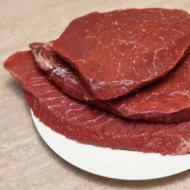
Производство творога традиционным способом. Технологическая линия производства творога
Чтобы сделать творог в домашних условиях какого-либо специализированного оборудования не потребуется, соответственно, затраты на производственный процесс будут минимальными. Как правило, для изготовления творога достаточно иметь:
- две кастрюли разного размера;
- шумовку;
- сито.
При этом самый простой рецепт и вовсе позволяет обойтись одной кастрюлей и марлей. Кастрюли желательно использовать алюминиевые, а не эмалированные, поскольку в эмалированных кастрюлях молоко при нагревании может слегка подгореть, что негативно отразится на вкусе конечного продукта.
Сырье
Основным сырьем для приготовления творога является молоко, но можно использовать также кефир. Некоторые рецепты потребуют дополнительных ингредиентов, например, сметану. При этом все используемые продукты должны быть натуральными – пастеризованное молоко, которое можно приобрести в магазине, использовать нельзя.
Помещение
Никаких особых требований к помещению для организации домашнего производства, разумеется, нет – вполне подойдет обычная кухня, главное, чтобы там было чисто, и чтобы пространства для работы было достаточно.
Расширяем производство
Если вы хотите изготавливать не только обычный, но и обезжиренный творог, вам потребуется сепаратор молока – специальный аппарат разделяющий молоко на обезжиренное молоко и сливки. Есть также сепараторы для работы с творогом. Они разделяют сквашенное молоко на творог и сыворотку. Но такое оборудование, как правило, используется лишь при промышленном производстве.
Технология и рецепты
Как мы писали выше, существует огромное множество рецептов приготовления творога, и каждый из них предполагает собственную технологию. Опишем пару самых простых из них – они позволяют изготовить продукт максимально быстро.
Рецепт №1
Свежее молоко нужно налить в небольшую кастрюлю, и поставить ее в теплое место – можно просто оставить на столе. Кастрюлю нужно продержать в тепле по меньшей мере 30 часов, не прикасаясь к молоку в течение всего этого срока – это ухудшит качество творожного сгустка.
По прошествии указанного времени молоко превратится в простоквашу и сывороточную жидкость. Теперь кастрюлю нужно поставить на плиту на очень маленький огонь. Простоквашу необходимо нагреть, но до кипения ее доводить не следует. Чтобы лучше контролировать температуру, можно воспользоваться водяной баней – поставить кастрюлю со сквашенным молоком в другую кастрюлю большего размера с водой, причем вода должна доходить не более чем до середины кастрюли с простоквашей.
Если сквашенное молоко будет перегрето, творог может получиться чрезмерно жестким , из-за чего он будет крошиться, а если нагреть простоквашу недостаточно, творог наверняка получится кислым, поскольку сыворотка будет отделяться недостаточно хорошо.
Во время нагревания молочную массу нельзя помешивать ложкой – это нарушит процесс отделения сыворотки. В ходе подогревания, нужно периодически проверять температуру, просто прикасаясь к кастрюле, чтобы не допускать перегрева. Греть нужно до тех пор, пока не появятся характерные творожные сгустки и прозрачная сыворотка, то есть около получаса. После этого кастрюлю нужно снять с огня и оставить остывать – до полного остывания пройдет около шести-восьми часов.
Затем нужно выложить творог шумовкой на сито, либо слить содержимое кастрюли в банку через марлю, после чего следует оставить творог на некоторое время, чтобы он стек. Если творог был переложен в марлю, ее нужно подвесить над раковиной или ванной, если в сито – его необходимо установить над любой емкостью, чтобы жидкости было куда стекать. До полной готовности творог должен стекать примерно час-полтора: если оставить его на более продолжительный срок, продукт может стать чрезмерно сухим.
Рецепт №2
Эта технология позволяет получить готовый творог еще быстрее.
Молоко нужно налить в банку, положить туда же несколько столовых ложек сметаны или кефира (примерно 50 грамм на один литр молока), и оставить в теплом месте для сквашивания. Добавление кисломолочных продуктов придаст творогу особый вкус, а кроме того, значительно ускорит этот процесс – в зависимости от температуры сквашивание может занять от 12-ти часов до суток. Во время сквашивания помешивать молоко не следует.
Когда молочная смесь превратится в простоквашу, нужно будет взять чистую кастрюлю, поставить в нее банку и налить такое количество воды, чтобы она была примерно на одном уровне с простоквашей. После чего банку нужно вынуть, а кастрюлю поставить на огонь. Доведя воду до кипения, необходимо выключить огонь и поставить в кастрюлю с горячей водой банку со сквашенным молоком. Банку следует накрыть крышкой и оставить примерно на полчаса.
По прошествии указанного времени банку нужно достать из воды и дать постоять еще 40-45 минут. После этого содержимое банки нужно вылить на марлю и подвесить получившийся творожный сгусток над ванной или раковиной на два часа.
Рентабельность
Исходя из того, что для изготовления одного килограмма творога нужно около трех литров молока, небольшое подсобное хозяйство с двумя коровами, дающими до десяти литров молока в день, может производить в среднем по шесть килограмм творога ежедневно. Средняя стоимость одного килограмма среднежирного домашнего творога на рынке – 250 рублей. Маложирный творог стоит порядка 300 рублей за килограмм. Чистая прибыль в месяц, таким образом, составит около 45-50 тысяч рублей. Дополнительную прибыль можно получить, продавая побочные продукты производства – сыворотку и, если при обработке молока использовался сепаратор, сливки.
Никаких особых сложностей в производстве творога в домашних условиях нет, а прибыль оно может приносить значительную, отнимая при этом совсем немного времени. Это идеальный вариант для получения дополнительного дохода с личного подсобного хозяйства.
Характеристика продукции, сырья и полуфабрикатов . Творог - белковый кисло-молочный продукт, изготовляемый сквашиванием культурами молочно-кислых бактерий с применением или без применения молокосвертывающего фермента и хлорида кальция пастеризованного нормализованного цельного или обезжиренного молока (допускается смешивание с пахтой) с последующим удалением из сгустка части сыворотки и отпрессовыванием белковой массы.
Творог имеет чистые кисло-молочные вкус и запах; для первого сорта допускается слабо выраженный привкус кормов, тары, легкой горечи. Консистенция нежная, однородная; для жирного творога первого сорта допускается несколько рыхлая и мажущаяся, для нежирного - рассыпчатая, с незначительным выделением сыворотки. Цвет белый, слегка желтоватый, с кремовым оттенком, равномерный по всей массе; для жирного творога первого сорта допускается некоторая неравномерность цвета.
Значительное содержание в твороге жира, и особенно полноценных белков, обусловливает его высокую пищевую и биологическую ценность. В твороге содержится значительное количество минеральных веществ (кальция, фосфора, железа, магния и др.), необходимых для нормальной жизнедеятельности сердца, центральной нервной системы, мозга, для костеобразования и обмена веществ в организме.
В зависимости от массовой доли жира творог подразделяют на три вида: жирный, полужирный и нежирный.
В качестве сырья используют доброкачественное свежее молоко цельное и обезжиренное кислотностью не выше 20 °Т. По жиру молоко нормализуют с учетом содержания в нем белка (по белковому титру), что дает более точные результаты.
К творожным изделиям относятся различные творожные массы и сырки, торты, кремы и т. п.
Особенности производства и потребления готового продукта. Существуют два способа производства творога - традиционный (обычный) и раздельный. Раздельный способ производства творога позволяет ускорить процесс отделения сыворотки и значительно снизить при этом потери. Сущность раздельного способа заключается в том, что молоко, предназначенное для выработки творога, предварительно сепарируют. Из полученного обезжиренного молока вырабатывают нежирный творог, к которому затем добавляют необходимое количество сливок, повышающих жирность творога до 9 или 18 %.
По методу образования сгустка различают два способа производства творога: кислотный и сычужно-кислотный. Первый основывается только на кислотной коагуляции белков путем сквашивания молока молочно-кислыми бактериями с последующим нагреванием сгустка для удаления излишней сыворотки. Таким способом изготовляется творог нежирный и пониженной жирности, так как при нагревании сгустка происходят значительные потери жира в сыворотку. Кроме того, этот способ обеспечивает выработку нежирного творога более нежной консистенции. Пространственная структура сгустков кислотной коагуляции белков менее прочная, формируется слабыми связями между мелкими частицами казеина и хуже выделяет сыворотку. Поэтому для интенсификации отделения сыворотки требуется подогрев сгустка.
При сычужно-кислотном способе свертывания молока сгусток формируется комбинированным воздействием сычужного фермента и молочной кислоты. Под действием сычужного фермента казеин на первой стадии переходит в параказеин, на второй - из параказеина образуется сгусток. Казеин при переходе в параказеин смещает изоэлектрическую точку с рН 4,6 до 5,2. Поэтому образование сгустка под действием сычужного фермента происходит быстрее, при более низкой кислотности, чем при осаждении белков молочной кислотой, полученный сгусток имеет меньшую кислотность, на 2.. .4 ч ускоряется технологический процесс. При сычужно-кислотной коагуляции кальциевые мостики, образующиеся между крупными частицами, обеспечивают высокую прочность сгустка. Такие сгустки лучше отделяют сыворотку, чем кислотные, так как в них быстрее происходит уплотнение пространственной структуры белка. Поэтому подогрев сгустка для интенсификации отделения сыворотки не требуется.
Сычужно-кислотным способом изготовляют жирный и полужирный творог, при котором уменьшается отход жира в сыворотку. При кислотном свертывании кальциевые соли отходят в сыворотку, а при сычужно-кислотном сохраняются в сгустке. Это необходимо учитывать при производстве творога для детей, которым необходим кальций для костеобразования.
Стадии технологического процесса. Производство творога традиционным способом включает в себя следующие стадии:
Приемка молока;
Нормализация молока до требуемого состава;
Очистка и пастеризация молока;
Охлаждение молока до температуры заквашивания;
Внесение закваски и сычужного фермента в молоко;
Сквашивание молока;
Разрезка сгустка;
Отделение сыворотки;
Охлаждение творога;
Фасование;
Упаковывание в тару и хранение готовой продукции.
Характеристика комплексов оборудования. Технологический процесс производства творога традиционным способом выполняется при помощи комплексов оборудования для приема, охлаждения, переработки, хранения и транспортирования сырья.
Для хранения принимаемого молока используют металлические емкости (танки). Молоко и продукты его переработки перекачиваются насосами. Приемку сырья осуществляют при помощи весов (молокосчетчиков), сепараторов-молокоочистителей, пластинчатых охладителей, пастеризаторов, фильтров и вспомогательного оборудования.
Ведущий комплекс линии состоит из творогоизготовителей с прессующими ваннами, ванн для творожного сгустка, установок для прессования и охлаждения творога.
Завершающий комплекс оборудования линии обеспечивает фасование, упаковывание, хранение и транспортирование готового продукта. Он содержит фасовочно-упаковочные машины и оборудование экспедиций и складов готовой продукции.
Машинно-аппаратурная схема линии производства творога традиционным способом приведена на рис.
Рис. Машинно-аппаратурная схема линии производства творога традиционным способом
Молоко из емкости 1 подается сначала в балансировочный бачок 2, а затем насосом 3 в секцию рекуперации пастеризационно-охладительной установки 5, где оно подогревается до температуры 35.. .40 °С и направляется на сепаратор-очиститель 4.
Нормализованное и очищенное молоко направляют на пастеризацию при 78.. .80 °С с выдержкой 20. ..30 с. Температура пастеризации влияет на физико-химические свойства сгустка, что, в свою очередь, отражается на качестве и выходе готового продукта. Так, при низких температурах пастеризации сгусток получается недостаточно плотным, так как сывороточные белки практически полностью отходят в сыворотку, и выход творога снижается. С повышением температуры пастеризации увеличивается денатурация сывороточных белков, которые участвуют в образовании сгустка, повышая его прочность и усиливая влагоудерживающую способность. Это снижает интенсивность отделения сыворотки и увеличивает выход продукта. Путем регулирования режимов пастеризации и обработки сгустка, подбором штаммов заквасок можно получать сгустки с нужными реологическими и влагоудерживающими свойствами.
Пастеризованное молоко охлаждают в секции рекуперации пластинчатой пастеризационно-охладительной установки 5 до температуры сквашивания (в теплое время года до 28...30 °С, в холодное - до 30...32 °С) и направляют в специальные ванны 6 на заквашивание. Закваску для производства творога изготовляют на чистых культурах мезофильных молочно-кислых стрептококков и вносят в молоко в количестве от 1 до 5 %. Продолжительность сквашивания после внесения закваски составляет 6...8 ч.
При ускоренном способе сквашивания в молоко вносят 2,5 % закваски, приготовленной в заквасочнике 10 на культурах мезофильного стрептококка, и 2,5 % термофильного молочно-кислого стрептококка. Температура сквашивания при ускоренном способе повышается в теплое время года до 35 °С, в холодное - до 38 °С. Продолжительность сквашивания молока при ускоренном способе 4,0...4,5 ч, т.е. сокращается на 2,0...3,5 ч, при этом выделение сыворотки из сгустка происходит более интенсивно.
Для улучшения качества творога желательно применять беспересадочный способ приготовления закваски на стерилизованном молоке, что позволяет снизить дозу внесения закваски до 0,8... 1,0 % при гарантированной ее чистоте.
При сычужно-кислотном способе производства творога после внесения закваски добавляют 40 %-ный раствор хлорида кальция (из расчета 400 г безводной соли на 1 т молока), приготовленного на кипяченой и охлажденной до 40...45 °С воде. Хлорид кальция восстанавливает способность пастеризованного молока образовывать под действием сычужного фермента плотный, хорошо отделяющий сыворотку сгусток. Немедленно после этого в молоко в виде 1 % -ного раствора вносят сычужный фермент или пепсин из расчета 1 г на 1 т молока. Сычужный фермент растворяют в кипяченой и охлажденной до 35 °С воде. Раствор пепсина с целью повышения его активности готовят на кислой осветленной сыворотке за 5...8 ч до использования. Для ускорения оборачиваемости творожных ванн 6 молоко сквашивают до кислотности 32...35 °Т в резервуарах, а затем перекачивают в творожные ванны и вносят хлорид кальция и фермент.
Окончание сквашивания и готовность сгустка определяют по его кислотности (для жирного и полужирного творога должна быть 58...60 °Т, для нежирного - 66...70 °Т) и визуально - сгусток должен быть плотным, давать ровные гладкие края на изломе с выделением прозрачной зеленоватой сыворотки. Сквашивание при кислотном методе продолжается 6.. .8 ч, сычужно-кислотном - 4.. .6 ч, с использованием активной кислотообразующей закваски - 3...4 ч.
Чтобы ускорить выделение сыворотки, готовый сгусток разрезают специальными проволочными ножами на кубики с размером граней 2 см. При кислотном методе разрезанный сгусток подогревают до 36.. .38 °С для интенсификации выделения сыворотки и выдерживают 15...20 мин, после чего ее удаляют. При сычужно-кислотном - разрезанный сгусток без подогрева оставляют в покое на 40...60 мин для интенсивного выделения сыворотки.
Для дальнейшего отделения сыворотки сгусток подвергают самопрессованию и прессованию. Для этого его разливают в бязевые или лавсановые мешки по 7.. .9 кг (на 70 % вместимости мешка), их завязывают и помещают несколькими рядами в пресс-тележку 7. Под воздействием собственной массы из сгустка выделяется сыворотка. Самопрессование происходит в цехе при температуре не выше 16 °С и продолжается не менее 1 ч. Окончание самопрессования определяется визуально по поверхности сгустка, которая теряет блеск и становится матовой. Затем творог под давлением прессуют до готовности. В процессе прессования мешочки с творогом несколько раз встряхивают и перекладывают. Во избежание повышения кислотности прессование необходимо проводить в помещениях с температурой воздуха 3.. .6 °С, а по его окончании немедленно направлять творог на охлаждение до температуры не выше 8 °С с использованием охладителей различных конструкций; наиболее совершенным из них является двухцилиндровый охладитель 8.
Готовый продукт фасуют на машинах 9 в мелкую и крупную тару. Творог фасуют в картонные ящики с вкладышами из пергамента, полиэтиленовой пленки. В мелкую упаковку творог фасуют в виде брусков массой 0,25; 0,5 и 1 кг, завернутых в пергамент или целлофан, а также в картонные коробочки, пакеты, стаканы из различных полимерных материалов.
Творог хранят до реализации не более 36 ч при температуре камеры не выше 8 °С и влажности 80.. .85 %. Если срок хранения будет превышен из-за непрекращающихся ферментативных процессов, в твороге начинают развиваться пороки.
Творогоизготовители с прессующей ванной используют для выработки всех видов творога, при этом трудоемкий процесс прессования творога в мешочках исключается. Творогоизготовитель состоит из двух двустенных ванн вместимостью 2000 л с краном для спуска сыворотки и люком для выгрузки творога. Над ваннами закреплены прессующие ванны с перфорированными стенками, на которые натягивают фильтрующую ткань. Прессующая ванна при помощи гидравлического привода может подниматься вверх или опускаться вниз почти до дна ванны для сквашивания.
Готовый творог направляется на фасование и затем в холодильную камеру для доохлаждения.
С целью резервирования творога в весенний и летний периоды года его замораживают. Качество размороженного творога зависит от метода замораживания. Творог при медленном замораживании приобретает крупитчатую и рассыпчатую консистенцию вследствие замораживания влаги в виде крупных кристаллов льда. При быстром замораживании влага одновременно замерзает в виде мелких кристаллов во всей массе творога, которые не разрушают его структуру, и после размораживания восстанавливаются первоначальные, свойственные ему консистенция и структура. Наблюдается даже устранение после размораживания нежелательной крупитчатой консистенции вследствие разрушения крупинок творога мелкими кристаллами льда. Замораживают творог в фасованном виде - блоками по 7... 10 кг и брикетами по 0,5 кг при температуре от -25 до -30 °С в термоизолированных морозильных камерах непрерывного действия до температуры в центре блока-18 °С и-25 °С в течение 1,5... 3,0 ч. Замороженные блоки укладывают в картонные ящики и хранят при этих же температурах в течение соответственно 8 и 12 мес. Размораживание творога проводят при температуре не выше 20 °С в течение 12 ч.
Машинно-аппаратурная схема линии производства творога раздельным способом представлена на рис.

Рис. Машинно-аппаратурная схема линии производства творога раздельным способом с использованием сепаратора-творогоотделителя
Устройство и принцип действия линии. При этом способе производства молоко, предназначенное для выработки творога, из емкости 1 насосом 2 подается в уравнительный бачок 3, а из него - насосом 2 в секцию рекуперации пластинчатой пастеризационно-охладительной установки 4 для подогревания до 40...45 °С. Подогретое молоко поступает в сепаратор-сливкоотделитель 5, в котором разделяется на обезжиренное молоко и сливки с массовой долей жира не менее 50.. .55 %. Полученные сливки подают сначала в промежуточную емкость 6, а затем насосом 7 в пластинчатую пастеризационно-охладительную установку 8, где они пастеризуются при температуре 85.. .90 °С с выдержкой 15.. .20 с, охлаждаются до 2.. .4 °С и направляются в двустенную емкость 9 на временное хранение до смешения с творогом.
Обезжиренное молоко из сепаратора поступает в пластинчатую пастеризационно-охладительную установку 4, где сначала пастеризуется при температуре 78 °С с выдержкой 15...20 с, а затем охлаждается до 30...34 °С и направляется в резервуар 11 для сквашивания, снабженный специальной мешалкой. Закваска, приготовленная в заквасочнике 10, насосом 7 подается в резервуар 11 для заквашивания. Сюда же подаются хлорид кальция и фермент, смесь тщательно перемешивают и оставляют для сквашивания до кислотности сгустка 90... 116 °Т, а если используется ускоренный способ сквашивания молока, то 85.. .90 °Т. При сепарировании сгустка с меньшей кислотностью сопла сепаратора могут засориться.
Полученный сгусток тщательно перемешивается и насосом 12 подается в пластинчатый теплообменник 13, где вначале подогревается до 60...62 °С для лучшего отделения сыворотки, а затем охлаждается до 25...32 °С, благодаря чему он лучше разделяется на белковую часть и сыворотку. Из теплообменника 13 сгусток через сетчатый фильтр 14 под давлением подается в сепаратор-творогоизготовитель 15, где разделяется на сыворотку и творог.
При выработке жирного творога обезвоживание сепарированием проводят до массовой доли влаги в сгустке 75... 76 %, а при выработке полужирного творога-до массовой доли влаги 78...79 %. Полученный обезжиренный творог подают специальным насосом 16 сначала на охладитель 17 для охлаждения до 8 °С, растирают на вальцовке до получения гомогенной консистенции. Охлажденный творог направляют в месильную машину 19, куда дозирующим насосом 7 подаются пастеризованные охлажденные сливки из емкости 18 и все тщательно перемешивается. Готовый творог фасуют на машинах 20 и направляют в камеру для хранения.
ТЕХНОЛОГИЯ ТВОРОГА
Традиционный способ технологии производства творога
Технологический процесс производства творога традиционным способом включает следующие последовательно осуществляемые технологические операции: подготовку молока, получение сырья требуемого состава, пастеризацию, охлаждение до температуры заквашивания, заквашивание, сквашивание, дробление сгустка, отделение сыворотки, охлаждение творога, фасование.
Схема технологической линии производства творога традиционным способом представлена на рисунке 12.
Рис. 12. Схема технологической линии производства творога традиционным способом:
1 - емкость для молока; 2-балансировочный бачок; 3- насос; сепаратор-очиститель;
5 - пластинчатая пастеризационно-охладительная установка; 6-творожная ванна; 7- пресс-тележка; 8 - охладитель для творога; 9 - автомат для фасования творога; 10 - заквасочник
При выработке творога с различной массовой долей жира проводят нормализацию молока по жиру с учетом массовой доли белка в цельном молоке, а для производства нежирного творога используют обезжиренное молоко.
Сырье, предназначенное для производства творога, предварительно очищают.
Пастеризацию подготовленного сырья осуществляют при температуре 78…80 °С с выдержкой 20…30 с. Пастеризованное молоко охлаждают до температуры сквашивания, которая в теплый период года достигает 28…30 °С, а в холодный - 30…32 °С, и направляют на заквашивание.
Если используют кислотно-сычужную коагуляцию белков молока, то при заквашивании в молоко вносят закваску?, хлорид кальция и сычужный фермент, если кислотную коагуляцию - то только закваску.
Для заквашивания применяют закваску на чистых культурах мезофильных лактококков. Продолжительность сквашивания составляет 6…8 ч. При ускоренном способе сквашивания в молоко вносят закваску, приготовленную на культурах мезофильных лактококков и на культурах термофильного молочнокислого стрептококка. Температура сквашивания при ускоренном способе
35…38 °С, продолжительность сквашивания 4…4,5 ч.
Хлорид кальция, необходимый для восстановления солевого равновесия, нарушенного при пастеризации молока, вносят в виде 40%-ного раствора из расчета 400 г безводной соли на 1 т молока. После этого в молоко вносят сычужный фермент, или пепсин, или ферментный препарат из расчета 1 г фермента на 1 т молока. После внесения закваски, хлорида кальция и сычужного фермента молоко перемешивают и оставляют в покое до окончания сквашивания.
Об окончании сквашивания судят по кислотности сгустка. Для творога с массовой долей жира 18 и 9 % кислотность должна составлять 58…60 °Т, для нежирного 66…70 °Т.
Для ускорения выделения сыворотки готовый сгусток разрезают специальными проволочными ножами на кубики размером по ребру около 2 см. Разрезанный сгусток оставляют в покое на 40…60 мин для выделения сыворотки и нарастания кислотности.
В производстве творога нежирного используют кислотную коагуляцию белков молока. Полученный при этом сгусток имеет меньшую прочность, чем сгусток, полученный при сычужно-кислотной коагуляции, и хуже обезвоживается. Для усиления и ускорения выделения сыворотки нагревают полученный сгусток до
36…38 °С с выдержкой 15…20 мин.
Выделившуюся сыворотку удаляют, а сгусток разливают в бязевые или лавсановые мешки по 1…9 кг и направляют для дальнейшего отделения сыворотки на самопрессование и прессование.
После прессования творог немедленно охлаждают до 3…8 °С, в результате чего прекращается молочнокислое брожение с нарастанием излишней кислотности. Охлажденный творог фасуют в виде брикетов в пергамент, коробочки и стаканчики из полимерных материалов и др.
Производство творога традиционным способом с использованием для прессования мешков - трудоемкий и продолжительный процесс. В настоящее время с целью снижения трудозатрат и потерь сырья, повышения производительности и культуры производства отдельные операции механизированы и созданы механизированные и автоматизированные линии.
Творогоизготовитель ТИ-4000 имеет перфорированную пресс-ванну, что позволяет механизировать операции отделения сыворотки и прессования сгустка.
Технологический процесс производства творога 9%-ной и 18%-ной жирности, крестьянского и нежирного с помощью кислотно-сычужной и кислотной коагуляции белков на творогоиз-готовителях ТИ-4000 от приемки до прессования сгустка состоит из тех же операций, что и при традиционном способе. Прессование сгустка в творогоизготовителе после удаления части выделившейся сыворотки осуществляется с помощью перфорированной пресс-ванны, на которую натянуто фильтрующее полотно. Пресс-ванна с помощью гидропривода опускается до соприкосновения с зеркалом сгустка со скоростью 200 мм/мин. При прессовании сгустка она опускается со скоростью 2…4 мм/мин. Сыворотка периодически откачивается из пресс-ванны самовсасывающим или вакуумным насосом. Творог прессуют до достижения стандартной массовой доли влаги. Продолжительность прессования от 4 до 6ч в зависимости от вида творога. После прессования пресс-ванну поднимают, а готовый творог выгружают в тележки и охлаждают.
Технологическая линия с перфорированными ваннами-вставками позволяет механизировать процессы самопрессования и охлаждения творога. Ванну-вставку помещают непосредственно в творожную ванну перед началом сквашивания. После образования сгустка его подогревают до температуры 50…55 °С и выдерживают в течение 25…30 мин. После окончания нагревания сгусток охлаждают и удаляют часть выделившейся сыворотки. Для более свободного стекания сыворотки ванну-вставку с помощью тельфер-ного устройства поднимают над ванной и оставляют в таком положении на 20…40 мин.
После самопрессования творог охлаждают пастеризованной и охлажденной до 5 °С сывороткой. Ванну-вставку погружают в сыворотку и выдерживают в ней в течение
20…30 мин. Творог охлаждают до температуры 13±5°С, ванну-сетку поднимают, и творог самопрессуется в течение 20…30 мин, затем его подают на фасование.
Механизированная линия Я9-ОПТ служит для выработки полужирного, крестьянского и нежирного творога.
Технологический процесс производства творога на линии Я9-ОПТ (рис. 13) состоит из следующих операций: приемки молока, очистки, нормализации, гомогенизации, пастеризации, охлаждения до температуры сквашивания, сквашивания (кислотная коагуляция белков), обработки сгустка, охлаждения и фасования творога.
Заквашивание и сквашивание молока проводят в емкостях до образования сгустка с pH 4,5…4,7. Продолжительность сквашивания не должна превышать 10 ч.
Готовый сгусток перемешивают в течение 2…5 мин и винтовым насосом подают в прямоточный подогреватель, в котором нагревают до температуры 48…54 °С при выработке полужирного творога, до 46…52 °С - крестьянского творога и до 42…50 °С - нежирного творога. Нагревание проводят в течение 2…2,5 мин горячей (70…90°С) водой, циркулирующей в рубашке подогревателя. Из подогревателя сгусток поступает в выдерживатель, где находится в течение 1… 1,5 мин, затем направляется в охладитель. В охладителе сгусток охлаждается до 30…40 °С при производстве полужирного творога и крестьянского, до 25…35 °С - при выработке нежирного творога.
Для обезвоживания творожного сгустка используют вращающийся двухцилиндровый обезвоживатель, обтянутый фильтрующей тканью из лавсана. Содержание влаги в твороге регулируют путем изменения угла наклона барабана обезвоживателя или температуры подогревания и охлаждения.
Полученный творог охлаждают до 8… 12 °С в двухцилиндровом или шнековом охладителе и подают на фасование.
Рис. 13. Схема механизированной линии Я9-ОПТ по производству творога:
1- емкость для сырой нормализованной смеси; 2- насос для молока; 3- пастеризационно-охладительная установка; 4- сепаратор-молокоочиститель; 5 - гомогенизатор; 6- емкость для сквашивания молока; 7- винтовой насос для подачи сгустка; 8- аппарат для тепловой обработки сгустка (а - подогреватель; б- выдерживатель; в - охладитель); 9-обезвоживатель сгустка; 10- центробежный насос для сыворотки; 11 - охладитель творога; 12- подъемник для тележек; 13 - фасовочный автомат
Технология мягкого диетического творога
Технологический процесс производства мягкого диетического творога состоит из следующих операций:
– приемка и подготовка сырья и основных материалов;
– подогрев и сепарирование молока;
– пастеризация и охлаждение сливок;
– пастеризация и охлаждение обезжиренного молока;
– заквашивание и сквашивание обезжиренного молока;
– нагревание и охлаждение творожного сгустка;
– сепарирование творожного сгустка;
– охлаждение обезжиренного творога;
– смешивание обезжиренного творога со сливками и плодово-ягодными наполнителями;
– доохлаждение упакованного продукта.
Приемка и подготовка сырья и основных материалов. Молоко и другое сырье принимают по массе и качеству.
Для приготовления сахарного сиропа сахар-песок, предварительно просеянный на специальной машине или через сито, массой, предусмотренное рецептурой, вносят в емкость (ванна ВДП, сироповарочный котел и др.) и растворяют в питьевой воде, взятой согласно рецептуре. Раствор нагревают до температуры (93±2) °С, перемешивают мешалкой до полного осветления сиропа, а затем охлаждают до температуры (20±2) °С. Готовый сироп должен иметь массовую долю сахарозы 66, % и плотность 1322,4 кг/м3.
Плодово-ягодные наполнители, поступившие на предприятие в герметичных модулях, дополнительной тепловой обработки не требуют.
Плодово-ягодные наполнители, поступившие на предприятие в таре, извлекают из нее и помещают в подготовительную емкость (ванну ВДП). В случае обнаружения молочнокислых бактерий, плесеней или дрожжей в количестве, превышающем нормативы, наполнители пастеризуют при температуре (80±2) ºС с выдержкой 5–10 мин, перемешивают и охлаждают до температуры 20–25 °С.
В случае использования плодово-ягодных наполнителей, поступающих на молочный завод в мелкой упаковке, необходимо предусмотреть обязательную пастеризацию в накопительной емкости при температуре (80±2) ºС с выдержкой 5–10 мин, перемешиванием и охлаждением до температуры 20–25 °С.
Мороженые плоды и ягоды перебирают на разборном столе, промывают теплой водой и загружают в котел, где они обрабатываются паром в течение 3–5 мин, а затем подаются в протирочную машину.
Полученную однородную массу без плодоножек и косточек пастеризуют при температуре (80±2) ºС с выдержкой 5–10 мин, перемешивают и охлаждают до температуры 20–25 °С.
Подогрев и сепарирование молока . Отобранное по качеству молоко нагревают до температуры (37±3) °С и направляют в сепаратор–сливкоотделитель для получения сливок с массовой долей жира 50–55 %. При необходимости сливки нормализуют до массовой доли в них жира 50–55% путем добавления к ним соответствующей массы цельного или обезжиренного молока, либо более жирных сливок.
Пастеризация и охлаждение сливок . Полученные сливки поступают в промежуточную емкость, откуда их насосом подают на пастеризиционно-охладительную установку, где их пастеризуют при температуре (88±2) °С с выдержкой 15–20 с и охлаждают до температуры (38±8) °С, после чего сливки подают в секцию охлаждения специального теплообменника, где их охлаждают и направляют в двустенные емкости для доохлаждения и хранения до использования. Сливки доохлаждают до температуры (8±2) °С и хранят не более 5 ч или до температуры (3±2) °С и хранят не более 18 ч.
Допускается производить пастеризацию, охлаждение и хранение сливок при указанных режимах в двустенных резервуарах.
Пастеризация и охлаждение обезжиренного молока . Обезжиренное молоко с массовой долей жира не более 0,05 % пастеризуют на пастеризационно-охладительных установках при температуре (78±2)°С с выдержкой 15–20 с. Пастеризованное обезжиренное молоко охлаждают до температуры заквашивания и направляют в вертикальные резервуары вместимостью 5–10 м3 для заквашивания и сквашивания. Если молоко непосредственно после пастеризации не поступает на переработку, его охлаждают до температуры (4±2) °С и хранят в резервуарах не более 5 часов. При более длительном хранении перед заквашиванием обезжиренное молоко подвергают повторной пастеризации.
Заквашивание исквашивание обезжиренного молока . Закваску, приготовленную на чистых культурах лактококков, подают в резервуары для сквашивания до заполнения, в процессе и непосредственно после их заполнения обезжиренным молоком или в потоке. Закваска вводится массой от 30 до 50 кг на 1000 кг заквашиваемого молока при его температуре (30±2) °C в холодное время года и (28±2) °С – в теплое.
После заполнения резервуара молоком и внесения закваски добавляют хлористый кальций из расчета 400 г безводного хлористого кальция на 1000 кг заквашенного молока. Хлористый кальций вносят в виде водного раствора с массовой долей хлористого кальция 30–40 %, которую уточняют по плотности.
После внесения хлористого кальция в молоко вводят сычужный порошок, или пепсин пищевой говяжий, или пепсин свиной, или ферментный препарат ВНИИМС из расчета 1,01,2 г активностью 100000 ед на 1000 кг молока в виде водного раствора с массовой долей фермента не более I %.
Закваску, растворы хлористого кальция и фермента вносят при непрерывном перемешивании молока механической мешалкой. Перемешивание молока после заквашивания продолжают в течение 1015 мин., затем оставляют молоко в покое до образования сгустка требуемой кислотности.
Окончание сквашивания молока определяют по активной кислотности сгустка, которая должна быть в пределах рН 4,44,5 или по титруемой кислотности сыворотки 6070 °Тили сгустка 90110 °Т. Продолжительность сквашивания составляет 810 ч.
Нагревание и охлаждение творожного сгустка . Готовый сгусток тщательно перемешивают в течение 510 мин и насосом подают в пластинчатую пастеризационно-охладительную установку для сгустка, где его нагревают до температуры (60±2) °Си охлаждают до температуры (28±2) °С. После охлаждения сгусток направляют через сетчатый фильтр в сепаратор для получения обезжиренного творога.
Рис.26 ПОУ для сгустка
На линиях, где пастеризационно-охладительные установки для сгустка не предусмотрены, допускается производить нагрев творожного сгустка до температуры (36± 2) °С в течение 2030 мин в резервуаре путем подачи в межстенное пространство горячей воды и производить сепарирование сгустка при указанной температуре или производить сепарирование сгустка без предварительного нагревания.
Сепарирование творожного сгустка . При производстве всех видов мягкого диетического творога обезжиренный творог должен иметь массовую долю влаги не более 80 %. Для получения обезжиренного творога с указанной влажностью, в барабане творожного сепаратора устанавливают сопла с диаметром отверстий в пределах от 0,4 до 0,8 мм.
Рис.27 Сепараторы для обезвоживания белкового сгустка
Основной рабочий орган сепаратора - барабан. Обезвоживание сгустка в нем осуществляется следующим образом.
Способ производства мягкого творога
Перед сепарированием сгусток проходит через фильтр, представляющий собой два поочередно работающих вертикальных цилиндра с сеткой внутри, соединенных трубопроводом, в котором установлен трехходовой кран.
Сгусток подается под давлением, которое контролируется манометром, установленным на входном трубопроводе, далее по питающей трубке он поступает в тарелкодержатель, где, распределяясь по внутренним каналам между ребрами тарелкодержателя, приобретает угловую скорость и поступает через отверстия в тарелкодержателе в вертикальные каналы, образуемые отверстиями в тарелках.
Распределяясь тонкими слоями между тарелками, сгусток под действием центробежной силы разделяется на творог и сыворотку. Творог как более тяжелая фракция направляется к периферии барабана, откуда непрерывно выводится через сопла в приемник, а сыворотка - более легкая фракция - оттесняется к оси вращения барабана, поднимается по наружным каналам в тарелкодержателе и выводится в приемник.
Во избежание интенсивного отделения сыворотки от сгустка в течение всего времени работы сепаратора периодически включают мешалку в резервуаре.
В процессе сепарирования сгустка необходимо контролировать отделяемую сыворотку на наличие в ней частичек белка.
В бутылку емкостью 0,5 л каждые 20–30 мин работы сепаратора отбирают сыворотку и оставляют в покое на 2–3 мин для удаления пузырьков воздуха. При правильном режиме работы сепаратора сыворотка должна быть прозрачной. При наличии частичек белка необходимо снизить производительность сепаратора для предотвращения излишних потерь белка с сывороткой.
При получении творога с массовой долей влаги более 80 %необходимо повысить производительность сепаратора. Если при этом массовая доля влаги не уменьшается, то необходимо сепаратор остановить, разобрать, промыть и заново начать сепарирование сгустка.
Охлаждение обезжиренного творога. По выходе из сепаратора обезжиренный творог поступает в бункер насоса для подачи его на трубчатый или пластинчатый охладители творога, где он охлаждается до температуры (14±2) °С. При выработке нежирного творога, творог поступает из охладителя на упаковывание (в стаканчики, коробочки, батончики) и доохлаждение до температуры (4±2) °С.
Рис. 28 Теплообменник трубчатый для охлаждения творога в потоке
Смешивание обезжиренного творога со сливками и плодово-ягодными наполнителями . Обезжиренный творог из охладителя направляют в смеситель. Одновременно с творогом в смеситель подают и сливки. При этом перемешивание творога и сливок происходит в потоке.
При выработке творога на линиях, имеющих специальный смеситель–дозатор, обезжиренный охлажденный творог попадает в бункер дозатора творога, а сливки - в дозатор сливок.
В случае выработки плодово-ягодного творога сахарный сироп и плодово-ягодные наполнители предварительно смешивают в отдельном резервуаре со сливками 5055 % жирности в количествах, предусмотренных рецептурами.
Допускается смешивание в отдельном резервуаре творога со сливками или без сливок с плодово-ягодными наполнителями и сахарным сиропом. Творог с компонентами (сливками, плодово-ягодными наполнителями, сахарным сиропом) тщательно перемешивают.
В случае выработки плодово-ягодного обезжиренного мягкого диетического творога к обезжиренному творогу добавляют только плодово-ягодные наполнители и сахарный сироп, согласно рецептурам.
Упакованный мягкий диетический творог направляют в холодильную камеру для доохлаждения до температуры (4±2) °С, продолжительность которого не должна быть более 7 ч.
При ускоренном способе производства мягкого диетического творога обезжиренное молоко пастеризуют при температуре (85±2) °С без выдержки или с выдержкой до 10 мин или (90±2) °С без выдержки или с выдержкой до 3–х мин. Обезжиренное молоко охлаждают до температуры заквашивания (36±2)°С. В данном случае применяют закваски, приготовленные на чистых культурах лактококков и термофильных молочнокислых стрептококков. Закваски вносят в молоко при температуре (36±2) °С из расчета 25 кг закваски, приготовленной на чистых культурах лактококков, и 25 кг закваски, приготовленной на чистых культурах термофильных стрептококков, на 1000 кг заквашиваемого молока. Добавляют растворы хлористого кальция и ферментных препаратов.
Окончание сквашивания молока определяют по активной кислотности сгустка, которая должна быть в пределах, рН 4,64,7 или по титруемой кислотности сгустка 8590 °Т. Продолжительность сквашивания составляет 57ч.
Рис. 29 Схема технологического процесса производства творога мягкого
диетического (на линии марки Б60ТР)
I пластинчатый теплообменник для обезжиренного молока и сливок: 2 емкость для сливок, сиропов и их смесей; 3 насос для сливок, сиропов и их смесей; 4 бак расходный: 5 резервуар для сквашивания молока; 6 насос для сгустка; 7 пастеризатор сгустка; 8 фильтр творожного сгустка; 9 ротаметр сгустка; 10 сепаратор для сгустка; 11 бункер для творога со шнекомпитателем; 12 насос для творога: 13 охладитель творога обезжиренного; 14 смеситель с дозаторами жидких компонентов; 15 емкость для творога; 16 автомат для фасовки и упаковки творога.
В чем разница между творогом и творожным продуктом - что лучше выбрать?
УПАКОВКА И ХРАНЕНИЕ ТВОРОГА И ТВОРОЖНЫХ ИЗДЕЛИЙ
Творог фасуют на автоматах в мелкую тару - брикеты из пергамента или кашированной фольги, стаканчики из полистирола, пакеты из полиэтиленовой пленки с последующей укладкой в картонные, деревянные или полимерные ящики с вкладышами из пергамента, полиэтиленовой пленки массой не более 20 кг.
Пергаментные этикетки для мелких порций творога, крышки полистироловых коробочек, стаканов и тубы из полимерных пленок для мягко диетического творога имеют маркировку. На ней указывают наименование или номер предприятия-изготовителя и его подчиненность, наименование продукта, массовую долю жира, массу нетто, дату конечного срока реализации, розничную цежу и стандарт.
Для удобства транспортирования творог в мелкой упаковке укладывают в ящики вместимостью не более 20 кг. При фасовании творога в крупную тару используют тщательно вымытые подготовленные алюминиевые бидоны вместимостью не более 10 кг и металлические ящики на 35 кг. Ящики маркируют при помощи этикеток или бирок.
Творог хранят в холодильных камерах при температуре не выше 4 + 2 °С и влажности воздуха 80…85 %/ Его размещают по партиям выработки. в камерах поддерживают строгий санитарный режим и не допускают значительных колебаний температуры. Гарантийный срок хранения творога составляет 36 ч с момента окончания технологического процесса, в том числе на предприятии не более 18 ч; творог пониженной жирности со стабилизаторами хранят до 7 сут, творог термизированный — до 14 сут. При температуре 0 ± 1 °с творог хранят не более 10 сут.
УПАКОВКА И ХРАНЕНИЕ МАСЛА
На заводе масло хранят в специальных охлаждаемых сухих, чистых помещениях с хорошей вентиляцией при относительной влажности воздуха не выше 80 % во избежание плесневения продукта. Тару с маслом размещают штабелями и прокладывают рейками таким образом, чтобы способствовать быстрому охлаждению продукта.
На предприятиях молочной промышленности сливочное масло хранят в монолитах и фасованным.
Производство творога традиционным способом
В монолитах при массовой доле влаги в масле 16, 20 и 25 % его хранят при температуре от 0 до 5 °с не более 3 сут, от 0 до -12 °С - не более 10 сут, а от -12 до -18 °С - не более 15 сут. При массовой доле влаги в масле более 25 % его хранят при температуре от 0 до 5 °С не более 2 сут, от 0 до -2 °С - не более 5 сути от -12 до -18 °С - не более 6 сут.
Фасованное масло с массовой долей влаги 16, 20 и 25 % хранят при температуре от -3 до -18 °С в течение 3 сут, а с массовой долей влаги более 25 % - при температуре от -3 до -18 °С в течение 3 сут. Можно храните фасованное масло всех видов при температуре от 2 до -2 °С не более 2 сут. Топленое масло хранят при температуре от 4 до -6 °С.
Сливочное масло в потребительской таре должно храниться при температуре не выше -3 °С и относительной влажности воздуха не более 80 %. Срок его хранения со дня фасования в пергаменте - не более 10 сут; в алюминиевой кашированной фольге - 20; в стаканчиках и коробочках из полимерных материалов - 15; в металлических банках (кроме Вологодского масла) - 90 сут.
Срок хранения Вологодского масла в транспортной таре и срок его реализации в фанерно-штампованных бочонках и в металлических банках -- не более 30 сут с момента выработки.
Топленое масло в потребительской таре хранят при температуре от 0 до -3 °С и влажности 80 %; в стеклянных байках - не более 3 мес.
Не допускаются колебания температуры в камерах хранения масла, так как это приводит к конденсации влаги на монолитах масла, а затем к росту и развитию плесеней.
Хранят подсырное масло на заводах до 20 сут, а на маслобазах и в цехах переработки - 30…40 сут при температуре не выше 5 °С и относительной влажности менее 80 %; при температурах от -10 до -15 °С - до 2 мес.
УПАКОВКА И ХРАНЕНИЕ СЫРОВ
В зависимости от формы, размера и веса сыры упаковывают в деревянные ящики, барабаны и окоренки, а рассольные – в бочки.
В каждую единицу упаковки помещают сыры одного наименования, сорта одинаковой формы и одного возраста.
Тара должна быть чистой, прочной, влажность древесины не более 20%.
Ящики разделены внутри перегородками для предохранения сыров от повреждения. Многие сыры перед упаковкой завертывают в пергамент, восковку, целлофан и другие пленки. Мягкие сычужные сыры завертывают в пергамент и алюминиевую фольгу, на которую наклеивают этикетку, после чего упаковывают.
Плавленые сыры завертывают в алюминиевую лакированную фольгу. Копченый сыр выпускают в оболочке из различных пленок на торцевую сторону внешней тары наносят маркировку, где указывают название сыра, номер завода, вес нетто, тар и брутто, количество сыров, фамилию мастера.
Поступившие на холодильник сыры должны иметь сопроводительные документ. Затем сыры рассортировывают по видам и сортам, проверяют соответствие сопроводительных документов и маркировки отправителя, исправность и сохранность упаковки.
Для хранения сыров на складах выделяют отдельные помещения во избежание передачи другим продуктам сырного запаха. Рассольные сыры располагают отдельно от других, учитывая возможность утечки рассола.
Для длительного хранения твердых сычужных сыров наилучшие условия - температура от 0 до -4 °С и относительная влажность воздуха 85…90 %. Такой режим способствует замедлению биохимических процессов в сыре и устраняет возможность его перезревания. Однако хранение сыра при температурах ниже 0 °С иногда оказывает отрицательное влияние на его качество. Хранение при таких температурах допустимо только для полнозрелого сыра, имеющего корку без дефектов, хорошо выраженной вкус и нормальную.
Хорошо созревшие сыры, заложенные, на длительное хранение, можно держать при температуре от -1 °С до -5 °С и относительной влажности воздуха 85…90 %.
На предприятиях мягкие сычужные сыры хранят при 10 °С в течение 10 сут. В торговрй сети при температуре от 0 до -5 °С - не более 10 сут и от минус 5 до 0 °С – не более 1 мес.
Рассольные сыры хранят в бочках с рассолом концентрацией 16…18% при температуре не выше 8 °С: брынзу – 75, сулугуни – 25, столовый – 15 сут.
Производство творога
Рынок молочной продукции широко развит, поэтому производителю, который хочет занять достойное место на нем, нужно особое внимание уделять качеству производимого продукта. Для производства творога в пищевой промышленности применяются так называемые творожные ванны относящиеся к оборудованию для пищевого производства. Их наполняют молоком, а затем вносят в него закваски и выдерживают заданное время. В результате продукт заквашивается, творожная масса сначала отделяется от сывороточной части, затем прессуется и нормализуется по уровню влажности.
Как работают творожные ванны
По сути, творожные ванны - это специальные резервуары (оборудование для производства творога). Они имеют форму полуцилиндра, устанавливаются на опоры, оснащаются рубашками теплообмена, трубами с отверстиями, инжектором. Установки высокого качества надежны в работе и могут функционировать без проблем в течение десятка лет, если соблюдать правила их эксплуатации. На рынке представлено типовое оборудование, есть возможность заказа аппаратуры по индивидуальным эскизам. Главное - соблюдение производителем всех этапов изготовления ванны, поскольку от этого зависит слаженность работы всех ее функциональных частей. Качественное долговечное оборудование - залог поддержания нормальных производственных процессов, бесперебойного выпуска товаров, отсутствия простоев и финансовых потерь. Именно поэтому выбору творожных ванн следует уделять особое внимание.
Преимущества отечественного оборудования для производства творога
Импортные установки проверены временем, долговечны, надежны в работе, но недешевы. Покупая их, вы несете соответствующие расходы на доставку, оформление таможенных документов, вынуждены ожидать значительное время, пока заказ приедет на объект.
Фальшивый творог
Зачем платить больше? Отечественное оборудование производства БСЗ - это надежные творожные ванны, изготовленные с соблюдением всех технических норм, надежные, качественные. Товар не только продается, но и доставляется на объект, монтируется, идет с гарантией. В процессе эксплуатации могут возникать разные ситуации, а потому гарантийное обслуживание и запасные части в наличии - не лишние условия.
Боровичский специализированный завод изготавливает творожные ванны и другое оборудование для обработки молока из нержавеющей стали. Это идеальный материал в плане соотношения цены и качества, долговечности, надежности, прочности. Готовые ванны служат минимум 10 лет, сталь не вступает в реакцию ни с молочными продуктами, ни с веществами, применяемыми для дезинфекции тары.
Преимущества творожных ванн производства Боровичского специализированного завода
БСЗ производит современное технологичное оборудование для производства творога высокого качества более 30-ти лет. Выбирая нашу продукцию, вы получаете:
1.Инновационное оборудование для пищевого производства, соответствующее передовым мировым стандартам.
2.Типовые и индивидуальные решения, готовые и под сборку.
3.Адекватную стоимость творожных ванн и остального оборудования.
4.Возможность покупки как отдельных установок, так и готовых к работе производственных линий.
5.Оперативное выполнение заказов и доставку во все регионы России, страны СНГ.
Все представленные в продаже творожные ванны прошли лицензирование и имеют необходимые сертификаты качества. Со специализированным оборудованием производства БСЗ вы можете укомплектовать свое производство с минимальными затратами. В штате специализированного завода работают грамотные мастера, которые окажут вам консультации по интересующим вопросам и выполнят работы на должном уровне. Благодаря солидному опыту работы и наличию передового технического оснащения БСЗ берется за выполнение заказов любой сложности. Нужны качественные творожные ванны по доступным ценам? Боровичский специализированный завод предложит широкий спектр решений для реализации бизнес задач, увеличения объемов производства и выхода на новый уровень.
Технологическая схема и обоснование режимов производства творога на механизированных линиях Я9-ОПТ и OBRAM
Технологический процесс производства творога на линии Я9-ОПТ:
Приемка и подготовка сырья.
Нормализация
Очистка 43+/-2С
Гомогенизация 55-65 С р=12,5+/-2,5 МПа
Пастеризация 78+/-2 С с выд.25-30 сек. , 90+/-2 С с выд.15+/-5 сек
Охлаждение до температуры заквашивания 28+/-2 С летом и 30+/-2 С зимой
Заквашивание
Сквашивание не более 10ч
Перемешивание сгустка
Нагревание, выдерживание и охлаждение творожного сгустка
Охлаждение творога
Расфасовка
На линии вырабатывается творог 5%,9% и нежирный.
Нормализацию проводят для 5% и 9% творога с учетом фактического содержания белка и коэффициента пересчета. Нормализованную смесь подогревают, очищают и затем гомогенизируют при 55-65°С, 12,5±2,5 МПа.
При выработки творога из гомогенизированного молока сгусток получается дряблый, плохо выделяется сыворотка. Для получения творога нужной влажности применяют термообработку сгустка. Нормализованное молоко пастеризуется при температуре 92±2°С. Пастеризованное молоко охлаждается до температуры заквашивания в летний период 24-28°С, в зимний период 26-30°С. Охлажденное молоко подают в емкости для сквашивания. Молоко заквашивают закваской на чистых культурах молочнокислых стрептококков, образующих в молоке в меру вязкий сгусток. Молоко с закваской перемешивается и оставляется в покое до сквашивания. Окончанием сквашивания считается образование сгустка кислотностью 75-95°Т- для творога 5 и 9%, и 80-100°Т для творога нежирного. Продолжительность сквашивания не должно превышать 10ч. Готовый сгусток перемешивают 3 мин и винтовым насосом подают в аппарат ТОС(теплообработник сгустка).ТОС состоит из трех секций: нагрева, выдерживания, охлаждения. Сгусток нагревают в секции нагрева до 48-54°С при выработке творога 9%, 46-52°С – 5%, 42-50°С – нежирного. Продолжительность подогрева 4-7мин. Из подогревателя сгусток поступает в секцию выдерживания, где находится 1,5-2мин. Из выдерживателя он направляется в секцию охлаждения, в которой охлаждается до 30-40°С при выработке творога 9 и 5%, до 25-30° — нежирного. Из секции охлаждения аппарата ТОС смесь поступает в устройство для обезвоживания, которое представляет собой вращающийся обезвоживатель барабанного типа, обтянутый фильтрующей тканью. Массовую долю влаги в твороге регулируют путем изменения угла наклона барабана обезвоживателя. Далее творог поступает в охладитель, где охлаждается до 8-12°С и подается на расфасовку.
Технологический процесс производства творога на линии OBRAM :
Приемка и подготовка сырья.
Нормализация
Очистка 43+/-2 С
Пастеризация 82+/-2 С 30 сек
Охлаждение до температуры заквашивания 25+/-2 С
Заквашивание
Сквашивание
Разрезка и нагревание сгустка 40+/-5 С 2ч
Отделение сыворотки
Формование
Прессование творога
Охлаждение 15+/-5С
Упаковка
Доохлаждение пр-та 4+/-2 С
Хранение и реализация
Нормализованное молоко пастеризуется при температуре 82±2°С, 20-30с. Смесь охлаждают до температуры сквашивания 25±2°С и направляют в коагулятор. В смесь вносится закваска, перемешивается 15мин и оставляется в покое до образования сгустка. Готовность сгустка определяют по достижении pН 4,5-4,7, сгусток должен обладать нежной, однородной, желеобразной консистенцией, без выделения сыворотки. Продолжительность сквашивания 12±2ч. Готовый сгусток вымешивают 10мин. Для ускорения отделения сыворотки сгусток нагревают до температуры 40±2°С- для творога нежирного, 42±2°С- для 5%, 44±2°С – для 7%, 46±2°С – для 9, 13%. Продолжительность нагревания не менее 2ч. Для равномерного нагревания сгусток периодически перемешивают. Сыворотку удаляют в количестве 60% от обьема смеси.
Технология производства творожных изделий
Творожный сгусток подается на формовочно-пресующее устройство, в котором образуются порции, соответствующие размеру и форме. Продолжительность прессования творога составляет 30-180сек. Отпресованный творог охлаждают до t=15+-5С и отправляют на упаковку. Упаковывают в термоусадочную пленку, после чего творог направляют в камеру хранения, с температурой 4±2°С. Срок хранения творога: при температуре 4±2°С, влажности 85%- 30сут.
Не нашли, что искали? Воспользуйтесь поиском.
По методу образования сгустка различают два способа производства творога: кислотный и сычужно-кислотный. Первый основывается только на кислотной коагуляции белков путем сквашивания молока молочнокислыми бактериями с последующим нагреванием сгустка для удаления излишней сыво -
Ротки. Таким способом изготовляется творог нежирный и пониженной жирности, так как при нагревании сгустка происходят значительные потери жира в сыворотку. Кроме того, этот способ обеспечивает выработку нежирного творога более нежной консистенции. Пространственная структура сгустков кислотной коагуляции белков менее прочная, формируется слабыми связями между мелкими частицами казеина и хуже выделяют сыворотку. Поэтому для интенсификации отделения сыворотки требуется подогрев сгустка.
При сычужно-кислотном способе свертывания молока cry сток формируется комбинированным воздействием сычужного фермента и молочной кислоты. Под действием сычужного фермента казеин на первой стадии переходит в параказеин, на второй - из параказеина образуется сгусток. Казеин при переходе в параказеин смещает изоэлектрическую точку с рН 4,6 до 5,2. Поэтому образование сгустка под действием сычужного фермента происходит быстрее, при более низкой кислотности, чем при осаждении белков молочной кислотой, полученный сгусток имеет меньшую кислотность, на 2-4 ч ускоряется технологический процесс. При сычужно-кислотной коагуляции кальциевые мостики, образующиеся между крупными частицами, обеспечивают высокую прочность сгустка. Такие сгустки лучше отделяют сыворотку, чем кислотные, так как в них быстрее происходит уплотнение пространственной структуры белка. Поэтому подогрев сгустка для интенсификации отделения сыворотки не требуется.
Сычужно-кислотным способом изготовляют жирный и полужирный творог, при котором уменьшается отход жира в сыворотку. При кислотном свертывании кальциевые соли отходят в сыворотку, а при сычужно-кислотном сохраняются в сгустке. Это необходимо учитывать при производстве творога для детей, которым необходим кальций для костеобразования.
В качестве сырья используют доброкачественное свежее молоко цельное и обезжиренное кислотностью не выше 20 °Т. По жиру молоко нормализуют с учетом содержания в нем белка (по белковому титру), что дает более точные результаты.
Нормализованное и очищенное молоко направляют на пастеризацию при 78-80°С с выдержкой 20-30 с. Температура пастеризации влияет на физико-химические свойства сгустка, что, в свою очередь, отражается на качестве и выходе готового продукта. Так, при низких температурах пастеризации сгусток получается недостаточно плотным, так как сывороточные белки практически полностью отходят в сыворотку, и выход творога снижается. С повышением температуры пастеризации увеличивается денатурация сывороточных белков, которые участвуют в образовании сгустка, повышая его прочность и
Усиливая влагоудерживающую способность. Это снижает интенсивность отделения сыворотки и увеличивает выход продукта. Путем регулирования режимов пастеризации и обработки сгустка, подбором штаммов заквасок можно получать сгустки с нужными реологическими и влагоудерживающими свойствами.
Г. Н. Мохно было предложено температуру пастеризации смеси для творога повысить до 90 °С, чтобы полностью осадить сывороточные белки и повысить выход творога на 20-25%; при этом не возникает трудностей при отделении сыворотки от сгустка.
Пастеризованное молоко охлаждают до температуры сквашивания (в теплое время года до 28-30, в холодное - до 30- 32 °С) и направляют в специальные ванны для выработки творога. Закваску для производства творога изготовляют на чистых культурах мезофильных молочнокислых стрептококков и вносят в молоко в количестве от 1 до 5%. Некоторые специалисты рекомендуют вводить в закваску Str. acetoinicus. Продолжительность сквашивания после внесения закваски составляет 6-8 ч.
При ускоренном способе сквашивания в молоко вносят 2,5% закваски, приготовленной на культурах мезофильного стрептококка, и 2,5% термофильного молочнокислого стрептококка. Температура сквашивания при ускоренном способе повышается в теплое время года до 35, в холодное - до 38 °С. Продолжительность сквашивания молока сокращается на 2- 3,5 ч, при этом выделение сыворотки из сгустка происходит более интенсивно.
Для улучшения качества творога желательно применять беспересадочный способ приготовления закваски на стерилизованном молоке, что позволяет снизить дозу внесения закваски до 0,8-1% при гарантированной ее чистоте.
При сычужно-кислотном способе производства творога после внесения закваски добавляют 40%-ный раствор хлорида кальция (из расчета 400 г безводной соли на 1 т молока), приготовленного на кипяченой и охлажденной до 40-45°С воде. Хлорид кальция восстанавливает способность пастеризованного молока образовывать под действием сычужного фермента плотный, хорошо отделяющий сыворотку сгусток. Немедленно после этого в молоко в виде 1 % - ного раствора вносят сычужный фермент или пепсин из расчета 1 г на 1 т молока. Сычужный фермент растворяют в кипяченой и охлажденной до 35 °С во - , де. Раствор пепсина с целью повышения его активности готовят на кислой осветленной сыворотке за 5-8 ч до использования. Для ускорения оборачиваемости творожных ванн молоко сквашивают до кислотности 32-35 °Т в резервуарах, а заТем перекачивают в творожные ванны и вносят хлорид Каль ция и фермент.
Готовность сгустка определяют по его кислотности (для жирного и полужирного творога должна быть 58-60, для нежирного - 75-80 °Т) и визуально-сгусток должен быть плотным, давать ровные гладкие края на изломе с выделением прозрачной зеленоватой сыворотки. Сквашивание при кислотном методе продолжается 6-8 ч, сычужно-кислотном - 4-6, с использованием активной кислотообразующей закваски- 3-4 ч. Важно правильно определить конец-сквашивания, так как при недосквашенном сгустке получается кислый творог мажущейся консистенции.
Чтобы ускорить выделение сыворотки, готовый сгусток разрезают специальными проволочными ножами на кубики с размером граней 2 см. При кислотном методе разрезанный сгусток подогревают до 36-38 °С для интенсификации выделения сыворотки и выдерживают 15-20 мин, после чего ее удаляют. При сычужно-кислотном - разрезанный сгусток без подогрева оставляют в покое на 40-60 мин для интенсивного выделения сыворотки.
Для дальнейшего отделения сыворотки сгусток подвергают самопрессованию и прессованию. Для этого его разливают в бязевые или лавсановые мешки по 7-9 кг (на 70% вместимости мешка), их завязывают и помещают несколькими рядами в пресс-тележку. Под воздействием собственной массы из сгустка выделяется сыворотка. Самопрессование происходит в цехе при температуре не выше 16 °С и продолжается не менее 1 ч. Окончание самопрессования определяется визуально, по поверхности сгустка, которая теряет блеск и становится матовой. Затем творог под давлением прессуют до готовности. В процессе прессования мешочки с творогом несколько раз встряхивают и перекладывают. Во избежание повышения кислотности прессование необходимо проводить в помещениях с температурой воздуха 3-6 °С, а по его окончании немедленно направлять творог на охлаждение до температуры не выше 8 °С с использованием охладителей различных конструкций; наиболее совершенным из них является двухцилиндровый.
Готовый продукт фасуют на автоматах в мелкую и крупную тару. Творог фасуют в чистые, пропаренные деревянные кадки или чистые алюминиевые, стальные, луженые широкогорлые фляги или картонные ящики с вкладышами из пергамента, полиэтиленовой пленки. В мелкую упаковку творог фасуют в виде брусков массой 0,25; 0,5 и 1 кг, завернутых в пергамент или целлофан, а также в картонные коробочки, пакеты, стаканы из различных полимерных материалов, упакованные в ящики массой нетто не более 20 кг.
Творог хранят до реализации не более 36 ч при температуре камеры не выше 8 °С и влажности 80-85%. Если срок хранения будет превышен из-за непрекращающихся ферментативных процессов, в твороге начинают развиваться пороки.
Творогоизготовители с прессующей ванной используют для выработки всех видов творога, при этом трудоемкий процесс прессования творога в мешочках исключается.
Творогоизготовитель состоит из двух двухстенных ванн вместимостью 2000 л с краном для спуска сыворотки и люком для выгрузки творога. Над ваннами закреплены прессующие ванны с перфорированными стенками, на которые натягивают фильтрующую ткань. Прессующая ванна при помощи гидравлического привода может подниматься вверх или опускаться вниз почти до дна ванны для сквашивания.
Соответственно подготовленное молоко поступает в ванны.
Здесь в него вносят закваску, растворы хлорида кальция и сычужного фермента и так же, как и при обычном способе выработки творога, оставляют для сквашивания. Готовый cry сток разрезают ножами, входящими в комплект творогоизготовители, и выдерживают в течение 30-40 мин. За это врем* выделяется значительное количество сыворотки, которую уда ляют из ванны отборником (перфорированный цилиндр, обтя нутый фильтрующей тканью). В его нижней части есть патрубок, вдвигающийся в патрубок ванны. Отделившаяся сыворотка через фильтрующую ткань и перфорированную поверхность поступает в отборник и по патрубку выходит из ванны. Такое предварительное удаление сыворотки повышает эффективность прессования сгустка.
Для прессования перфорированную ванну быстро опускают вниз до соприкосновения с поверхностью сгустка. Скорость погружения прессующей ванны в сгусток устанавливают в зависимости от его качества и вида вырабатываемого творога. Отделившаяся сыворотка проходит через фильтрующую ткань и перфорированную поверхность и собирается внутри прессующей ванны, откуда ее каждые 15-20 мин откачивают насосом.
Движение прессующей ванны вниз прекращается нижним конечным выключателем, когда между поверхностями ванн остается пространство, заполненное отпрессованным творогом. Расстояние это устанавливают при опытных выработках творога. В зависимости от вида вырабатываемого творога продолжительность прессования составляет 3-4 ч для жирного творога, 2-3 ч для полужирного, 1-1,5 ч для нежирного. При ускоренном методе сквашивания продолжительность прессования жирного и полужирного творога сокращается на 1-1,5 ч.
По окончании прессования перфорированную ванну поднимают, а творог выгружают через люк в тележки. Тележка с творогом подается подъемником наверх и опрокидывается над бункером охладителя, откуда охлажденный творог поступает на фасование.
Механизированная линия Я9-ОПТ-5 производительностью по молоку 5000 л/ч наиболее совершенна и используется для выработки полужирного, «Крестьянского» и нежирного творога. Готовый сгусток перемешивается в течение 2-5 мин и винтовым насосом подается в прямоточный подогреватель с рубашкой. Здесь сгусток быстро (4,5-7 мин) подогревается до температуры 42-54 °С (в зависимости от вида творога) подачей горячей воды (70-90 °С) в рубашку. Подогретый сгусток охлаждается до 8-12 °С в охладителе водой (25-40 °С) и направляется в двухцилиндровый обезвоживатель, обтянутый фильтрующей тканью. Содержание влаги в готовом твороге регулируется изменением угла наклона барабана обезвожива - теля или изменением температуры нагрева и охлаждения сгустка.
Готовый творог направляется на фасование и затем в холодильную камеру для доохлаждения.
С целью резервирования творога в весенний и летний периоды года его замораживают. Качество размороженного творога зависит от метода замораживания. Творог при медленном замораживании приобретает крупитчатую и рассыпчатую консистенцию вследствие замораживания влаги в виде крупных кристаллов льда. При быстром замораживании влага одновременно замерзает в виде мелких кристаллов во всей массе творога, которые не разрушают его структуру, и после размораживания восстанавливаются первоначальные, свойственные ему консистенция и структура. Наблюдается даже устранение после размораживания нежелательной крупитчатой консистенции вследствие разрушения крупинок творога мелкими кристаллами льда. Замораживают творог в фасованном виде - блоками по 7-10 кг и брикетами по 0,5 кг при температуре от -25 до -30 °С в термоизолированных морозильных камерах непрерывного действия до температуры в центре блока -18 и -25°С в течение 1,5-3 ч. Замороженные блоки укладывают в картонные ящики и хранят при этих же температурах в течение соответственно 8 и 12 мес. Размораживание творога проводят при температуре не выше 20°С в течение 12 ч.
ПРОИЗВОДСТВО ТВОРОГА РАЗДЕЛЬНЫМ СПОСОБОМ
При этом способе производства (рис. 8) молоко, предназначенное для выработки творога, подогревают в пластинчатом аппарате до 40-45°С и сепарируют с получением сливок с массовой долей жира не менее 50-55%. Сливки пастеризу-
Сладки Сыворотка
Закіасна Тіорог
Рис. 8. Схема поточной линии творога раздельным способом:
/ и 7 -емкости; 2 - иасос для молока; 3 - пластинчатый пастеризатор; 4 - сепаратор- сливкоотделитель; 5-насос для сливок; 6 - пластинчатый пастеризатор-охладитель для сливок; 8- дозирующий насос; 9-заквасочник; 10 - емкостный аппарат для сквашивания; // -мембранный насос; 12- пластинчатый теплообменник; 13 - сепаратор-творого - отделитель; 14 - приемник; 15 - насос для творога; 16 - охладитель для творога; 17 - смеситель
Ют в пластинчатой пастеризационно-охладительной установке при 90°С, охлаждают до 2-4 °С и направляют на временное хранение.
Обезжиренное молоко пастеризуют при 78-80 °С с выдержкой 20 с, охлаждают до 30-34°С и направляют в резервуар для сквашивания, снабженный специальной мешалкой. Сюда же подаются закваска, хлорид кальция и фермент, смесь тщательно перемешивают и оставляют для сквашивания до кислотности сгустка 90-100°Т, так как при сепарировании сгустка с меньшей кислотностью сопла сепаратора могут засориться.
Полученный сгусток тщательно перемешивается и насосом подается в пластинчатый теплообменник, где вначале подогревается до 60-62 °С, а затем охлаждается до 28-32 °С, благодаря чему он лучше разделяется на белковую часть и сыворотку. Из теплообменника сгусток под давлением подается в сепаратор-творогоизготовитель, где разделяется на сыворотку и творог.
При выработке жирного творога обезвоживание сепарированием проводят до массовой доли влаги в сгустке 75-76%, а при выработке полужирного творога - до массовой доли влаги 78-79%. Полученную творожную массу охлаждают на пластинчатом охладителе до 8 °С, растирают на вальцовке до
Получения гомогенной консистенции. Охлажденный творог направляют в месильную машину, куда дозирующим насосом подаются пастеризованные охлажденные сливки, все тщательно перемешивается. Готовый творог фасуют на автоматах и направляют в камеру для хранения.
По изложенной технологии получают жирный, полужирный, «Крестьянский», мягкий диетический, мягкий диетический пло - дово-ягодный творог.
Мягкий диетический творог вырабатывают путем сквашивания пастеризованного (85-90 °С) обезжиренного молока чистыми культурами молочнокислых стрептококков с удалением части сыворотки сепарированием с последующим добавлением к нежирному творогу сливок. Для этого в пастеризованное и охлажденное до 28-34 °С обезжиренное молоко вносят при перемешивании закваску, хлорид кальция и раствор сычужного фермента (1-1,2 г/т). Смесь сквашивают до кислотности сгустка 90- 110°Т (рН 4,3-4,5) или до 85-90°Т (сквашивание ускоренным методом). Готовый сгусток тщательно перемешивается мешалкой (5-10 мин) и с помощью насоса направляется в пластинчатый теплообменник, где он сначала нагревается до 60-62 °С для лучшего отделения сыворотки, а затем охлаждается до 28-32 °С. Далее сгусток дробится с помощью сетчатого фильтра и поступает на сепаратор-творого - изготовитель для получения нежирного творога.
Полученный творог насосом подаетея сначала на трубчатый охладитель, где охлаждается до 8 °С и подается на смеситель - дозатор для смешивания с пастеризованными (85-90 °С с выдержкой 15-20 с) и охлажденными (до 10-17°С) сливками с массовой долей жира 50-55%
Мягкий диетический творог должен содержать массовую долю жира не менее 11%, влаги 73%: кислотность его должна быть не выше 210 °Т. Творог должен иметь чистый кисломолочный вкус, нежную однородную консистенцию, слегка мажущуюся, белый с кремовым оттенком цвет, равномерный IIO всей массе.
Мягкий диетический плодово-ягодный творог вырабатывается с сиропами, которые предварительно тщательно смешиваются в отдельной емкости со сливками и подаются в Смеситель - дозатор для смешивания с творогом. Вырабатывают и нежирный мягкий диетический плодово-ягодный творог.
Готовый продукт фасуют на автомате в коробки, стаканчики или пакеты из полимерных материалов, которые затем укладывают в ящики и направляют в холодильную камеру на хранение при температуре 2 °С.
Срок реализации продукта не более 36 ч с момента выработки при температуре не выше 8 °С»
Домашний сыр изготовляется жирный (4% жира) и нежирный. Он представляет собой сырную массу из отдельных зерен белого (для жирного) со слегка желтоватым оттенком цвета. Вкус продукта нежный, слегка солоноватый, запах кисломолочный. Массовая доля жира в домашнем сыре составляет 4,3 и 20%, нежирном - 0,4, соли не более 1, влаги не более 78,3 и 79% соответственно; кислотность продукта не выше 150 °Т. Для его выработки используют обезжиренное молоко с кислотностью не выше 19 °Т и сливки с массовой долей жира 30% и кислотностью не выше 17°Т.
Сливки предварительно пастеризуют при 95-97 °С с выдержкой 30 мин (для придания привкуса пастеризации), гомогенизируют при температуре 26-30°С и давлении 12,5- 13 МПа, после чего охлаждают до 4-8 °С. Обезжиренное молоко пастеризуют при 75 °С с выдержкой 18-20 с, охлаждают до 30-32 °С и заквашивают в ванне. В состав закваски входят Str. lactis, Str. diacetilactis, Str. cremoris в соотношении 2:1; : 2. Если закваску вносят в количестве 5-8%, сквашивание продолжается 6-8 ч, если в количестве 1-3%, то 12-16 ч при температуре 21-23 °С. Кроме закваски, в молоко вносят хлорид кальция в виде раствора (400 г безводной соли на 1 т молока) и 1%-ный раствор сычужного фермента (1 г на 1 т молока).
Готовность сгустка определяют по кислотности сыворотки, которая должна быть 45-57°Т (рН 4,7-4,9), и прочности сгустка. Готовый сгусток разрезают проволочными ножами на кубики с размером ребра 12,5-14,5 мм и оставляют в покое иа 20-30 мин. В процессе выдержки возрастает кислотность, лучше отделяется сыворотка и уплотняется (обсыхает) сгусток. После этрго для снижения кислотности сыворотки до 36-40°Т в ванну добавляют воду (при 46 °С) с таким расчетом, чтобы уровень в ванне повысился на 50 мм, сгусток подогревают, вводя в рубашку ванны горячую воду. Подогрев ведут так, чтобы вначале температура сгустка повышалась со скоростью 1 °С за 10 мин, затем до поднятия температуры 48-55°С - 1 °С за 2 мин. Кислотность сгустка во время нагревания не должна повышаться более чем на 3°Т (т. е. до 39-43°Т), По достижении температуры 48-55°Т творожное зерно с целью его уплотнения вымешивают в течение 30-60 мин. Готовность зерна определяют пробой на сжатие: при легком сжатии в руке оно должно сохранять свою форму и не разминаться.
Когда творожное зерно готово, из ванны удаляют сыворот-1 ку и наливают в нее воду температурой 16-17°С, в которой зерно промывают, охлаждая в течение 15-20 мин. Затем его промывают холодной водой (2-4°С). "Объем воды должен быть равен объему удаленной сыворотки. Затем воду спускают, й зерно сдвигают к стенкам ванны так, чтобы на середине образовался желоб для стекания сыворотки. К обсушенному зерну (массовая доля влаги не более 80%) добавляют наполнители и тщательно перемешивают. Соль предварительно растворяют в 8-10-кратном количестве сливок. Готовый Домашний сыр фасуют в мелкую тару - коробки, рассчитанные на 500 г, картонные стаканы с полимерным покрытием и полимерные стаканы на 200, 250 и 500 г, а также в широкогорлые фляги и картонные коробки с прокладкой из бумаги и полимерным покрытием, рассчитанные на 20 кг.
Сроки реализации Домашнего сыра: при комнатной температуре не более 24 ч, при 8-10 °С не более 5 сут, а при 2- 4 °С не более 7 сут.
Домашний творог предпочитают все, кто понимает разницу между качественными продуктами и их имитацией. Если вы живете в деревне, этот бизнес для вас, хотя организовать производство можно и в городе. Технология не очень сложная, успех обеспечен при налаженном сбыте.
Планировать бизнес по изготовлению домашнего творога лучше всего в деревне, хотя вполне возможно наладить его и в городских условиях. Технология производства творога не сложная и не затратная.
Чтобы изготовить творог в домашних условиях, достаточно иметь чистую кухню, молоко, сметану и кастрюлю.
Рецепт приготовления очень прост: молоко кипятят, когда оно остынет до 30 градусов, кладут в него сметану из расчета 100 грамм на 2 литра молока и ставят в теплое место на девять часов.
После массу выкладывают в чистую марлю, отжимают и подвешивают для удаления сыворотки. В этом рецепте нужно соблюсти важное условие – качественное сырье.
Если вы находитесь в деревне, найти такое молоко не составит труда, для жителей города это тоже вполне возможно, хоть и сопряжено с некоторыми сложностями. Сбыт готового творога нужно налаживать через предприятия общественного питания и поставлять его постоянным покупателям.
Если вы задумываетесь об открытии бизнеса более крупного, задачи несколько сложнее.
У творога широкий спектр разновидностей:
- собственно творог разной жирности, от обезжиренного до жирного;
- продукты из творога– торты, сырки, кремы, пасты. Эти продукты разнообразят добавками – шоколадными, фруктовыми, овощными и прочими.
Реализация
Основными потребителями творога и его производных являются покупатели розничных магазинов всех возрастных категорий и предприятия общественного питания (кафе, рестораны и т. п.).
Реализовать готовый продукт можно через:
- розничную сеть (магазины, супермаркеты);
- оптовых покупателей, занимающихся посредничеством;
- предприятия, использующие творог для приготовления изделий из него.
- сектор HoReCa (рестораны , кафе , столовые, кулинарии).
Основное внимание следует обратить на первые два канала сбыта. Поставки в торговую сеть позволят извлечь больше прибыли и наладить регулярный сбыт, а сотрудничество с оптовиками гарантирует стабильные объемы продаж при более низкой цене. В этом случае отпадает необходимость хранить готовую продукцию.
Технология и оборудование
Технологический процесс заключается в сквашивании пастеризованного молока с применением молочнокислых бактерий. Возможно также применение сычужного фермента или хлористого кальция.
Изготовление творога можно разделить на такие этапы:
- Прием молока и его фильтрация;
- Пастеризация молока в электропастеризаторе;
- Охлаждение молока и его сквашивание. Устранение сгустков (ванны);
- Прессование (с применением пресс-тележки). Возможно прессование в мешках, в барабанах для прессования и охлаждения творога;
- Автоматическая расфасовка.
Для обеспечения этого процесса понадобится такое оборудование:
- Станция для приема и фильтрации;
- Электропастеризатор;
- Творожная ванна;
- Пресс-тележка (дешевле) или установка барабанного типа (практичнее);
- Автомат для фасовки.
Рассмотрим два варианта налаженного производства по изготовлению творога.
1-й вариант. Экономичный
Производительность - 130 кг/ч.
В состав линии входят:
- Ванна для пастеризации, рабочий объем 50 л, цена - 230 тыс. руб.;
- Ванна творожная, объем 1,25 куб. м – 13,5 тыс. руб.;
- Пресс-тележка – 98 тыс. руб.;
- Станция приема и учета сырья производительностью 5 000 литров в час - 348 тыс. руб.;
- Дополнительное оборудование (узлы соединения, насосы, мойки и т. п.) – 100 тыс. руб.
Всего – 911 тыс. руб.
2-ой вариант. Стандартный
Производительность -130 кг/ ч.
- Станция приема и учета сырья, объем 5 000 литров в час - 348 тыс. руб.;
- Установка для прессования и охлаждения производительность 130 кг/час – 249 тыс./руб.;
- Пастеризатор электрический на 1000 литров – 605 тыс. руб.;
- Дополнительное оборудование - 100 тыс. руб.
Всего – 130,2 тыс. руб.
Кроме этого оборудования понадобится:
- Автоматический фасовщик и упаковщик - 885 тыс. руб.;
- Холодильная камера = 117,8 тыс. руб.
Видим, что экономичная линия обойдется в 1,9 млн. руб., а стандартная - в 2,3 млн. руб.
Для работы на экономичной линии нужны 7 человек, на стандартной – 4 человека.
Стандартная линия полностью автоматизирована и не потребует больших трудозатрат. В результате себестоимость продукта с этой линии ниже, чем с линии экономичной, что позволит снизить отпускные цены на творог и завоевать тем самым популярность у покупателей.
Финансовые вложения
- Оборудование - 2,3 млн. руб.;
- Доставка, монтаж, и наладка оборудования - 0,3 млн. руб.;
- Сырье - 1 млн. руб.;
- Подготовка производственного помещения – 0,5 млн. руб.;
- Регистрация предприятия, открытие счета, подобные расходы - 0,1 млн. руб.
Всего: 4,2 млн. руб.
Выручка и прибыльность
- Готовый продукт, кг/час- 90;
- Продолжительность смены, час. -12;
- Кол-во смен в месяц – 30;
- Выработка в месяц, кг – 16 200
- Оптовая цена 1 кг, руб. – 120;
- Выручка в руб. – 1 940 000 руб.;
- Прибыль, руб. – 250 000 руб.
Инвестиции окупятся через 18-24 месяца.