыворотка выделялась достаточно активно. Важно мягкое изменение температурного режима без резкого скачка, иначе нарушится зерновая структура творога.
Работа со сгустком
Творога предполагает применение специальных установок. Сырье помещают в мышки, наполняемые на три четверти, закладывают в пресс и охлаждают от часа до четырех, пока продукт не достигнет необходимого уровня влажности. Далее сгусток подвергает прессованию (включая самостоятельное). Самопресс длится час или больше. Чтобы ускорить процесс, необходимо регулярно встряхивать емкость. В мешках прессовка осуществляется в холодильнике в подвешенном состоянии либо на столе. Среда прогревается не выше 8 градусов. Длительность процедуры - пока творог не достигнет нужной консистенции.
Для обезжиренного продукта оптимальный уровень влажности - 80 %, для жирности 5 % он снижается до 75 %, еще на два процента ниже для творога жирностью 9 %. Применение стабилизатора для сохранения влаги позволяет повысить показатель на один-полтора процента сверх указанного норматива, при этом день хранения позволяет сырью дойти до стабильного состояния. Стабилизация дает окончательный результат только после охлаждения продукции.
Технология производства творога допускает стандартизацию влажности посредством встроенного в холодильные агрегаты специального пресса. Тележки нагружают мешками, наполненными продуктом, укладывая их один на другой, крепят пресс. Когда процесс завершается, творог вынимают их мешков, смешивают, фасуют и отправляют на хранение и реализацию.
Как все начиналось
Творог - это один из самых древних продуктов, изготавливаемых из молока. Предполагают, что люди, используя для хранения молока желудки, случайно обнаружили сычужный процесс заквашивания. В сравнении с самопроизвольным течением так переработка происходила быстрее, а готовый продукт был приятным на вкус. Славяне творог ранее именовали сыром, из него делали сырники. О происхождении наименования филологи и лингвисты все еще продолжают спорить. Даже распространенность сычужных сырных продуктов не изменила востребованности слова «сырники».
Творог в наших землях был одним из наиболее распространенных продуктов, употребляемых едва ли не каждый день. Его готовили из простокваши, которую в емкости ставили в нагретую печь на несколько часов. Содержимое горшка перекладывали в мешок, сливали жидкость и оставляли под прессом. Такой натуральный продукт хранился непродолжительное время, но был изобретен способ его консервирования - описанную ранее процедуру с печью и прессом повторяли дважды, затем закладывали продукт в емкость и закрывали топленым маслом. В прохладном помещении творог, подготовленный таким образом, хранился месяцами.
Технические особенности
Технология производства творога кислотно-сычужным способом применяясь в течение долгих веков. Ферментом для процесса были кусочки телячьих, ягнячьих желудков, предварительно тщательно просушенных. Впервые ферментные препараты изобретены около столетия тому назад. Именно тогда французские промышленники наладили изготовление закваски в жидком виде, вскоре получившей немалый спрос на рынке. В конце 19-го столетия впервые изготовили фермент в сухом виде. С 1888-го начали использовать молочнокислые бактериальные чистые культуры.
В нашей стране принято выделять несколько шагов развития промышленности, связанной с творогом. Первый этап начался, когда появились первые заводы, и длился приблизительно до середины прошедшего столетия. В тот период актуальной была технология производства творога кислотным способом. Сгусток варили в открытой емкости или обрабатывали в печи. Долгие десятилетия промышленность оставалась на низком уровне технического обеспечения. Во многом это было обусловлено длительностью и сложностью сквашивания и этапа работы с прессом. В основном использовался ручной труд. Уже в двадцатых годах начали готовить творог из отличавшихся по жирности сортов молока. Продавали свежий продукт, хранили соленый. К середине прошлого столетия в продаже были три сорта жирного и обезжиренного творога.
Нюансы изготовления
Технология производства творога, используемая в те годы, предполагала применение ванн с двумя стенками или чанов из дуба для заквашивания исходной жидкости. Процедура требовала до 12 часов. Готовность продукта определяли визуально. Сгусток специальным ковшом перемещали в ушат, затем варили на котле, смешивая, дабы вещество прогревалось равномерно. По мере готовности его резали крестами ножами из дерева, вынимали ушаты из жидкости и оставлялись освобождаться от сыворотки. Охлаждаясь, творог самостоятельно прессовался. Чтобы качественно снизить температуру, использовали для хранения творога помещение с прогревом воздуха не выше 8 градусов.
Технология производства творога традиционным способом учитывала тот факт, что самостоятельное прессование позволяло продукту освободиться лишь от части сыворотки. Чтобы удалить остатки, необходимо было продолжить прессование в таре. Для этого использовали непосредственно ту, в которую продукт затем упаковывали. Чаще применяли кадки из дерева в форме обратного конуса. Емкость наполняли на треть либо половину, укрывали тканью и ставили груз. Выдержав продукт некоторое время, сливали жидкость, закладывали новый слой творога и повторяли процедуру. Когда кадка наполнялась полностью, ее накрывали крышкой и хранили в прохладном месте до двух месяцев. Если требовалось хранение до девяти месяцев, творог замораживали, выдерживали, и лишь после этого отправляли покупателю.
Развитие процесса
Со временем технология производства творога традиционным способом трансформировалась, и особенно заметно это стало в середине прошлого века. Считается, именно тогда начался второй этап развития творожной промышленности, длившийся приблизительно до начала 70-х. На заводах проводились объемные работы по механизации. Рабочий процесс оформили аппаратурой. В тот период рабочим стали доступны ванны для молочного сквашивания и изготовления сгустка, тележки для изъятия сыворотки и прессовочные установки, в которых творог предварительно остывал. Такие агрегаты позволили совместить сквашивание с изготовлением и делением сгустка, изъятием сыворотки и прессованием.
После середины прошлого столетия, как можно узнать из составленных в те времена инженерами докладов, технология производства творога без нагрева и с таковым стала доступна большому количеству предприятий, одновременно удалось снизить трудозатраты и временные промежутки на процессы. Рабочие получили доступ к творожным сепараторам. Разработали изготовители творога, функционирующие непрерывно, а также охладители с одним и двумя цилиндрами. Создали смесители для работы одновременно со сливками и творогом, шнековые подъемные установки, вальцовочные аппараты и технику для растирания. Месильные агрегаты позволили работать с творогом и добавками к нему - орехами, изюмом и другими продуктами.
Прогресс не стоит на месте
В середине прошлого столетия изобретена технология производства творога раздельным способом и разработана специальная производственная поточная линия для ее реализации. Практически все технологические этапы изготовления незаменимого для человека продукта механизировали в высокой степени. Объем изготавливаемого творога существенно вырос. Союзный институт питания выпустил рекомендации по обеспечению людей разными нутриентами в течение суток. Объемы производимого творога за счет механизации наконец стали такими, чтобы обеспечивать исполнение этих нормативов.
В тот же период инженеры изобрели автоматические и полуавтоматические фасовочные, упаковочные аппараты. Они позволяли работать не только с творогом, но и Стало возможным быстро паковать продукцию в мелкую тару, рассчитанную на конечного покупателя.
Последний период
Считается, что третий этап начался в 70-х годах и длится по нынешний день. Развились технология производства творога ультрафильтрацией и другими перспективными методами. Техника активно совершенствуется. Созданы новые схемы производственных непрерывных процессов. Предусмотрена возможность белковой коагуляции. Улучшили станции для самостоятельного прессования, усовершенствовали сепараторы, создали схемы для автоматизации работы. Современный человек имеет доступ к большому разнообразию вкусов и типов изделий из творога, включая декорированные глазурью. За последние десятилетия существенно улучшилось оборудование, позволяющее фасовать, перевозить и хранить продукцию. Организованы производственные линии нетрадиционного типа. Современный покупатель имеет доступ к творогу из сыворотки, пахты, сухого молока. Разработана технология производства зерненого творога, включая дополненный сливками, а также диетической продукции. В продаже есть сухой творог.
Полученный за долгие века опыт, современные производственные процессы и исследования в этом направлении позволяют с уверенностью заключить: производство и далее будет совершенствоваться, меняться. Наверняка расширится ассортимент. Во многом это связано с увеличением численности населения и укрупнением городов, что наверняка повлияет на промышленность. Предполагается, в скором времени увеличится количество заводов, активнее станет использоваться немолочное сырье. Предполагается, что технология производства творога ультрафильтрацией, обратным осмотическим способом, ионным обменом будет распространяться все шире. Наверняка больший интерес и применение на практике получит технология электродиализа. Это обусловлено эффективностью мембранной техники. Не менее актуальная перспектива - использование биологических полимеров, позволяющих сделать процесс концентрирования более результативным, повысить эффективность фракционирования.
Вчера, сегодня, завтра
Новые технологии в производстве творога в России, как считают эксперты, будут включать обновление аппаратного обеспечения непрерывного процесса изготовления. Вероятно, уже в скором времени технологам станут доступны эффективные компьютеризированные управленческие системы, благодаря которым контроль за работой будет проще и четче.
Как уже сегодня активно применяются в некоторых державах в процессе изготовления творога. Технология предполагает включение изолятов в натуральный или восстановленный продукт с продолжением изготовления по стандартной системе. Некоторые считают, что со временем станут возможны иные варианты включения соевых белков в производственный процесс. Вероятно, покупатели смогут приобретать специализированные комбинированные продукты.
Как считают аналитики, изучающие особенности развития технологий производства зерненого творога, соевого, обезжиренного и прочих видов, производственное оснащение будет совершенствоваться в направлении непрерывного рабочего процесса. Вероятно, потоковая белковая коагуляция - это самый перспективный вариант развития. При этом аппаратура (вне зависимости от уровня производительности) будет автоматизированной и компьютеризированной, управляемой через единый центр.
О тонкостях
Довольно любопытны особенности изготовления разных кисломолочных продуктов, а не только технология производства творога. Резервуарным способом, к примеру, производят кефир. Этот молочный продукт не менее важен для человека, чем рассмотренный выше. Считается, он изобретен в северокавказских территориях, где его традиционно провозглашали небесным даром и напитком, дарующим силы и бодрость. Кефир рекомендован при ряде заболеваний и позволяет улучшить качество жизни человека. Изготавливается молочным сквашиванием с применением микроскопических форм жизни (дрожжей). В настоящий момент не удалось определить точно микробиологическую природу необходимых для сквашивания грибков. Промышленное изготовление кефира возможно не только резервуарным методом, но и термостатным.
Особенность резервуарной методики - использование одной емкости для закваски, скваски, вызревания продукта. Сперва молоко нормализуют по жирности, нагревают в пастеризаторе и удаляют примеси посредством сепаратора. Следующий этап - пастеризация и обработка в гомогенизаторе. Далее продукт выдерживают и охлаждают, заквашивают и перемещают в резервуар для сквашивания, где появляется сгусток. Система оснащена элементами перемешивания и охлаждения. Созревание достигает 12 часов. Завершение процесса определяется по особенностям структуры продукта и механическим качествам кефира. После готовности продукт разливают в емкости и охлаждают до температуры не более 8 градусов.
Для всех возрастов
Актуальность разработки новейших технологий производства детского творога обусловлена агрессивными условиями жизни человека. Экология постоянно ухудшается, поэтому каждый из нас сталкивается с опасными микроэлементами, и особенно велик вред детским организмам. Многие испытывают нехватку полезных соединений, и восполнить дефицит можно с продуктами питания. Дети нуждаются в довольно большом количестве кальция для нормального развития. Чтобы обогатить рацион, необходимо питаться молоком и изготовленными из него продуктами, включая творог. Современные предприятия производят подходящий для детей творог раздельным методом или способом кислотного сычужного ферментирования. Оба вариант непросты технически. Технологический цикл длителен, высока опасность повторного обсеменения микроорганизмами, вредными для человека.
Особенность детского творога, производимого в настоящее время - сравнительно высокий уровень кислотности. Не всегда организм ребенка располагает ресурсами для компенсирования этого качества. Термокальциевый - появившийся сравнительно недавно метод изготовления низкокислого продукта. Процесс производства требует непродолжительного времени. Технология создана на базе исследований профессора Дьяченко.
Продолжение лек №2
Технология творога, творожных продуктов и сметаны
Творог представляет собой белковый кисломолочный продукт, основная часть которого - казеин - содержит все незаменимые аминокислоты. В твороге жирном содержатся почти в равных количествах (по 18%) белки и жир, а также витамины молока. Творог богат кальцием, фосфором, магнием и другими ценными минеральными веществами. Из продуктов брожения молочного сахара творог содержит молочную кислоту и ароматические вещества, придающие ему специфический кисловатый вкус и кисломолочный запах. В твороге столько же белка, сколько в мясе, а стоимость его значительно ниже. Кроме непосредственного потребления творог используется для приготовления различных блюд, кулинарных изделий и большого ассортимента творожных продуктов. Добавление сахара повышает калорийность творожных продуктов и улучшает их вкус.
Творог и творожные продукты вырабатываются из пастеризованного молока с применением в качестве закваски мезофильных молочнокислых бактерий. Он должен иметь чистый, нежный кисломолочный вкус и запах, нежную консистенцию. Консистенция творога зависит от технологии производства, он может иметь слоистую структуру или представлять собой однородную гомогенную массу. Содержание жира в твороге жирном не менее 18%, в полужирном- не менее 9%; влажность жирного - не более 65%, полужирного- 73, нежирного - 80%. Кислотность творога жирного высшего сорта - 200, I сорта- 225° Т; полужирного высшего сорта -210, I сорта - 240° Т; творога нежирного высшего сорта - 220 и I сорта - 270° Т.
Существует два способа производства жирного и полужирного творога: обычный - из нормализованного молока и раздельный - из обезжиренного молока с последующим обогащением обезжиренного творога сливками. Ниже дана технологическая схема производства творога.
Раздельный способ имеет ряд преимуществ. Значительно снижаются потери жира в производстве; экономия жира на 1 т жирного творога составляет 13,2, полужирного - 14,2 кг. Облегчается отделение сыворотки от сгустка, создается большая возможность механизации технологических операций и, следовательно, повышения производительности труда . Наконец, важным преимуществом раздельного способа производства творога является улучшение качества продукта в результате снижения кислотности: добавление к обезжиренному творогу свежих пастеризованных сливок уменьшает его кислотность, а вместе с тем охлажденные сливки снижают температуру творога, что препятствует дальнейшему повышению кислотности готового продукта.
Перечисленные преимущества раздельного способа делают его экономически более выгодным, несмотря на необходимость проведения дополнительных операций (сепарирование молока и смешивание обезжиренного творога со сливками).
Нормализация молока по жиру и белковому титру. Производится только при выработке жирного творога из цельного молока, при раздельном способе эта операция заменяется сепарированием молока и последующим смешиванием получаемых сливок с обезжиренным творогом.
Пастеризация молока. Температура пастеризации 72-74°С, выдержка 20 с. При этом режиме сывороточные белки не подвергаются заметной тепловой денатурации и при выработке творога полностью переходят в сыворотку.
Пастеризация при температуре 78-80°С с выдержкой 20-30 с увеличивает надежность пастеризации молока и получаемого из него творога и несколько увеличивает выход продукта за счет коагулирующих при этой температуре термолабильных сывороточных белков.
Заквашивание молока. Закваску из чистых культур мезофильных стрептококков в холодное время года вносят в молоко при температуре его 30-32°С (в расчете на возможное охлаждение), а в теплое - при 28-30°С. При ускоренном способе сквашивания, когда используют смесь культур мезофильных и термофильных стрептококков, устанавливают температуры молока соответственно 38 и 35° С.
Применение стрептококковой закваски в производстве творога основывается на том, что кислотообразующая способность ее гарантирует получение готового продукта с кислотностью в пределах требований к продукту высшего сорта, т. е. не более 200°Т. Излишняя кислотность снижает качество творога, он переводится в I сорт или становится нестандартным.
Однако, несмотря на использование только стрептококковой закваски, в готовом продукте обнаруживаются термоустойчивые молочнокислые палочки. Они постоянно присутствуют в твороге и как раз вызывают самый распространенный порок свежего творога - излишнюю кислотность. Источником загрязнения творога молочнокислыми палочками является пересадочная закваска.
Для устранения причины, вызывающей появление этого порока, рекомендуется при заквашивании вносить в молоко не 5% (к объему молока) вторичной, а 2% первичной стрептококковой закваски. В этом случае в течение всего процесса выработки творога в заквашенном молоке и сгустке преобладают молочнокислые стрептококки (1,4-2 млрд./г), а количество термоустойчивых палочек едва достигает 30 млн./г и не может существенно (за пределы норм высшего сорта) повысить кислотность творога.
Для улучшения качества творога предложено также использовать непосредственно лабораторную закваску (приготовленную на стерилизованном молоке) в количестве всего 0,8%. При этом существенного замедления процесса сквашивания не наблюдается, но гарантировано получение продукта высокого качества.
При сычужно-кислотном способе производства творога кроме бактериальной закваски в молоко вносят сычужный фермент из расчета 1 г/т молока. Сычужный фермент снижает кислотность сгустка, повышает его плотность к моменту обработки. Одновременно с сычужным ферментом в заквашенное молоко вносят 40%-ный раствор хлористого кальция (500 г безводной соли на 1 т молока). После внесения сычужного фермента и хлористого кальция молоко оставляют в покое до полного сквашивания.
Сквашивание молока. В заквашенном молоке как результат жизнедеятельности молочнокислых микроорганизмов происходит нарастание кислотности. Химизм воздействия молочной кислоты на казеинаткальцийфосфатный комплекс молока в процессе сквашивания молока при выработке творога аналогичен описанному ранее в технологии кисломолочных продуктов. Но при изготовлении творога параллельно действует и внесенный сычужный фермент, поэтому происходит совместная кислотная и сычужная коагуляция казеина. Частичное превращение казеина в параказеин под влиянием сычужного фермента, по существу, предшествует кислотной коагуляции. Поскольку казеин при переходе в параказеин смещает свою изоэлектрическую точку с рН 4,6 до 5,2, образование сгустка происходит при более низкой титруемой кислотности, чем при чисто кислотном осаждении, что, в конечном счете, приводит к меньшей кислотности получаемого творога. Кроме того, в образовании структуры сгустка при сычужно-кислотном способе осаждения участвуют кальциевые мостики, образующиеся между частицами параказеина, как это происходит при сычужной коагуляции в производстве сычужных сыров. Наличие кальциевых мостиков, упрочняющих структуру сгустка, приводит к образованию более плотного сгустка, что в свою очередь предупреждает распыление его при механическом дроблении, в известной мере благоприятно отражаясь на повышении выхода творога.
При сычужно-кислотном способе производства творога процесс сквашивания длится 4-6 ч с момента внесения в молоко закваски, при ускоренном способе с использованием активной кислотообразующей закваски - 3-4 ч, а при предварительном подкислении молока сывороткой-3-3,5 ч. Кислотность молока при производстве жирного и полужирного творога достигает 66-70, нежирного - 58-60°Т. Конец сквашивания молока определяют по пробе на излом и по виду выделяющейся из сгустка сыворотки. Если при разделении сгустка ложкой или шпателем образуются ровные края разлома с блестящими гладкими поверхностями, значит сгусток готов к дальнейшей обработке. Сыворотка, выделяющаяся в месте разлома, должна быть прозрачной, светло-зеленого цвета.
Обработка сгустка. Очень важно правильно определить момент окончания сквашивания молока перед началом обработки. При обработке недостаточно сквашенного сгустка повышаются потери творога, так как часть его в виде «пыли» переходит в сыворотку. Из переквашенного сгустка получается кислый творог мажущейся консистенции. При правильном сквашивании молока образуется сгусток в виде плотного геля, самопроизвольно выделяющего сыворотку (процесс синерезиса). Разрезка сгустка, увеличивая его поверхность, ускоряет выделение сыворотки.
Готовый сгусток разрезают проволочными ножами на кубики размером по ребру около 2 см; сначала разрезают по длине ванны на горизонтальные слои, затем по длине и ширине на вертикальные. Разрезанный таким образом сгусток оставляют в покое на 1 ч для нарастания кислотности, способствующей наиболее полному выделению сыворотки.
Отделение сыворотки от сгустка. Известно, что в изоэлектрическом состоянии белковые вещества имеют минимум растворимости и минимум набухания. Самопроизвольное отделение сыворотки от сгустка в процессе синерезиса наиболее активно происходит при рН 4,6-4,7, т. е. в изоэлектрической точке казеина, а для параказеина (при сычужной коагуляции) при рН 5,0-5,2. При смешанном сычужно-кислотном способе производства творога изоэлектрическая точка сгустка сдвинута в сторону параказеина и оптимальное значение рН составляет около 4,7-5,0.
При удалении свободно выделившейся в результате синерезиса сыворотки часть ее задерживается в сгустке. Для окончательного отделения сыворотки от сгустка и получения творога со стандартным содержанием влаги применяют самопрессование, а затем принудительное прессование. Самопрессование сгустка, выложенного из ванны в мешочки из синтетической ткани (лавсан), миткаля или марли, ведется на пресс-тележках, на которых имеется приспособление и для принудительного прессования. Самопрессование продолжается не менее 1 ч, при этом мешочки с творогом перекладывают. Температура помещения не должна быть выше 160С. После самопрессования мешочки с продуктом для окончательной отпрессовки творога равномерно раскладывают по дну пресс-тележки и покрывают металлической перфорированной пластиной, которая через специальную раму воспринимает давление от винта пресса.
Этот способ наиболее простой, но и самый трудоемкий. В настоящее время преимущественно применяют творогоизготовители с прессующей ванной.
Творогоизготовитель (рис. 1) предназначен для сквашивания молока, получения творожного сгустка, разрезания его, удаления свободно отделившейся сыворотки и окончательной отпрессовки творожной массы. Он состоит из двустенных ванн с краном для выпуска сыворотки и люком для выгрузки творога. Над творожной ванной смонтирована прессующая ванна с перфорированными стенками, на которую надевается фильтрующая ткань; внутри этой ванны установлен патрубок для откачивания сыворотки.
Молоко заливают в ванну для сквашивания, вносят закваску и фермент. Образовавшийся творожный сгусток разрезают, как было указано выше, и через некоторое время сливают часть выделившейся сыворотки с помощью отборника, опускаемого в ванну. По окончании слива сыворотки отборник вынимают и включают гидропривод, опускающий прессующую ванну вниз со скоростью 2-4 мм/мин.
При этом сыворотка проходит через фильтрующую ткань и перфорированную обшивку внутрь ванны, откуда периодически откачивается насосом. По окончании процесса прессующую ванну поднимают, открывают люк и творог выгружают в тележку.
Применение творогоизготовителей с прессующей ванной по сравнению с обычным способом прессования в мешочках дает большой экономический эффект: сокращаются затраты труда, механизируется процесс, уменьшается потребность в производственных площадях и в фильтрующем материале. Все это в конечном счете повышает производительность труда и снижает себестоимость продукта.
За последнее время освоено непрерывное производство творога сепарированием сквашенного молока на специальном творожном сепараторе (рис. 2). Рабочей частью сепаратора является барабан с комплектом конических тарелок (52 шт.). Барабан покрыт защитным сферической формы кожухом, опирающимся через промежуточный кожух на кольцевую чашу, служащую для улавливания творога, выбрасываемого из сопел диаметром от 0,5 до 0,7 мм. Барабан вращается со скоростью 5500 об/мин.
Водород" href="/text/category/vodorod/" rel="bookmark">водородных ионов, которая не должна превышать 4,50.
Ранее было указано, что наиболее благоприятные условия отделения сыворотки от сгустка наступают при значении рН, близком к изоэлектрической точке казеина, когда происходит наиболее полное соединение и уплотнение его частиц. При сепарировании сквашенного молока частицы осадка, находящиеся в электронейтральном состоянии, под влиянием центробежных сил могут образовывать в периферийной части барабана массу плотной консистенции, которая не будет выброшена через сопла сепаратора, причем неизбежно быстрое засорение сопел. Чтобы избежать этого, необходимо при сквашивании перейти рубеж изоэлектрического состояния казеина в сторону более кислой реакции. Опытным путем установлено, что сыворотка должна иметь рН в пределах 4,5-4,3.
В этом случае частицы казеина, размер которых прокалиброван сетчатым фильтром (рис. 3), начинают приобретать положительный заряд, т. е. противоположный заряду частиц казеина в свежем молоке. Одноименно заряженные частицы при соприкосновении друг с другом не образуют плотной массы и поэтому легко выводятся из барабана сепаратора, не забивая сопел.
Охлаждение творога. Отпрессованный творог необходимо немедленно охладить до 3-8°С, чтобы прекратить молочнокислое брожение с нарастанием излишней кислотности. Охлаждение в зависимости от вида технологического оборудования, применяемого для производства творога, осуществляется различными приемами.
При способе выкладки сгустка в мешочки прессование можно совместить с охлаждением, помещая пресс-тележки в холодильную камеру. Для этого применяют также специальный пресс-охладитель, представляющий собой трубчатый барабан, в который загружают мешки с творожной массой и по трубам пропускают охлажденный рассол; при медленном вращении барабана мешки перемещаются, происходит одновременно отделение сыворотки и охлаждение творога.
При использовании творогоизготовителя с прессующей ванной охлаждение творога совмещается с прессованием: для этого в межстенное пространство ванны пропускают хладагент. Окончательно готовый творог охлаждают в холодильной камере или же на специальном цилиндрическом охладителе. В охладителе конструкции Локтюхова внутри цилиндра циркулирует рассол температурой -7°С. На поверхность цилиндра с одной стороны через зазор размером 0,4-0,5 мм валиком наносится тонкий слой творога; на противоположной стороне цилиндра охлажденный слой творога ножом срезается с поверхности и падает в тележку, в которой подается на расфасовку.
Более совершенны одно - и двухцилиндровые творогоохладители ОТВ-500 и ОТД-650 (рис. 4).
Охлажденный творог непрерывно снимается ножами с поверхности цилиндра и, перемещаемый двумя шнековыми витками барабана, входит через отверстие в крышке цилиндра. В рубашке цилиндра по спиральному каналу циркулирует рассол.
Охлажденный с 28 до 10°С творог поступает на расфасовку.
Расфасовка, упаковка и хранение творога. Творог жирный, полужирный и нежирный для розничной продажи расфасовывают в бруски весом 250, 500 и 1000 г. Температура творога, направляемого на мелкую расфасовку, не должна превышать 6°С. Расфасовывают его на автоматах ОФЗ (рис. 5) и фасовочных полуавтоматах с формующими насадками. Бруски творога, завернутые в пергамент или бесцветный целлофан, укладывают в картонные или деревянные коробки. Расфасованный творог охлаждают и хранят до реализации в холодильных камерах при температуре около нуля, но не выше 4° С.
Следует иметь в виду, что при указанной температуре хранения качество творога понижается вследствие ферментативных процессов, дальнейшего распада лактозы и белковых веществ. Как известно, деятельность ферментов не прекращается даже при низких положительных температурах. Поэтому творог после двух-трехсуточного хранения при 4-6° С переводят из высшего сорта в первый; при продолжительном хранении качество его еще более ухудшается.
Для длительного хранения и резервирования летнего творога его замораживают. Обратимость этого процесса наиболее полная, если замораживание ведется при низких температурах. В этих условиях вода в твороге замерзает в виде мелких кристаллов, не нарушая его структуру. В противоположность этому медленное замораживание сопровождается перераспределением влаги в твороге с образованием крупных кристаллов. При дефростации быстрозамороженного творога его первоначальная консистенция и структура восстанавливаются. Более того, некоторые недостатки консистенции творога (например, крупитчатость) при дефростации устраняются. Это объясняется тем, что мелкие кристаллы льда, образующиеся при замораживании внутри крупинок творога, разрушают их, создается мелкозернистая структура, воспринимаемая на вкус как однородная масса.
Творог в мелкой расфасовке (0,5 кг) и в блоках (10 кг) замораживают в морозильных камерах при температуре ° С или же в скороморозильных аппаратах.
Зерненый творог. Эта разновидность творога вырабатывается у нас в промышленном масштабе с 1965 г. Зерненый творог со сливками имеет зернистую структуру, приятный кисломолочный вкус. В 100 г зерненого творога содержится 16-20 г белка, 6 г жира, 0,8-2,0 г минеральных и других веществ.
Рис. 6. Технологическая схема производства зерненого творога со сливками:
1- танк для молока; 2- центробежный насос; 3 - балансировочный бачок; 4- насос пастеризационной установки; 5 - пастеризационная установка; 6 - сепаратор-сливкоотделитель; 7-танк для сбора сливок; 8-насос подачи сливок в гомогенизатор; 9- гомогенизатор; 10- пастеризатор для сливок; 11 -танк для выдержки и хранения сливок; 12 - насос подачи сливок в автомат-дозатор; 13 -ванна с мешалкой; 14 - насос для подачи зерна на обсушку; 15 - виброустановка для обсушки зерна; 16 - тележки; 17 - подъемник тележек; 18 - автомат-дозатор зерна и сливок; 19 - заквасочник для материнской закваски; 20 - установка для производственной закваски; 21 - насос для подачи закваски в ванну; 22 - насос центробежный для подачи воды; 23 - танк для подготовки воды; 24 - охладительная установка.
Благодаря тому что сливки, как и при раздельном способе выработки творога, добавляются к обезжиренному продукту, они концентрируются на поверхности зерен, и по вкусу этот продукт напоминает высокожирный творог. Схема технологического процесса показана на рис. 6. Свежее кондиционное молоко пастеризуют в пластинчатой установке при 72-74°С с выдержкой 18-20 с и сепарируют. В обезжиренное молоко вносят закваску в количестве до 5%, состоящую из гомоферментативных молочнокислых стрептококков и ароматобразующих культур. Одновременно вносят сычужный фермент из расчета 0,5- 1,0 г и раствор хлористого кальция из расчета 400 г на 1т молока. Применяют два режима сквашивания: кратковременный и длительный. При кратковременном режиме температура сквашивания 30-32°С, продолжительность процесса 6-8 ч; при длительном соответственно 21-23° С и 12-18 ч.
Готовность сгустка определяют по нарастанию кислотности сыворотки. Сгусток должен быть прочным с ровными краями на изломе, сыворотка отделяется в виде прозрачной зеленоватой жидкости.
Готовый сгусток разрезают проволочными ножами на кубики размером 12-13 мм по ребру (вначале разрезают по длине на горизонтальные слои, затем по ширине на вертикальные), после чего оставляют в покое на 20-30 мин для выделения сыворотки и уплотнения сгустка. Затем в ванну добавляют воду температурой 46-48°С в таком количестве, чтобы повысить уровень содержимого в ванне на 50-60 мм. Вода на 2-3°С повышает температуру сгустка, снижает кислотность сыворотки с 40-42 до 36-38°Т. После добавления воды зерно тщательно перемешивают и постепенно подогревают, вводя в межстенное пространство сырной ванны горячую воду; температура содержимого в ванне должна повышаться на 1° за каждые 10 мин и достигнуть 33° С.
Последующее подогревание до 48-55°С нужно вести быстрее, чтобы температура повышалась на 1° за каждые 2 мин. По достижении указанной температуры зерно вымешивают в течение часа для уплотнения. Готовое предварительно охлажденное водопроводной водой зерно при легком сжатии в руке должно сохранять форму. Затем сыворотку удаляют и приступают к промывке и одновременному охлаждению зерна. Сначала в зерно добавляют воду температурой 16-17°С, перемешивают его 15-20 мин, затем сливают воду; для второй промывки добавляют воду температурой 2-4°С, выдерживают зерно в воде такое же время, после чего ее сливают.
Промытое зерно оставляют в ванне на 1-2 ч, а затем перекладывают в тележки с перфорированным дном, в которых его помещают на 10 -12 ч в холодильную камеру при температуре воздуха не выше 5-10°С. К обсушенному зерну добавляют сливки жирностью 20-30% и кислотностью не выше 17°Т. Сливки предварительно пастеризуют при 33-35°С с выдержкой 20-30 мин, затем охлаждают до 26-30°С, гомогенизируют при давлении 12,5-15,0 МПа, окончательно охлаждают до 2-4°С. Подсоленные сливки вносят в общую массу зерна или порционно, в каждый стаканчик при расфасовке.
Зерненый творог со сливками расфасовывают в мелкую тару - полимерные стаканчики емкостью 200, 250 и 500 г и в крупную тару из нержавеющей стали или картонные коробки по 20 кг с прокладкой из бумаги, покрытой полимерной пленкой.
Хранить зерненый творог при комнатной температуре (16-20°С) следует не более суток, а при 8-10°С -не более 6 суток. Стойкость зерненого творога при хранении несколько ниже стойкости обычного творога вследствие того, что из первого тщательной промывкой удалена молочная кислота, которая, как известно, обладает консервирующим свойством и противодействует развитию гнилостных процессов.
При хранении как в комнатных условиях, так и в холодильнике в зерненом твороге могут интенсивно развиваться дрожжи. Длительное хранение зерненого творога возможно только в рассоле (10% NaCl) при 6-8°С в течение 5 месяцев без существенного изменения органолептических свойств.
Творожные продукты
Из творога с добавлением сахара, соли, вкусовых и ароматических веществ (какао, кофе, цукаты, сухие фрукты, изюм, тмин, укроп и др.) вырабатывают сырки, сырковую массу, торты, кремы, а также полуфабрикаты - вареники, сырники, тесто для сырников и др., для которых в качестве дополнительного сырья используют пшеничную муку, куриные яйца, крахмал и другие продукты.
Товарная классификация творожных изделий делит их на четыре группы - с повышенным содержанием жира (20-26%), жирные (15%), полужирные (до 8%) и обезжиренные; по вкусовым добавкам - на сладкие с содержанием сахара от 13 до 26% и соленые с содержанием соли - от 1,5 до 2,5%. Творожные сырки и творожную массу указанных видов можно вырабатывать с добавлением и без добавления вкусовых веществ. Количество отдельных компонентов, входящих в состав творожных изделий, регламентируется рецептурой на определенные виды этой продукции и требованиями РТУ.
Технологический процесс производства творожных изделий заключается в предварительном измельчении творога на вальцовых машинах (рис. 7) для получения однородной творожной массы и последующем смешивании ее в месильных машинах с остальными ингредиентами. Продолжительность перемешивания зависит от конструкции и емкости машины, скорости вращения мешалки, а также от температуры и консистенции входящих компонентов.
По окончании обработки полученную массу охлаждают на цилиндрическом охладителе или в холодильных камерах до температуры не выше 6° С и затем направляют на расфасовку.
Упаковывают творожные изделия, за исключением глазированных сырков, тортов, кремов, в пергамент или полимерные упаковочные материалы; глазированные сырки - в алюминиевую или оловянную фольгу с опоясывающей этикеткой; творожные торты - в картонные коробки, дно которых предварительно выстилают пергаментом с узорами на краях. Творожные кремы расфасовывают в стаканчики или тубы из полистирола или других полимерных материалов, разрешенных для упаковки пищевых продуктов.
Рис. 7. Вальцовая машина:
1- бункер транспортера; 2 - шнек; 3 - приемный бункер; 4 - штурвал регулирования зазора валков; 5 - валки; 6 - опора станины.
Готовые творожные изделия должны отвечать требованиям действующих РТУ по кислотности, содержанию жира, сахара и соли, иметь вкус и запах чистый, кисломолочный, с ярко выраженным вкусом и ароматом добавляемых вкусовых и ароматических веществ, консистенцию однородную, нежную, в меру плотную, цвет белый, с кремовым оттенком или обусловленный добавкой вкусовых веществ, например какао,- шоколада, равномерный по всей массе.
Из наиболее часто встречающихся пороков вкуса творога и творожных изделий следует назвать излишне кислый вкус, возникающий при накоплении избытка молочной кислоты, дрожжевой привкус, особенно в сладкой творожной массе и сырках, появляющийся как следствие спиртового брожения, вызываемого дрожжами. Горечь в продукте - это результат загрязнения продукта гнилостными бактериями. Уксуснокислый вкус и запах вызываются развитием уксуснокислых бактерий. Распад жировых веществ под действием как гнилостных бактерий, так и плесеней также ведет к появлению пороков вкуса.
Из пороков консистенции наиболее часто встречается крупитчатость, указывающая на нарушение технологии производства и обработки творога.
Во всех случаях, чтобы предупредить появление пороков в продукте, необходимо поддерживать высокую санитарную культуру производства закваски и технологического процесса.
Пасты «Здоровье» и ацидофильная
Молочно-белковая паста «Здоровье» вырабатывается из пастеризованного обезжиренного молока сквашиванием его приготовленной на чистых культурах молочнокислых бактерий закваской и добавлением сливок, сахара, плодово-ягодных сиропов, витамина С (в виде сиропа из шиповника) и соли. Продукт предназначается для потребления в пищу непосредственно, как высокопитательный белковый концентрат, или в качестве приправы к блюдам. Он обладает чистым кисломолочным вкусом с выраженным ароматом добавляемых вкусовых веществ и по консистенции напоминает густую сметану.
Выпускается паста «Здоровье» нескольких видов: 5%-ной жирности, нежирная и с наполнителями - соленая (соли 0,2%) и сладкая (сахара 10-13%); содержание влаги от 75 до 85%, в зависимости от вида пасты.
Технологический процесс заключается в следующем. Обезжиренное молоко пастеризуют при температуре 80°С с выдержкой 20-30 с. Затем охлаждают до температуры заквашивания 36-38°С и вносят 5-8% закваски, приготовленной на смеси культур термофильных и мезофильных рас молочнокислых стрептококков в соотношении 1:1. Сквашивание ведется до кислотности 80-85°Т в течение 10-12 ч. Готовый сгусток разрезают на кубики размером по ребру около 2 см. Разрезанный сгусток оставляют в покое на 40-50 мин.
Удаление сыворотки и прессование сгустка производят теми же способами, как и при выработке творога.
Для получения однородной консистенции молочно-белковую основу пропускают через коллоидную мельницу, а затем добавляют в нее сироп, сливки, сахар или соль, в зависимости от вида пасты. Готовый продукт расфасовывают в различную тару: широкогорлые стеклянные банки, бутылки или тару из полимерных материалов.
Расфасованную продукцию охлаждают до температуры не выше 8°С и хранят не более 36 ч.
Для производства пасты «Здоровье» ВНИМИ разработана поточная линия, комплектуемая в основном из технологического оборудования, применяемого для производства творога.
Ацидофильная паста - лечебный кисломолочный продукт - представляет собой не только белковый, но и бактериальный концентрат ацидофильных палочек. Пасту вырабатывают из цельного и обезжиренного молока, применяя в качестве закваски чистые культуры ацидофильной палочки. В пасту добавляют сахар и фруктово-ягодные сиропы.
Выпускают пасту ацидофильную сладкую 8 и 4%-ной жирности и нежирную.
Ацидофильная паста предназначается для непосредственного потребления в пищу. Кроме того, ее рекомендуется применять в качестве лечебного продукта при ряде желудочно-кишечных заболеваний.
Пасту можно вырабатывать двумя способами: прессованием сгустка, получаемого сквашиванием молока, и из предварительно сгущенного молока, как это показано на помещаемой ниже схеме.
Кондиционное цельное молоко нормализуют до содержания в нем жира 2,3% для 4%-ной пасты и до 3,4% для пасты с содержанием жира 8%. Молоко (нормализованное, обезжиренное) пастеризуют в пастеризационных установках при температуре 85-90°С с выдержкой в ваннах в течение 15 мин, а затем в тех же ваннах охлаждают до температуры заквашивания (40-42°С).
При производстве пасты из предварительно сгущенного молока пастеризованное молоко направляют в вакуум-аппарат . Молоко сгущают в возможно короткий срок при температуре 50-55°С, повышая ее в конце сгущения до 55-60°С. Содержание сухих веществ в сгущенном молоке, нормализованном по жиру, должно быть не менее 29% и в обезжиренном сгущенном молоке не менее 23%. Сгущенное молоко охлаждают до температуры заквашивания (38- 40°С).
Заквашивают молоко приготовленной на ацидофильной палочке закваской, взятой в количестве 5% от веса молока. Заквашенное молоко тщательно перемешивают; сквашивание ведут до получения плотного сгустка. Кислотность сгустка из нормализованного по жиру молока должна быть в пределах 80-90°Т и из сгущенного 180-200°Т.
Сгусток выкладывают в бязевые или лавсановые мешки емкостью 12-14 л для самопрессования при температуре 6-8°С, а затем прессуют (в пресс-тележках, творожных прессах) до требуемой влажности.
К отпрессованной и сгущенной пасте добавляют сахарный сироп концентрацией 66% и смешивают в месильной машине до получения однородной консистенции.
Пасту расфасовывают в стеклянные банки или тару из полимерных материалов и направляют в холодильную камеру для охлаждения до 8°С.
Готовый продукт должен иметь вкус и запах чистый кисломолочный, для пасты из подсгущенного молока - с привкусом, свойственным сгущенному молоку, консистенцию нежную, пастообразную, однородную. Содержание влаги в сладкой пасте 8%-ной жирности 60%, 4 %-ной жирности- 65%, нежирной - 80%; содержание сахара соответственно 24, 20 и 12%. Кислотность во всех случаях не более 200°Т. Не допускается содержание в ацидофильной пасте патогенных микроорганизмов; титр кишечной палочки должен быть не ниже 0,3 мл.
Сметана
Сметана - национальный русский кисломолочный продукт, содержащий 20, 25, 30 и 36% жира. В сметане диетической жира 10, любительской 40%.
Технологический процесс производства сметаны состоит из следующих операций: сепарирования молока и получения сливок, нормализации сливок по жиру, пастеризации, гомогенизации, охлаждения сливок до температуры сквашивания, внесения закваски, сквашивания сливок, охлаждения и созревания сметаны, расфасовки и хранения готового продукта.
Молоко сепарируют при 40-45°С с получением сливок жирностью не менее 32%; окончательно нормализуют сливки по жиру до 31,6%, из расчета получения после внесения закваски в количестве 5% готового продукта жирностью 30%. При выработке продукта 36%-ной жирности сливки нормализуют до 37,9%. Соответствующий расчет делается и при других жирностях сметаны. Пастеризуют сливки при 85-95°С с выдержкой 15-20 с.
Сливки рекомендуется гомогенизировать при температуре 50- 70°С и давлении 7,0-8,0 МПа. Сметана из гомогенизированных сливок имеет более плотную консистенцию, как и кисломолочные напитки, выработанные резервуарным способом с применением гомогенизации молока.
После гомогенизации сливки немедленно охлаждают на пластинчатом или трубчатом охладителе до температуры заквашивания (в теплое время года 18, а в холодное 22°С). В качестве закваски применяют чистые культуры мезофильных стрептококков (Str. lactis, Str. cremoris) и ароматообразователи (Str. diacetilactis). Количество вносимой закваски существенно влияет на продолжительность сквашивания.
Сквашивание сливок в зависимости от температуры продолжается 14-16 ч. В первые 3 ч производится перемешивание сливок через каждый час, а затем их оставляют в покое до конца сквашивания. Конец сквашивания определяют по нарастанию кислотности до 65-75°Т в летнее время и 80-85° Т в зимнее.
Свежеприготовленная сметана может быть расфасована в мелкую или крупную тару; в этой же таре проводится охлаждение и созревание сметаны. Для охлаждения и созревания используют также большие емкости - ванны ВДП, двустенные резервуары, в этом случае расфасовывают уже готовую сметану. В любом случае охлаждение сочетается с созреванием сметаны, которое продолжается при 5-8°С в течение 24-48 ч. Созревание сметаны, заранее расфасованной в мелкую тару в холодильной камере при 2-4°С, может быть закончено в течение 24-28 ч. При быстром охлаждении заквашенных сливок до 5-6°С процесс созревания можно сократить до 6-8 ч.
Сущность процесса созревания при охлаждении сметаны заключается в кристаллизации глицеридов молочного жира, отвердевании оболочек жировых шариков и в совместной кислотной коагуляции казеина и термолабильных сывороточных белков плазмы, денатурированных в процессе высокотемпературной пастеризации сливок. Это основные процессы структурообразования сметаны, протекающего во времени.
Жировая фаза сметаны составляет более 4/3 по объему, ее физическое состояние, связанное с кристаллизацией, отвердеванием и образованием полиморфных структур, имеет решающее значение для консистенции сметаны. Так, по данным Твердохлеб, предварительное глубокое охлаждение сливок до 2-6°С перед сквашиванием и выдержка в течение 2-3 ч позволяют достичь высокой степени отвердевания жира и образования метастабильных форм кристаллов глицеридов, как это происходит при физическом созревании сливок в маслоделии. Подобного рода обработка сливок позволяет улучшить консистенцию сметаны и сократить продолжительность созревания.
На консистенции сметаны помимо отвердевания глицеридов молочного жира в процессе охлаждения и созревания ее отражается и степень дисперсности жировых частиц. На развитой поверхности оболочек жировых частиц, особенно после гомогенизации, белковые вещества включаются в структурообразование. При кислой реакции среды, т. е. при рН ниже 4,6-4,7, казеин вновь приобретает заряд (противоположный), происходит коллоидное растворение и нарушение гелевой структуры, разжижение сгустка. В этом случае сметана приобретает жидкую консистенцию, которая усиливается по мере смещения рН от изоэлектрической точки, что наблюдается при переквашивании сметаны.
На консистенцию сметаны, кроме того, оказывает большое влияние концентрация белков в плазме сметаны, что зависит от содержания казеина в исходном молоке. Увеличение содержания казеина даже на десятые доли процента может оказать ощутимое влияние на консистенцию сметаны при прочих равных условиях.
Денатурированные белковые вещества сыворотки также могут участвовать в образовании белковой стромы при кислотной коагуляции казеина. При коагуляции белковых веществ образующиеся структуры не обладают достаточно прочными связями, поэтому всякое механическое воздействие как в момент образования структуры, так и особенно на конечном этапе ее завершения должно быть сведено к минимуму.
Хранить сметану до реализации следует в холодильной камере при температуре не выше 2-40С и относительной влажности 75- 80%.
Сметана, направляемая в реализацию, должна соответствовать требованиям действующих РТУ: вкус и запах для высшего сорта чистый кисломолочный без посторонних привкусов и запахов; для первого сорта допускаются слабо выраженные привкусы кормовой, топленого масла, тары (дерева), наличие слабой горечи; консистенция сметаны высшего сорта однородная, в меру густая без крупинок жира и белка (творога), для первого сорта допускается недостаточно густая, слегка комковатая, с наличием крупинок и легкой тягучестью. Кислотность для высшего сорта 65-90, для первого сорта 65-110°Т.
В ассортимент сметаны входят еще две разновидности - «Диетическая» и «Любительская».
Особенности технологии производства диетической сметаны заключаются в следующем. Заквашенные специальной закваской молочнокислых бактерий, способных синтезировать витамин В, пастеризованные и гомогенизированные сливки жирностью 10% разливают в широкогорлые стеклянные бутылочки и стаканы или в пластмассовые стаканы и затем сквашивают в термостатах при 28°С до кислотности 65-70°Т, после чего охлаждают сметану в холодильной камере при температуре 5-6°С и выдерживают для созревания в течение 12-16 ч. Охлаждение сметаны заканчивают, когда температура ее понизится до 8°С, после чего ее направляют на реализацию.
Для производства любительской сметаны исходные сливки получают жирностью не менее 44,5% с последующим снижением ее закваской до 40%. Сливки пастеризуют при 87°С с выдержкой 20 мин или при 92-99°С с выдержкой 10-20 мин, что придает сметане специфический, так называемый «ореховый», привкус. Пастеризованные сливки гомогенизируют при 50°С и давлении 10 МПа. Закваска для любительской сметаны из штаммов мезофильных и термофильных рас в соотношении 1: 1 вносится в количестве до 10% от веса сливок при 45-50°С. По достижении требуемой кислотности (не ниже 55°Т) сметану охлаждают на цилиндрическом охладителе для творога до 4-6°С и расфасовывают на автоматах с упаковкой брикетов весом 100 г в пергамент или другой материал. Уложенные в картонные коробки брикеты сметаны помещают в холодильные камеры с температурой 0-6°С и выдерживают для созревания не менее 6-12 ч. Готовый продукт имеет плотную однородную консистенцию, сохраняет форму заданного брикета, вкус чистый кисломолочный с явно выраженным привкусом пастеризованных сливок.
2.5. О борудование для производства творога
Оборудование для производства творога и творожных изделий можно разделить на оборудование для получения и обработки сгустка и оборудование для охлаждения, перетирания и перемешивания творожной массы. Конструктивные особенности оборудования первой группы определяются способом производства творога.
При производстве творога традиционным способом нормализованное молоко сквашивается в аппаратах непрерывного или периодического действия. К аппаратам непрерывного действия относят многосекционный творогоизготовитель и коагуляторы, периодического - творогоизготовители и творожные ванны. После сквашивания молока отделение сыворотки от образовавшегося сгустка осуществляется либо в самих творогоизготовителях, либо в ваннах самопрессования, пресс-тележках или барабанных обезвоживателях.
При производстве творога раздельным способом сквашивание обезжиренного молока и образование сгустка осуществляются в емкостях, а для отделения сыворотки от творожного сгустка применяют сепараторы для обезвоживания творожного сгустка.
В линиях по производству творога малой и средней мощности вместо сепараторов используют ванны самопрессования и пресс-тележки. В комплектных технологических линиях по производству творога, имеющих более высокую производительность (2,5...5 м3/ч по перерабатываемому молоку), творожный сгусток получают в емкостях, а затем последовательно пропускают его через аппарат тепловой обработки и сепаратор для обезвоживания творожного сгустка.
Творог охлаждается в охладителях открытого и закрытого типов, а также комбинированных аппаратах, позволяющих совмещать эту операцию с обезвоживанием творожного сгустка. Для перетирания и перемешивания творожной массы используют вальцовки, смесители и куттеры.
Традиционный способ производства творога позволяет получить требуемую жирность продукта непосредственно в процессе переработки молока соответствующей жирности.
При раздельном способе необходимая жирность продукта обеспечивается смешиванием обезжиренного творога с соответствующим количеством охлажденных пастеризованных сливок. Охлажденные сливки резко снижают температуру творога, что препятствует повышению кислотности готового продукта и улучшает его вкусовые качества.
В процессе переработки молока на творог часть жира теряется. При этом чем больше исходная жирность сырья, тем больше относительные потери жира.
Таким образом, несмотря на необходимость проведения дополнительных операций (сепарирование молока и смешивание обезжиренного творога со сливками), раздельный способ производства творога имеет определенные преимущества по сравнению с традиционными.
2.5.1. Поточно-технологические линии производства творога
Особенностью оборудования, входящего в поточно-технологические линии производства творога как традиционным, так и раздельным способами, является их согласованность по часовой производительности. Обычно такие линии имеют производительность по творогу в пределах 500...600 кг/ч.
На рис. 2.5.1 показана технологическая схема линии производства творога раздельным способом в потоке.
Из емкости для хранения молоко насосом направляется в пластинчатую пастеризационно-охладительную установку. В сепараторе-молокоочистителе молоко очищается, а в сепараторе-сливкоотделителе разделяется на сливки и обезжиренное молоко.
В охладителе сливки охлаждаются и поступают в емкость для хранения, через межстенное пространство которой пропускают ледяную воду.
Рис. 2.5.1. Схема поточной линии производства творога раздельным способом:
1-ёмкость для хранения молока; 2,4-центробежные насосы; 3-уравнительный бак; 5-пластинчатый пастеризатор; 6-сепаратор-молокоочиститель; 7-сепаратор-сливкоотделитель; 8-охладитель для сливок; 9-ёмкость для хранения сливок; 10-ротационный насос; 11-ёмкость для сквашивания молока; 12-мембранный насос; 13-сепаратор для творога; 14-шнековый подъемник; 15-смеситель творога и сливок; 16-охладитель творога; 17-тележка для творога; 18-бак для сливок; 19-патрубок для поступления закваски, сычужного фермента и хлорида кальция
Обезжиренное молоко также хранят в емкостях. Через патрубки в них подают закваску, хлорид кальция и сычужный фермент. В этих емкостях обезжиренное молоко сквашивается и образуется творожный сгусток. Через двойной сетчатый фильтр насосом сгусток подается в сепаратор для отделения сыворотки и с помощью подъемника поступает в смеситель творога со сливками СТ-1. Готовый творог проходит через двухцилиндровый охладиОТД-1, где его температура снижается до 5...10˚С, и направляется на фасование.
Поточно-механизированные линии производства творога ЭПМЛПТ-2 и ОПМЛ-Т1 предназначены для получения творога на основе сквашивания нормализованного до необходимой жирности молока в емкостях с последующим подогревом сгустка и его обезвоживанием в потоке. Линии применяют на небольших предприятиях молочной промышленности, а также в подсобных хозяйствах (рис. 2.5.2).
Рис.2.5.2. Технологическая схема поточно-механизированной линии ЭПМЛПТ-2 производства творога:
1-ёмкость Я1-ОСВ; 2-винтовой насосный агрегат; 3-аппарат тепловой обработки сгустка; 4-обезвоживатель творожного сгустка; 5-бойлерная установка; 6-центробежный насос; 7-охладитель творога; 8-фасовочный автомат
В состав линии входят емкости из нержавеющей стали вместимостью 6,3 или 10 м3 для сквашивания молока; аппарат тепловой обработки сгустка для нагревания, выдержки и предварительного охлаждения продукта; обезвоживатель творожного сгустка; охладитель творога; фасовочный автомат; система управления и контроля.
Процесс производства творога начинается с заквашивания нормализованного молока в емкости. Готовый сгусток насосом подается в аппарат тепловой обработки, подогревается с помощью бойлерной установки, выдерживается и охлаждается. Из аппарата сгусток поступает в обезвоживатель творожного сгустка, где происходят отделение сыворотки и самопрессование творога. Отделившаяся сыворотка удаляется насосом для дальнейшей переработки или хранения. Из обезвоживателя творог подается в охладитель, где охлаждается, и поступает на фасовочный автомат.
Мойка оборудования и трубопроводов осуществляется циркуляционно. Производительность линий по творогу соответственно 110 и 70 кг/ч.
2.5.2 Технологический расчет оборудования для производства творога
Технологический расчет оборудования для производства творога зависит от объема перерабатываемого сырья. При переработке молока до 5 т в смену применяют традиционный способ производства творога с использованием творожных ванн различной вместимости. Творог из 20 т молока и больше целесообразно производить раздельным способом с помощью сепараторов для обезвоживания творожного сгустка.
Оборудование с периодическим циклом работы подбирают, исходя из сменной (м3 в смену) производительности ванн:
(2.5.1)
где: - рабочая вместимость ванн, м3; https://pandia.ru/text/78/521/images/image006_0.gif" width="31" height="25 src=">- продолжительность одного цикла переработки молока в творог, включающего в себя операции наполнения ванны, нагревания нормализованной смеси до температуры сквашивания (32 °С), сквашивания, выгрузки из ванны сгустка с сывороткой и ее мойки, ч.
Время наполнения ванны нормализованным молоком и его нагревания до температуры сквашивания зависит от графика организации технологических процессов и оборудования самой линии (температура поступающего в ванны молока, подача молочного насоса и т. д.).
Продолжительность выгрузки сгустка и сыворотки из ванны самотеком можно определить по формуле (2.1.5), используя соответствующий коэффициент расхода μ (0,85...0,9).
Время сквашивания можно принять равным 7...7,5 ч.
Расход теплоты и пара для нормализованной смеси в ваннах определяется по формулам (2.3.1) и (2.3.3).
Оборудование для охлаждения (охлаждения и прессования) подбирают по часовой производительности, указанной в его технической характеристике. Количество холода, необходимое для охлаждения творога (Дж/ч), находят по формуле
(2.5.2)
где: kх- коэффициент, учитывающий потери холода в окружающую среду (для открытых охладителей = 1,3, закрытых = 1,2); https://pandia.ru/text/78/521/images/image010_0.gif" width="19" height="23"> - удельная теплоемкость продукта, Дж/(кг °С); и https://pandia.ru/text/78/521/images/image011_0.gif" width="13" height="23"> = 25...30 °С) и выходе из него (t2 = 8...14 °С).
При расчете оборудования для производства творога раздельным способом технологические емкости подбирают с учетом их рабочей вместимости, времени работы и сменной производительности. Сепараторы для обезвоживания творожного сгустка, а также насосы для перекачивания сырья и готового продукта подбирают, исходя из их часовой подачи.
Существует два способа производства творога: традиционный и раздельный. Производство творога традиционным способом включает в себя следующие операции:
- нормализацию молока до требуемого состава;
- очистку и пастеризацию молока;
- заквашивание молока;
- сквашивание молока;
- разрезание сгустка;
- отделение сыворотки;
- самопрессование и прессование творога;
- охлаждение творога;
- фасование.
Аппаратурно-технологическая схема производства творога традиционным способом приведена на рис. 2.7. Молоко из емкости 1 подается сначала в уравнительный бачок 2, затем насосом 3 в секцию рекуперации пастеризационно-охладительной установки 5, где оно подогревается до температуры 35...40 °С и на сепаратор-очиститель 4.
Нормализованное и очищенное молоко направляют на пастеризацию при 78...80 °С с выдержкой 20...30 с. Пастеризованное молоко охлаждают в секции рекуперации пластинчатой пастеризационноохладительной установки 5 до температуры сквашивания (в теплое время года до 28...30 °С, в холодное - до 30...32 °С) и направляют в специальные ванны 6 на заквашивание.
В молоко вносят закваску, приготовленную в заквасочнике 10. Для ускорения выделения сыворотки сгусток разрезают специальными проволочными ножами на кубики (размер граней - 2 см). Для дальнейшего отделения сыворотки сгусток подвергают самопрессо-ванию и прессованию с использованием пресс-тележек 7. По окончании прессования творог немедленно направляют на охлаждение до температуры не выше 8 °С. С этой целью используют охладители разных конструкций, например двухцилиндровый охладитель 8. Готовый творог фасуют на машинах 9 в мелкую и крупную тару.
Рис. 2.7.
- 1 - емкость; 2 - уравнительный бачок; 3 - насос; 4 - сепаратор-очиститель;
- 5 - пастеризационно-охладительная установка; Б - ванна; 7 - пресс-тележка;
- 8 - охладитель; 9 - фасовочная машина; 10 - заквасочник
Аппаратурно-технологическая схема производства творога раздельным способом приведена на рис. 2.8. Молоко из емкости / подается насосом 2 в уравнительный бачок 3, из него насосом 2 в секцию рекуперации пластинчатой пастеризационно-охладительной установки 4 для подогрева до 40...45 °С.
Подогретое молоко поступает в сепаратор-сливкоотделитель 5, в котором разделяется на обезжиренное молоко и сливки с массовой долей жира не менее 50%. Сливки подаются сначала в промежуточную емкость 6, а затем насосом 7 в пластинчатую пастеризационноохладительную установку 8 , где они пастеризуются при температуре
85...90 °С с выдержкой 15...20 с, охлаждаются до 2...4 °С и направляются в двустенную емкость 9 на временное хранение до смешивания с творогом.
Обезжиренное молоко из сепаратора поступает в пластинчатую пастеризационно-охладительную установку 4, где оно сначала пастеризуется при температуре 78 °С с выдержкой 15...20 с, а затем охлаждается до 30...34 °С и направляется в резервуар //для сквашивания, снабженный специальной мешалкой. Закваска, приготовленная в заквасочнике 10, насосом 7подается в резервуар 11 для сквашивания. Сюда же поступают хлорид кальция и фермент; смесь тщательно перемешивают и оставляют для сквашивания. Полученный сгусток тщательно перемешивается и насосом 12 подается в пластинчатый теплообменник 13, где он сначала подогревается до 60...62 °С для лучшего отделения сыворотки, а затем охлаждается до 25...32 °С, благодаря чему он лучше разделяется на белковую часть и сыворотку. Из теплообменника 13 сгусток через сетчатый фильтр 14 под давлением подается в сепаратор-творогоизготовитель 15, где он разделяется на сыворотку и творог.
Обезжиренное

Рис. 2.8. Аппаратурно-технологическая схема производства творога раздельным способом: 1,6, 18 - емкости; 2, 7, 12 - насосы; 3 - уравнительный бачок; 4,8 - пастеризационноохладительные установки; 5 - сепаратор-сливкоотделитель; 9 - двустенная емкость;
- 10 - заквасочник; 11 - резервуар для сквашивания; 13 - теплообменник;
- 14 - сетчатый фильтр; 15 - сепаратор-творогоизготовитель; 1В - насос;
- 17 - охладитель; 19 - месильная машина; 20 - машина для фасования
Полученный обезжиренный творог подают специальным насосом 16 на охладитель /7 для охлаждения до 8 °С, а затем растирают на вальцовке до получения гомогенной консистенции. Охлажденный творог направляют в месильную машину 19, куда дозирующим насосом 7 подают пастеризованные охлажденные сливки из емкости 18 и все тщательно перемешивают. Готовый творог фасуют на машинах 20 и направляют в камеру хранения.
Мечта о собственном бизнесе есть у каждого из нас. Кто-то уже осуществил ее, а кто-то еще теряется в догадках, в каком направлении двигаться. Молочная промышленность – хороший вариант. К примеру, можно заняться производством творога. Однако не все так просто. Прежде всего, необходимо правильно подобрать оборудование для производства творога, об этом и пойдет речь в данной статье.
О пользе творога
Данный продукт хорош во всех отношениях. В его состав входят белки, которые очень хорошо усваиваются. Кроме того, в нем много кальция, необходимого человеческому организму (особенно маленьким детям). Творог, по сути, это уникальный продукт, его часто включают в различные диеты. В системе правильного питания он всегда присутствует. Рекомендуемая порция – 100 граммов в день. Чтобы иметь здоровые волосы, ногти и кожу, достаточно употреблять этот продукт три раза в неделю.
Особенности производства
Данный процесс проходит по следующей схеме:
1) Приемка цельного молока и его качественная оценка.
2) Предварительный подогрев и сепарация сырья.
3) Нормализация молока. Это необходимо для того, чтобы получить продукт определенной жирности. Следует отметить, что чаще всего производят творог 5%-ный и обезжиренный (с массовой долей жира в продукте 0,5-1%).
4) Пастеризация продукта и его охлаждение.
5) Добавление закваски в молоко и его сквашивание.
6) Разрезание образовавшегося сгустка и отделение сыворотки.
7) Прессование сгустка.
8) Охлаждение готового продукта.
9) Упаковывание и маркирование творога.
Необходимое оборудование
Рассмотрим, какое потребуется оборудование для производства творога:
1) Для приемки молока необходимо иметь большие резервуары, в которых продукт будет храниться до следующей стадии.
2) Потребуется пастеризатор-охладитель, в котором молоко подогревается, и сепаратор для производства творога, который отделяет сливки от молока.
3) Для процесса нормализации необходимы резервуары.
4) На стадии пастеризации и охлаждения используется тот же пастеризатор-охладитель, упомянутый во втором пункте.
5) Заквашивание производится в тех же резервуарах (еще одно их название – ванны для производства творога), в которые молоко поступает после нормализации.
6) Для разрезания сгустка нужен специальный нож. После этого необходимо слить образовавшуюся сыворотку в другой резервуар при помощи штуцера или сифона.
7) Для прессования творога потребуется пресс-тележка, обтянутая серпянкой. Здесь творог самопрессуется примерно в течение часа.
8) Охлаждение готового продукта производится в холодильных камерах.
9) Упаковка и маркировка творога осуществляются специальными автоматами, которые дозируют продукт, упаковывают его и наносят специальные отметки.
Автоматизированные установки
На сегодняшний день большим спросом пользуется автоматизированная линия для производства творога. Ее существенным преимуществом является то, что благодаря механизации процесса достаточно всего двух-трех человек обслуживающего персонала, а это существенная экономия на оплате труда.
Подобные установки способны производить до 3,5 тонн готового продукта (в пересчете на сырье – 24 тонны молока). Есть желание увеличить объем производства? Такое оборудование допускает организацию широкой линии из нескольких аппаратов, при этом поточность процесса сохраняется.
Таким образом, для того чтобы начать производство такого ценного продукта, необходимо закупить целый ряд аппаратов и правильно их разместить на территории цеха. Проще всего приобрести линию для производства творога, в которую входят все необходимые автоматы.